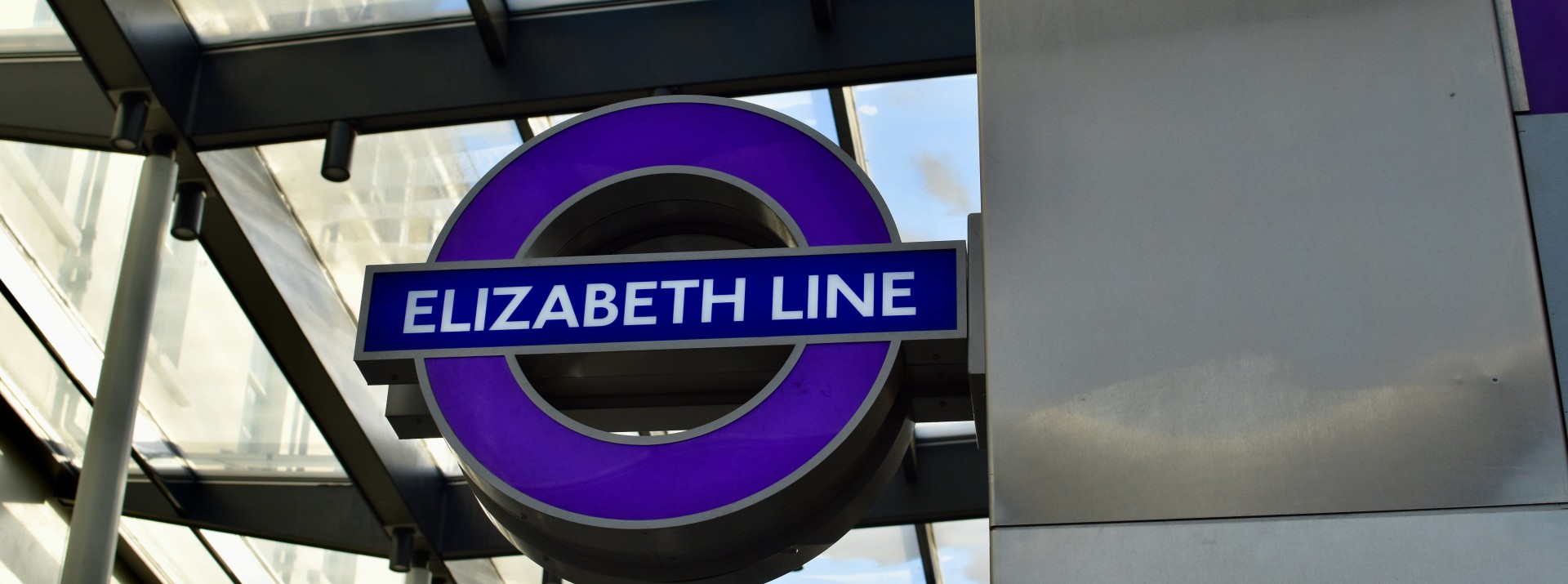
Platform Screen Doors designed, manufactured, and installed by Knorr-Bremse Rail Systems have been key to performance on the Elizabeth Line.
On top of that, an innovative way of installing the equipment at the central London stations offers a time-saving way of either installing Platform Screen Doors on a new railway system or retro-fitting them on existing networks.
The Platform Screen Doors are installed at eight stations on the central section of the cross-London railway and have not only vastly improved the service available to Elizabeth Line users but also involved an innovative way of delivering the product from the railhead to the platform, that can be replicated elsewhere with the added benefit of vastly reducing installation time in new or retro-fit projects.
The Platform Screen Doors are located at Paddington, Bond Street, Tottenham Court Road, Farringdon, Liverpool Street, Whitechapel, Canary Wharf and Woolwich. Seven of these stations opened in May 2022 when the central section welcomed its first passengers, with Bond Street opening in the following autumn.
Figures released by Transport for London (TfL) to mark the second anniversary of the opening of the central section of the cross-capital railway show that the 18-month period following its opening, the Elizabeth Line saw the highest passenger demand anywhere in the country.
More than 700,000 people per day use the network; if they use the central section then they will use the Platform Screen Doors from Knorr-Bremse.
Logistically, installing the equipment was likely to pose a challenge, however Knorr-Bremse created an innovative solution to what was a complex and likely time-consuming issue. Transporting the pre-assembled platfrom screen door modules from the surface to the platform was deemed unfeasible due to the depth of the stations and the tunnels. Assembling in-situ would have interfered with the construction and fitting-out of the stations at various crucial times in the programme.
The modules typically consist of a pair of automatic sliding doors and adjacent panels either side of the doors. The header contains the various systems fitted above the doors including the control gear and passenger information displays (PID) equipment. These are pre-assembled off-site and then fully tested so that they can be delivered as a fully functional item.
