Machbarkeitsstudie zeigt Potenziale von industriellem 3D-Druck in der Bahnbranche auf.
Gerade auch für die Schienenfahrzeugbranche öffnet der industrielle 3D-Druck interessante neue Optionen. Aktuell klärt eine Machbarkeitsstudie, inwieweit das Fertigungsverfahren für die Herstellung von Steuerungstafeln von Sandungssystemen einsetzbar ist. Die Ergebnisse sind vielversprechend, jedoch stellt die derzeit noch fehlende 3D-Druck-Prozesszulassung ein Hindernis für den umfangreichen Einsatz in der Produktion dar.
Kontakt
80809 München
Deutschland
carina.smid@knorr-bremse.com
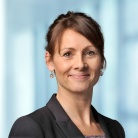
Neue Potenziale durch fortschreitende Entwicklung von industriellem 3D-Druck
Geht es um die Subsysteme neuer Schienenfahrzeuge, sind die bestimmenden Anforderungen klar umrissen: Fahrzeugbauer verlangen nach maximaler Flexibilität bei der Fahrzeugintegration, nach immer kürzeren Times-to-Market sowie geringstmöglichen Kosten und Gewicht. Die Eckpunkte in Einklang zu bringen, kommt allerdings bislang noch oft der sprichwörtlichen Quadratur des Kreises nahe. Die fortschreitende Entwicklung von industriellem 3D-Druck öffnet jedoch Potenziale, ihr zumindest sehr nahe zu kommen.
Bei Knorr-Bremse Systeme für Schienenfahrzeuge läuft deshalb aktuell eine Machbarkeitsstudie, ob – und wenn ja, wie – sich die Technologie bei der Herstellung von Steuerungstafeln von Sandungssystemen nutzen lassen könnte. Neben der Potential-Evaluierung ist die Analyse von potenziellen Hindernissen bei der Industrialisierung des Fertigungsverfahrens im Bremssystemumfeld das Ziel.
Aufbau und Funktionsweise der Sandungssystem-Steuerungstafeln
Steuerungsmodule von Sandungssystemen kombinieren pneumatische und elektropneumatische Komponenten auf einem Trägersystem, das üblicherweise eine Aluminiumtafel darstellt. Zahlreiche Bohrungen und Luftkanäle verbinden die Geräte untereinander. Über den Druckluftanschluss wird das Modul versorgt. Das Druckminderventil reduziert diesen Luftdruck auf den erforderlichen Arbeitsdruck. Zwei Magnetventile steuern den Zufluss der Druckluft an die Sandungseinheit, ein Kontrollstutzen dient als Messpunkt.
Zusammenfassung
Im Rahmen einer 3D-Druck-Machbarkeitsstudie konstruierte Knorr-Bremse einen neuartigen und deutlich leichteren sowie kompakteren Steuerungstafel-Funktionsträger für Sandungssysteme. Die mit dem neuen Bauteil durchgeführten Funktionstestsequenzen ergaben im Vergleich zu konventionell produzierten Tafeln nahezu deckungsgleiche Werte. Attraktive Einsatzszenarien sind zum Beispiel für die engen Einbauräume in Niederflurfahrzeugen oder in zukünftigen Hochgeschwindigkeitsanwendungen denkbar.
