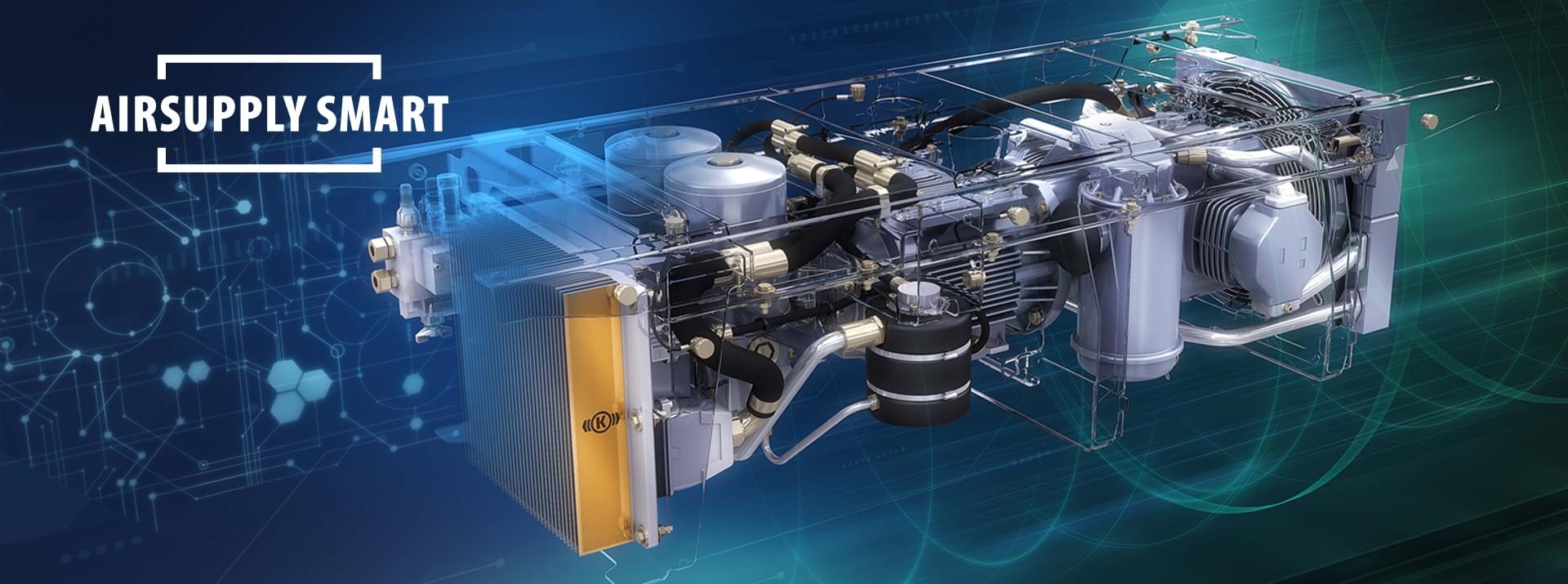
In trains, a compressed-air system provides the power needed to bring hundreds of tons of laden vehicles traveling at full speed safely to a standstill. Now Knorr-Bremse engineers have developed AirSupply Smart, a groundbreaking new way to manage air supplies that controls their energy consumption, noise emissions – and even digitizes them.
Air supply pipes weave their way through rail vehicles in a complex, wide-ranging web. Air compressors breathe life into this intricate network, which powers almost all of the train’s main functions – including braking and pneumatic suspension, entrance doors and steps, sanitary facilities, power collectors, windshield wipers, sand-scattering systems, and air horns.
For decades, train air supply systems operated in one of just two simple modes: “on” or “off”. A control system switched on the compressors whenever the air pressure in the compressed-air reservoirs fell below a certain threshold – and then switched them off again once the air pressure reached a certain value at the other end of the scale. The catch? The frequent starts and stops placed considerable strain on both compressor motors and air supply system, negatively impacting life-cycle costs for rail operators. And because the compressors always ran at full load while they were on, things very quickly became very noisy for people living near rail tracks or sidings.