The PSD mounting plates are set out accurately and installed on the platforms before the pre-built modules are then delivered. These arrive via specially adapted works trains that are equipped with bespoke lifting mechanisms used to position the modules precisely onto the mounting plates once the train has been correctly positioned.
The lifting equipment is used to move the door modules horizontally and longitudinally while also having to be ability to tilt in order to clear pre-installed vertical and horizontal beams. Once the doors and screens are in place other equipment is used to fill the space between the top of the door modules and the tunnel roof including lighting panelsand architectural facades.
Using this method offers significant time and cost savings for networks across the world. It enables Platform Screen Doors to be installed overnight or during a possession therefore significantly reducing the number of days, weeks or months of closures required for the railway.
Once in situ, the Platform Screen Doors provide up-to-the-minute passenger information including details of the next trains and their stopping patterns, and live disruption information including delays, cancellations or amended train running patterns. Their roof-to-floor design means that the stations can be air-conditioned with energy saving techniques possible via the ability to localise where the air conditioning is which not only improves the conditions for passengers but provides environmental benefits by not losing unnecessary energy into the tunnels.
Furthermore, the screens act as media walls by offering not only advertising space, which can bring in critical revenue, but they are also home to antennas which allow Transport for London to offer 5G Wi-Fi at the central section stations located deep under the streets of the capital.
Figures released by the Office of Rail and Road (ORR) show that five of the ten busiest stations in Britain are on the new railway, and that of the new stations that opened on the central section, none saw less than 7.12 million passengers.
All but one of the stations feature straight platforms, however Tottenham Court Road’s platforms were constructed on a curve requiring a different design to the other stations. All told there are 16 platform facades with a total of 432 pairs of doors. Knorr-Bremse also manufactured and supplied the braking system with Air Supply and the on-board train doors on the Alstom Class 345 trains operating services on the Elizabeth Line.
Knorr-Bremse firmly believes its Platform Screen Doors increase safety, create cleaner, quieter platforms, deliver consistent dwell times, greatly enhance platform architecture, are a key enabler of Automatic Train Operation (ATO) and facilitate enhanced passenger information and entertainment.
Fitting Platform Screen Doors enables the suppression of train noise, offers economical platform air conditioning and energy savings while optional digital enhancements are possible including media walls, Wi-Fi and dynamic lighting.
The 432 pairs of Platform Screen Doors (PSD) differ to the Knorr-Bremse platform edge doors (PEDs) fitted to the Jubilee Line in that the new doors are floor-to-ceiling so they must withstand pressure pulses from the trains arriving (which could in the longer-term allow more trains to run per hour due to units entering stations faster and accelerating quicker). Also the Platform Screen Doors must provide access for maintenance while at the same time protecting those staff members from overhead line electrification. The Elizabeth Line Platform Screen Doors also feature a selective door function allowing for the doors not to open if the adjacent train door is locked and vice-versa.