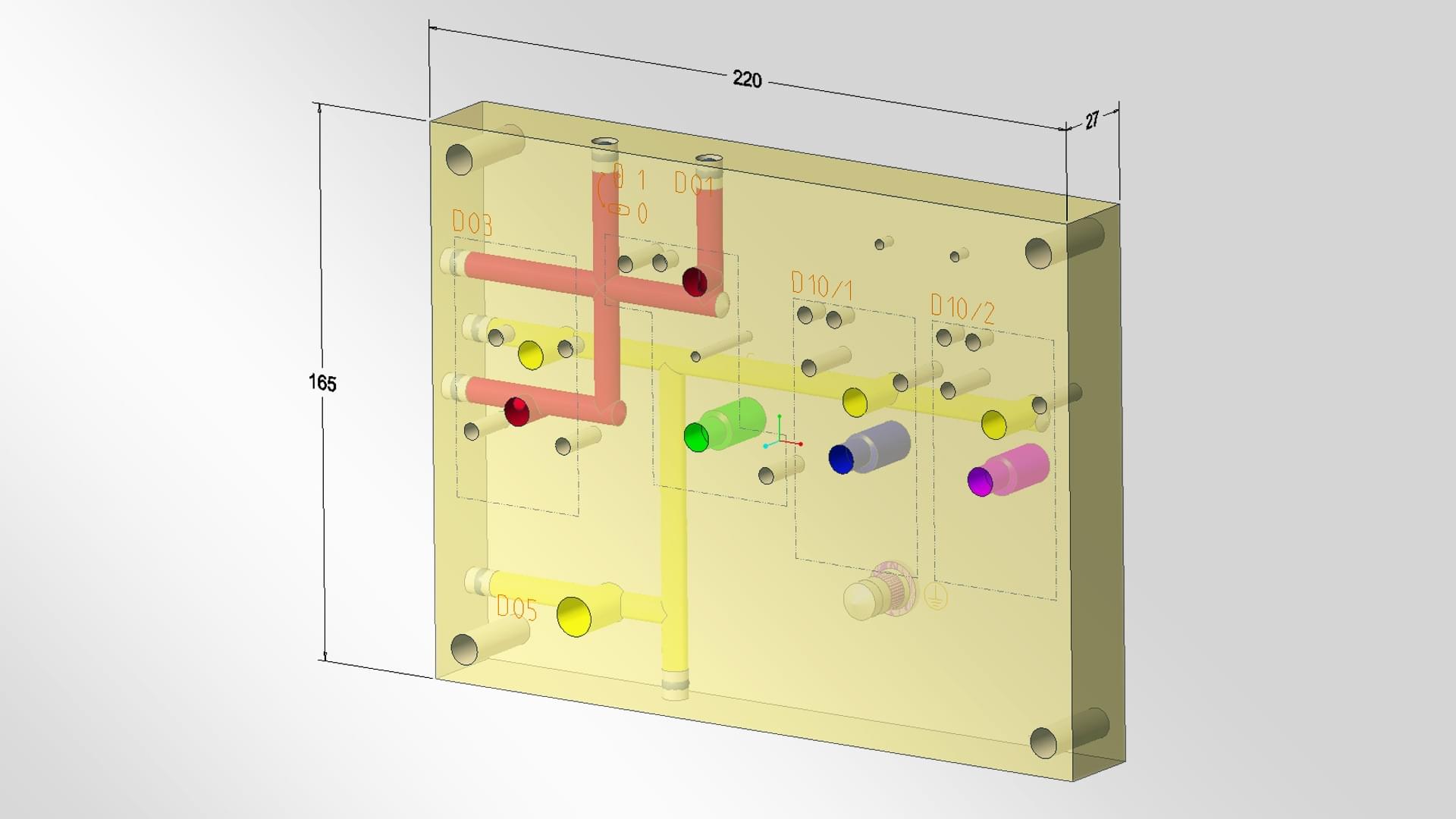
In einem typischen Anwendungsfall beläuft sich das Volumen des Aufbaus auf knapp 5.700 cm3, das Gewicht der Aluminiumtafel beträgt 2,53 kg. Das sperrige Design der Tafeln ist größtenteils von den Grenzen der spannenden Fertigungsverfahren Fräsen und Bohren bestimmt, sowie der Anordnung der Geräte in lediglich einer Ebene geschuldet.
Designmethodik vor dem Hintergrund des industriellen 3D-Drucks
Design-driven Manufacturing heißt das bestimmende Stichwort des industriellen 3D-Drucks, bei dem die Konstruktion die Fertigung bestimmt und nicht mehr die Fertigung die Konstruktion (Form follows Function). Die mit dem Verfahren einhergehenden neuen Freiheitsgrade im Design machen dabei die Fertigung von bislang praktisch nicht herstellbaren hochkomplexen Strukturen und filigranen Details möglich. Mit dem Einsatz des 3D-Drucks müsste sich folglich ein deutlich leichterer und kompakterer Steuerungstafel-Funktionsträger konstruieren lassen, so das Kalkül.
Anstelle der massiven Steuerungstafel sollten die Module lediglich noch an einem kompakten Gerüst angeordnet sein, das wiederum mit den jeweiligen Schnittstellen der Geräte ausgestattet ist. Nach verschiedenen Designvarianten stand deren optimale Position vor der Maxime eines möglichst kompakten Gerüsts fest. Damit einher ging zudem ein etwas adaptierter und verbesserter Anschlussverteiler.