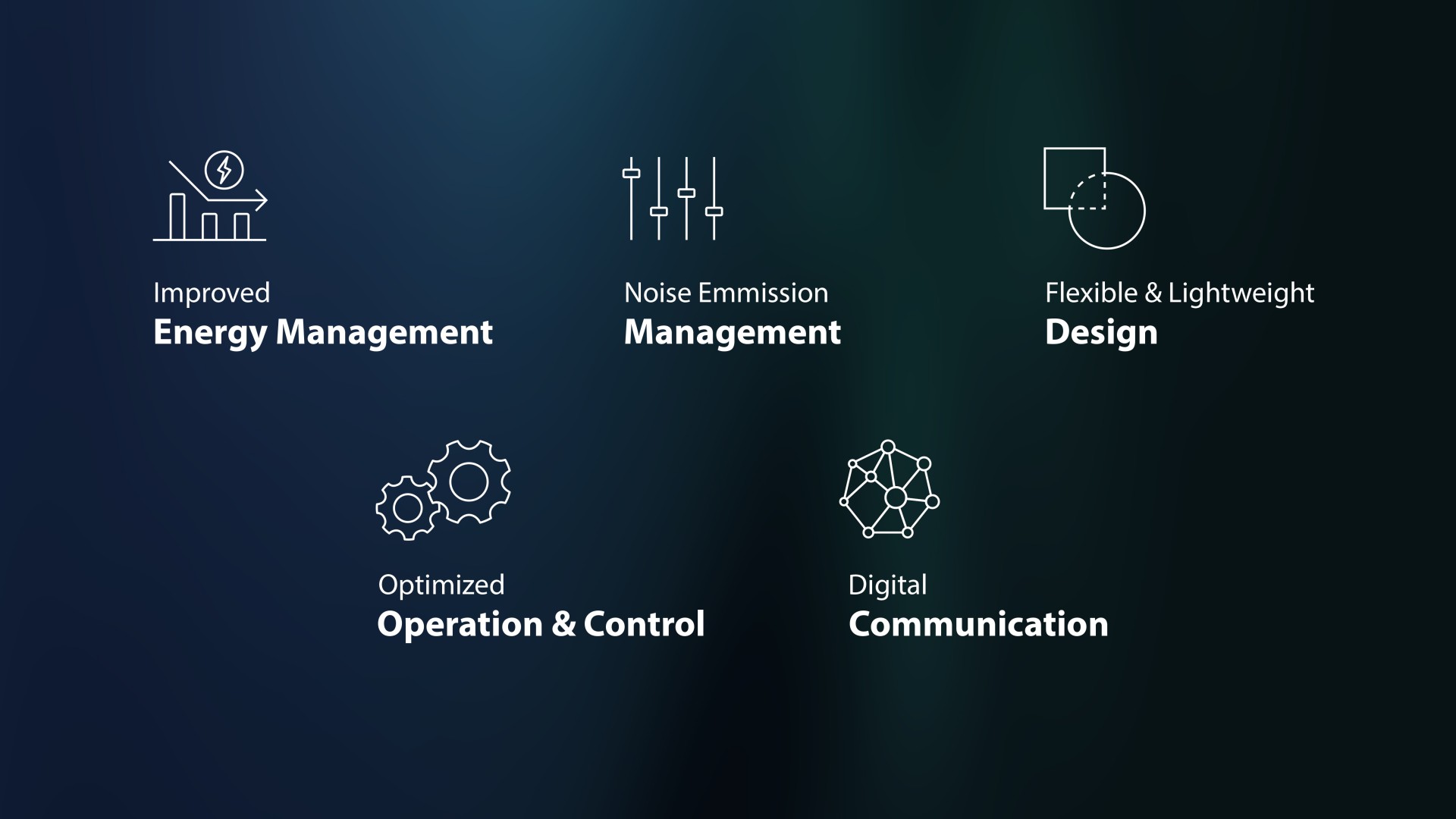
Optimized management and operation
AirSupply Smart represents a major paradigm shift – from a simple component business to demand-driven delivery of compressed air based on vehicle load, speed, braking operations, operating data and ambient conditions. The key component is a new frequency inverter, specially developed for the rail industry. Not only does it convert the power supplied by overhead lines to vehicle-specific voltages and frequencies – it also acts as the “brain” of the entire air supply system. AirSupply Smart is effectively a multifunctional platform, providing the prerequisites for a new, climate-compatible, eco-friendly energy and noise emission management system optimized for rail.
Managing noise emissions
Allaying the concerns of residents living near rail tracks is an important step in building up social acceptance of railroads. This is where AirSupply Smart’s “silent mode” comes in. Rail vehicles are often prepared for operation at night, while they are parked near residential areas or in stations. In such cases, the control system reduces the compressor’s operating speed, making it much quieter.
The impact of this silent mode on residents’ wellbeing is enormous, as the example of the VV120T oil-free compressor shows – smart adjustment of the compressor’s operating speed reduces noise output by up to 75 percent.
Improving energy management
The calculus behind this situational approach to compressor management also works the other way around. If the demand for air is particularly high – due, for example, to a large number of passengers disembarking simultaneously at a main station and the resulting self-adjustment of the pneumatic suspension – AirSupply Smart can switch over to “boost mode”. By boosting the airflow, the system avoids emptying the air reservoirs, which would otherwise cut off the train’s traction power. This in turn improves train availability and punctuality. Another plus point? Boost mode can also reduce the time required to prepare trains for operation.
Taking the additional output of “boost” mode into consideration, trains could now make do with smaller compressors. This would have a positive impact on vehicle weight and life-cycle costs. It would also give vehicle manufacturers more installation space to play with, most of which could be devoted to the actual air supply.
Lightweight, flexible design
Auxiliary air compressors are often used to raise trains’ power collectors (pantographs) into contact with overhead lines, but the new smart inverter makes them redundant. Thanks to reduced power consumption, the vehicle’s onboard battery is sufficient to power the main air compressor at least part of the time, so the latter can be used to raise the power collector instead. Removing the auxiliary air compressor reduces vehicle weight and simplifies vehicle configuration.
Fit for all things digital
AirSupply Smart is clearly designed to be future-proof. Not just because any new functions developed in the future will be easy to incorporate via software updates, but also because the AirSupply Smart sensors support comprehensive “condition monitoring”. By using algorithms to convert operating data and data on ambient conditions into status signals, the system effectively monitors itself. And because operators can supervise system status in real time, the risk of unexpected failure or downtime is enormously reduced – the availability of fleet vehicles rises while their life-cycle costs fall.