Eine Besonderheit der gedruckten Version liegt auch darin, dass die Verrohrungen nicht zwangsläufig rund sein müssen. Bei gleichbleibender Querschnittsfläche kann die Form der Rohre in einem gewissen Rahmen variieren. So ließen sich im konkreten Fall etwa Kanäle nebeneinander „verlegen“, anstatt wie bisher auf unterschiedlichen Bauteilebenen. Um eine mechanische Bearbeitung– zum Beispiel der Gewindeverbindungen– zu ermöglichen, erhielt das Machbarkeitsstudiendesign einen ebenfalls 3D-gedruckten Versteifungsrahmen sowie zusätzliche Befestigungspunkte.
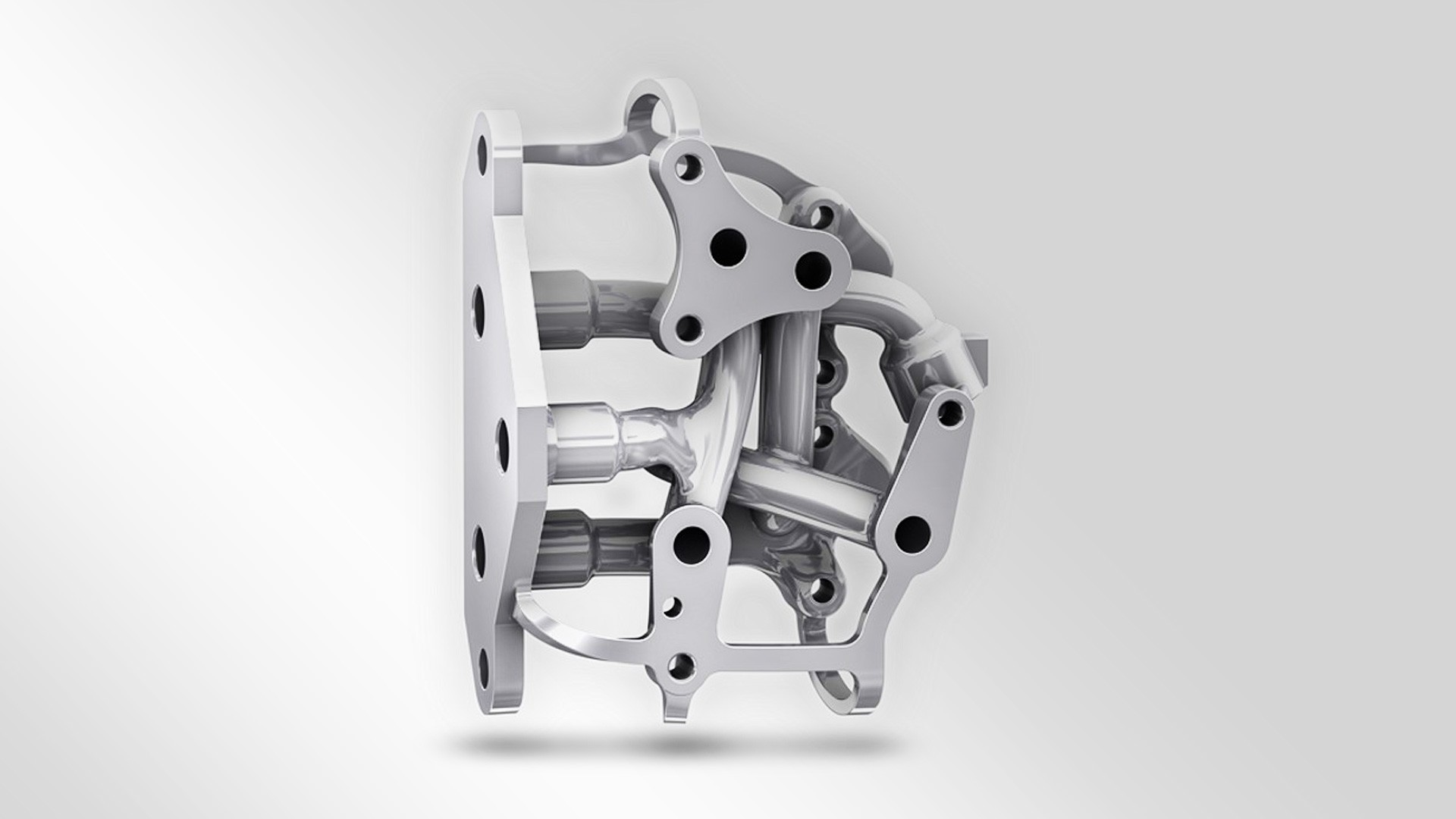
Technische Spezifikation der 3D-gedruckten Steuerungstafeln
Für den Versuchsträger waren im Wesentlichen die auch bei konventionellen Bremstafeln geltenden Maßgaben zu erfüllen: Die Pneumatik-Funktionalitäten hatten der Performance der konventionellen Steuertafel zu entsprechen. Der Aufbau musste mit den baulichen Anforderungen der EN12663 (Kategorie L) sowie den mechanischen Anforderungen nach EN 61373 (Kategorie 1, Klasse B) übereinstimmen. Die Konstruktion hatte gemäß DIN EN ISO 9227 einen 720-Stunden-Salzsprühtest zu bestehen. Die niedrigste Eigenfrequenz aller Geräte musste mindestens 30 Hz betragen und in den Verrohrungen durften sich keine Wassertaschen bilden. Vor der Fertigung validierten die Ingenieure die Konstruktion mit FE-Analysen für statisches und dynamisches Bauteilverhalten.
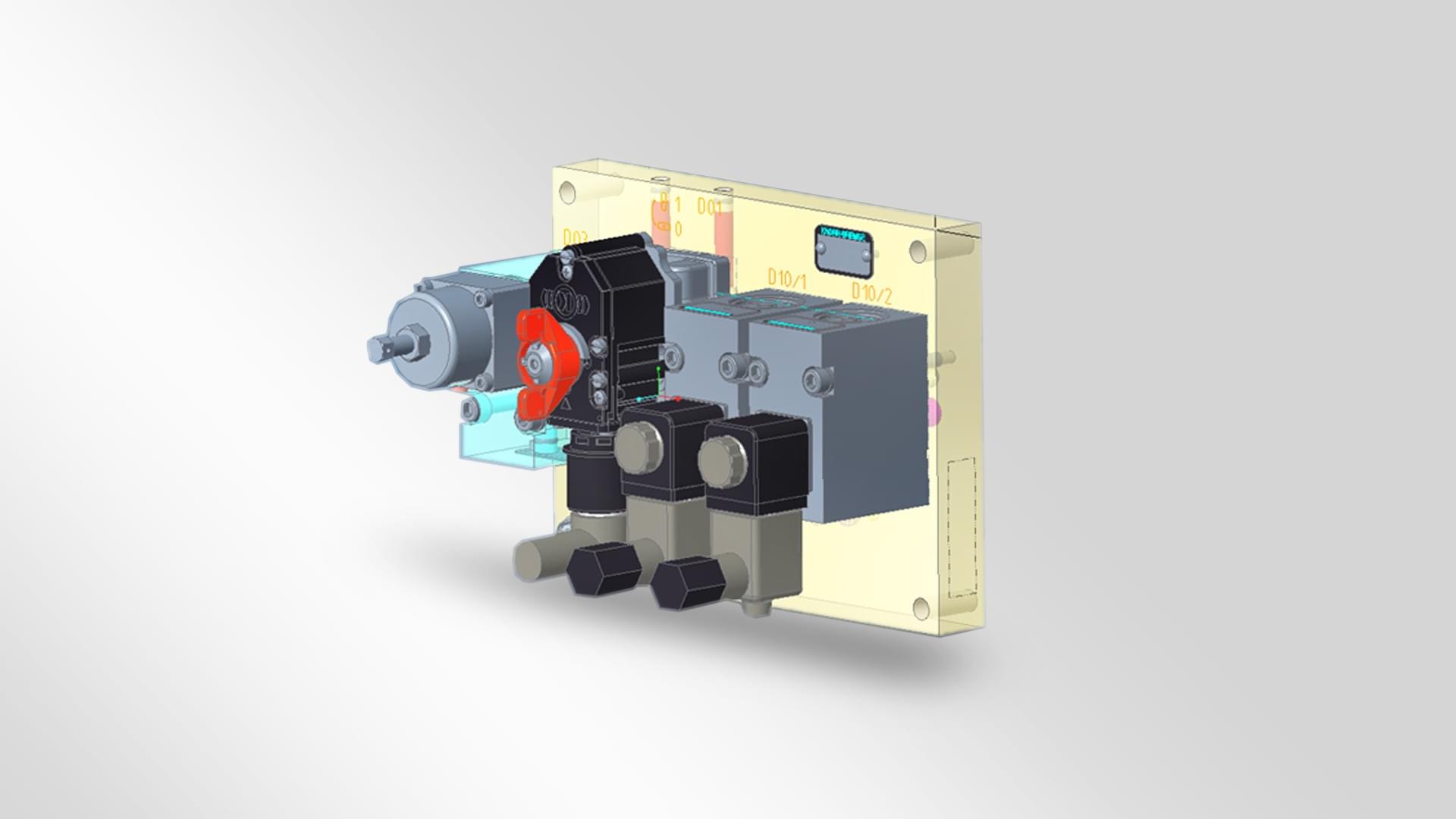
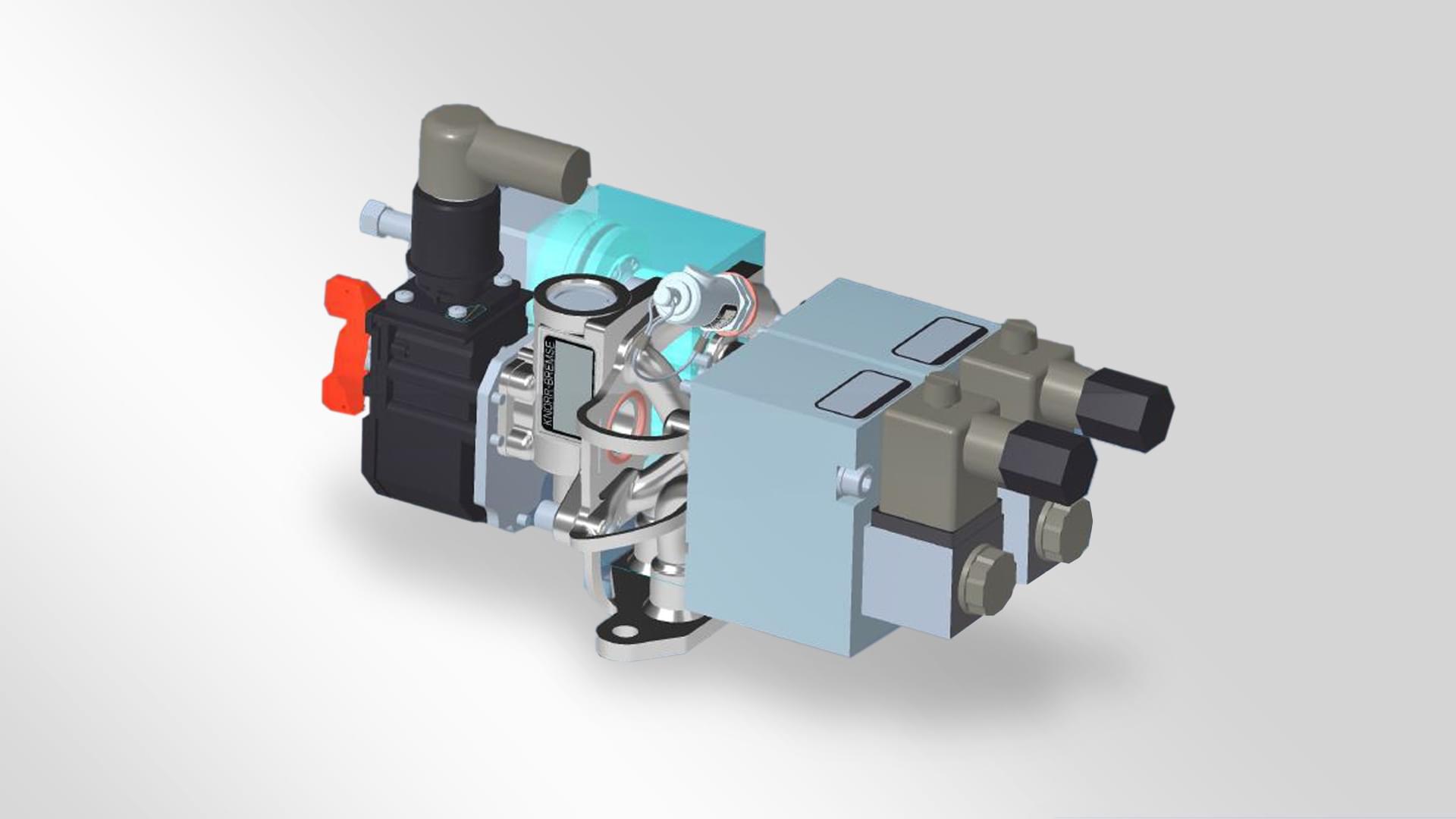
Direct Metal Laser Sintering (DMLS)
Beim Produktionsverfahren fiel die Wahl auf das Direct Metal Laser Sintering (DMLS)-Verfahren mit einer Aluminiumlegierung als Ausgangswerkstoff. Ein starker Laser schmilzt nun das pulverförmige Ausgangsmaterial exakt an jenen Stellen zusammen, die ihm die computergenerierten Bauteil-Konstruktionsdaten vorgeben. Schicht für Schicht und in einer Dicke von 60 Mikrometern „wächst“ das Gerüst von unten nach oben.
Die reine Druckzeit des Machbarkeitsstudienaufbaus betrug 12 Stunden. Drei weitere Stunden stellten sich als realistisch für die zu veranschlagende Vor- und Nachbearbeitungszeit heraus. Letztere kommt zum Beispiel durch die Entfernung des – in einer geringeren Materialdichte mitgedruckten – Stützkorsetts zustande. Das Korsett ist nötig, um eine Verformung des Aufbaus während des Druckprozesses durch sein steigendes Eigengewicht zu verhindern.
Belastungstests und Funktionalitätsprüfung
Am fertiggestellten Bauteil folgten die obligatorischen Belastungstests sowie die Überprüfung der Funktionalität. Angeschlossen an entsprechende Prüfinfrastruktur wurde allmählich der Druck erhöht und der Druckabfall gemessen. Danach erfolgte der Luftdichtheitstest in einer Wasserwanne. Mit 13 bar lag der Druck dabei etwa ein Drittel oberhalb des maximalen Betriebsdrucks von 10 bar. Sämtliche gemessenen Werte lagen innerhalb der Toleranzen, die auch für die konventionelle Steuertafeln maßgeblich sind. Die Shock-and-Vibration-Tests gemäß IEC 61373:1999-01 (Kategorie 1, Klasse B) bestand das Gerüst ebenfalls problemlos – wodurch sich die früheren Annahmen aus der FE-Berechnung als validiert betrachtet werden können.
Montiert an gängigem Serienequipment durchlief die Tafel sämtliche Funktionstestsequenzen, mit denen auch die Funktionalität der konventionell gefertigten Tafeln vor der Auslieferung überprüft wird. Dass die Messwerte bereits beim ersten Aufbau der Machbarkeitsstudie nahezu deckungsgleich mit den an konventionellen Tafeln gemessenen Werten waren, lag über den Erwartungen.
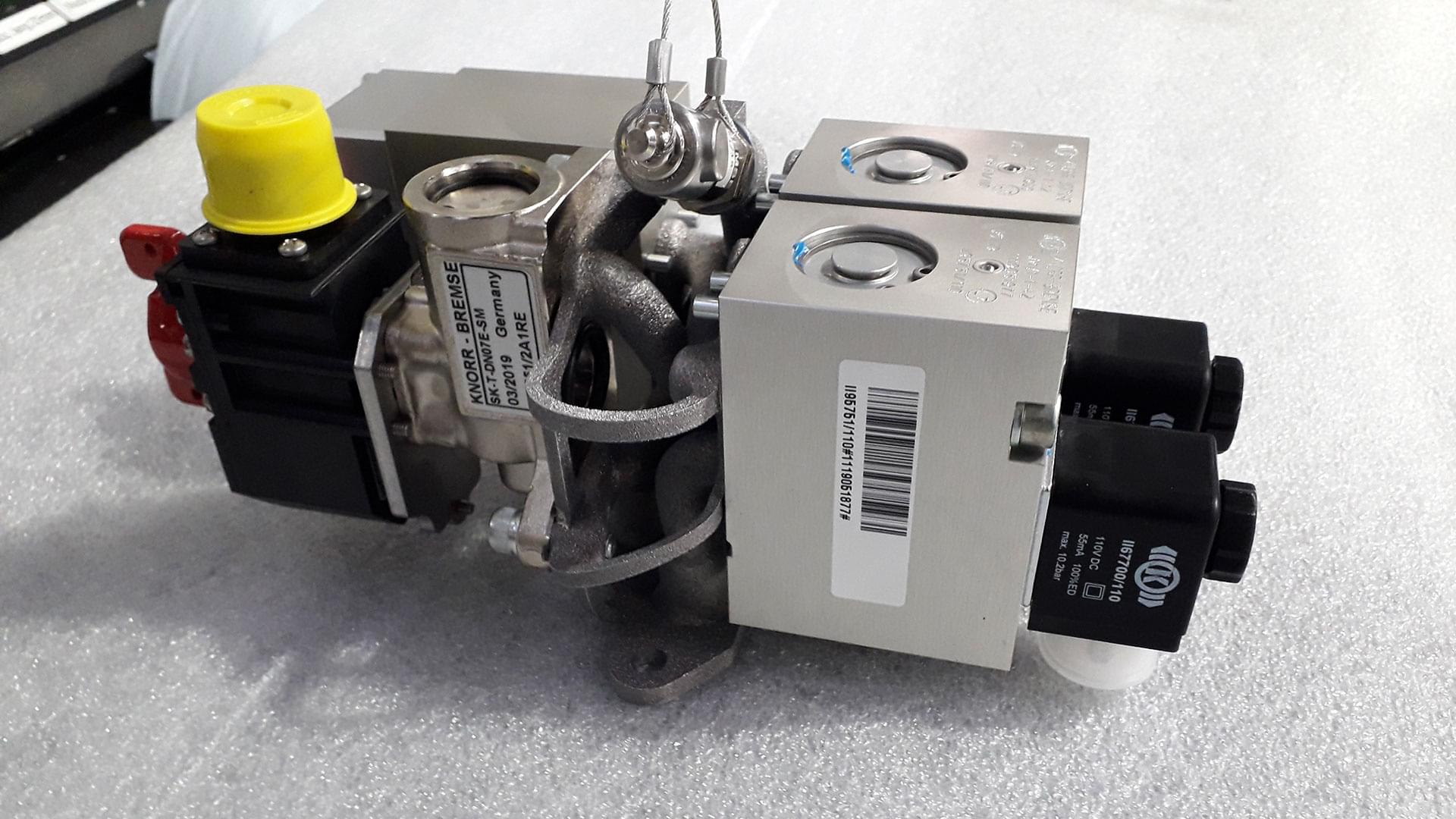
Umfangreicher 3D-Druck-Einsatz setzt Prozesszulassung voraus
Die vorangegangenen Simulationsergebnisse sowie die Bauteil- und Funktionstests weisen klar darauf hin, dass das Verfahren grundsätzlich zur Herstellung der Schalttafeln geeignet ist. Natürlich wären vor dem umfassenden Einstieg in die Serienfertigung noch zahlreiche weitere Testreihen nötig, etwa, was die Optimierung des Druckprozesses angeht.
Der Mehrwert einer 3D-gedruckten Steuertafel ist auch über die neuen Freiheitsgrade für die Bauteilkonstruktion hinaus zweifellos vorhanden: Im Vergleich zur konventionellen Aluminiumtafel beträgt die Gewichtsersparnis bis zu 90 Prozent. Zudem ermöglicht das Gerüst eine deutlich kompaktere Anordnung der Gerätschaften. Attraktive Einsatzszenarien sind zum Beispiel für die engen Einbauräume in Niederflurfahrzeugen oder in zukünftigen Hochgeschwindigkeitsanwendungen denkbar.
Ein Hindernis für den umfangreichen Einsatz der Technologie in der (Serien-)Fertigung stellt allerdings die aktuell noch fehlende Prozesszulassung für 3D-Druckverfahren in der Bahnindustrie dar. Nötig sind zum einen noch Regelwerke zum standardisierten Vorgehen für die Zulassung additiv hergestellter Bauteile. Zum anderen weisen einige der Einflussfaktoren im Druckprozess noch nicht den für eine industrielle (Serien-)Fertigung erforderlichen Reifegrad auf. Somit müssen die Bauteileigenschaften aktuell für jeden spezifischen Anwendungsfall umfangreich validiert und abgesichert werden. Es laufen jedoch bereits zahlreiche Initiativen für den Aufbau eines entsprechenden Zulassungswegs in der Bahnindustrie und die Weiterentwicklung der additiven Fertigungstechnologien.
Autoren: Dr. Thomas Anton, Bernhard Winkler, Attila Kovács, Attila Metál