Melksham
SN12 6TL
United Kingdom
Robert.Harker@knorr-bremse.com
Melksham
SN12 6TL
United Kingdom
Neil.Ponsillo@knorr-bremse.com
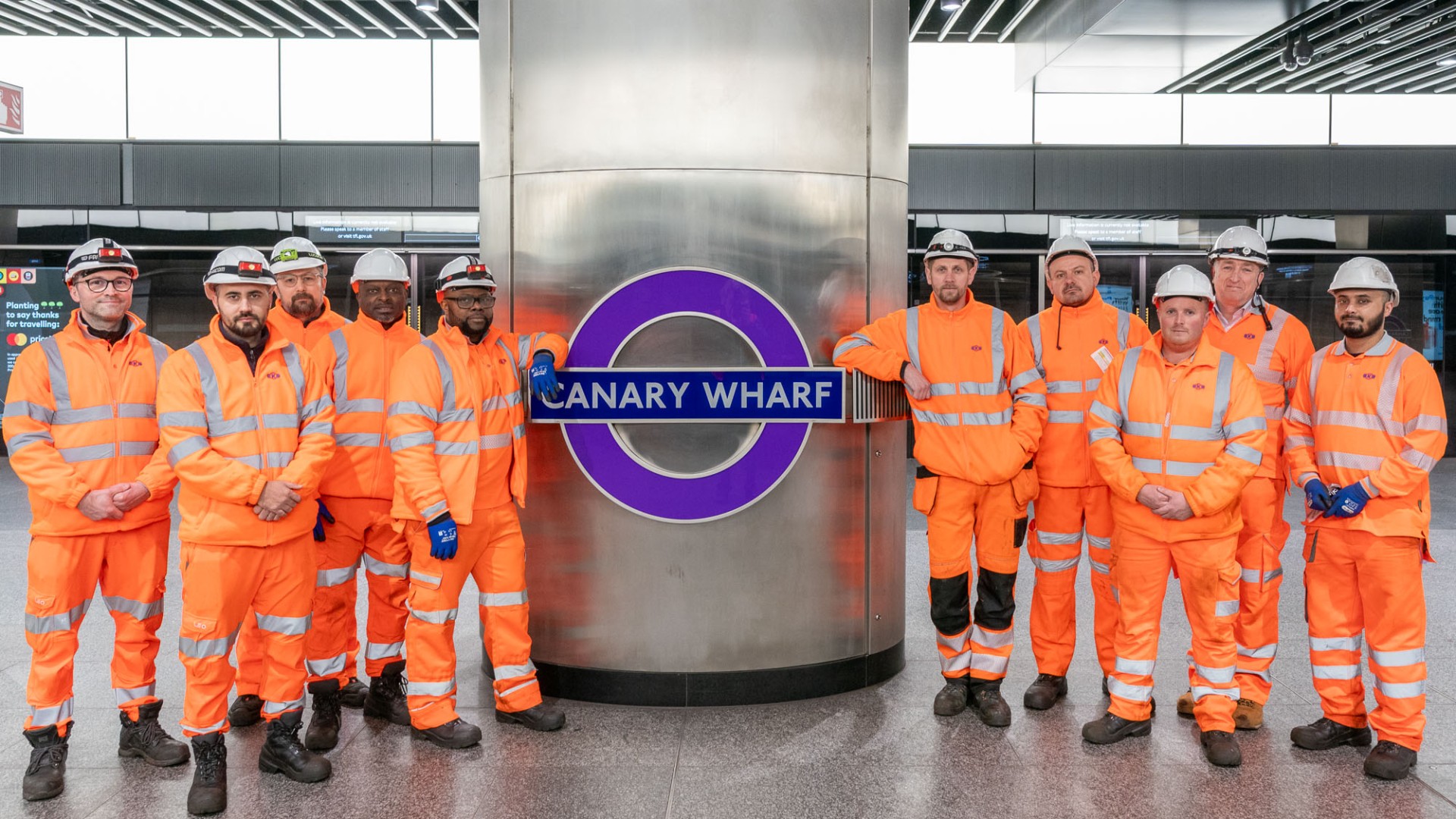
Because the Elizabeth Line was governed by the Interoperability Requirement of the Railways and other transport systems regulations, as well as common safety method on risk evaluation and assessment this meant this was the first time Platform Screen Doors had been authorised under these regulations.
The Platform Screen Doors must be perfectly synchronised with the train doors which involves interfaces with the signalling systems used on the Elizabeth Line, SCADA system and the power supply.
There is a new feature on the Elizabeth Line system, however, which further showcases the innovative nature of the installation. Individual train doors can be locked out of use as usual and this is reported via the unit’s train control management system (TCMS). Each Platform Screen Doors is able to be locked out of use too with its status reported to control. In normal operation, the train will brake to a stand automatically and when the signalling system registers it has stopped in the correct position permission is issued for the doors on the correct side to open.
When the Automatic Train Operation (ATO) or driver signals to open the doors, the train control management system issues the instruction but simultaneously a signal goes to the on-board control unit which is then transmitted to the wayside signalling system and on to the correct station Platform Screen Doors controller which will then instruct the doors to open.
The additional feature is that locked-out doors are synchronised with the adjacent door (train or platform) and so if a train door is locked out then during travel between stations the train control management system, via the on-board control unit and wayside signalling, sends that information to the next station’s Platform Screen Doors controller so that the relevant door at that station can remain locked out.
Another key development is the passenger information screens. These were fully integrated by Knorr-Bremse and located above each doorway. These provide information regarding the next train, stops and maps as well as live details of any disruption. However, the passenger information screens are also home to the public Wi-Fi system antennas which enables 5G mobile phone coverage along the length of the platform. The Wi-Fi equipment is accommodated into the design and is something that Knorr-Bremse offer as a further way of improving the passenger experience.
Not only did it design and conduct the installation of the Platform Screen Doors, but Knorr-Bremse Ltd is also responsible for the maintenance of the equipment. If a doorway has a problem, then the operator of the Elizabeth Line will continue to try and get trains running, however Knorr-Bremse aims to be on site to carry out repairs within 30 minutes and, 90% of the time, the issue is insignificant. If it is something more serious, such as a panel being damaged, or a door has failed completely then maintenance teams will undertake repairs at night. However, Knorr-Bremse points out a doorway has not yet remained out of service through reliability issues for a significant period since passenger trains began running through the central section of the Elizabeth Line in May 2022.
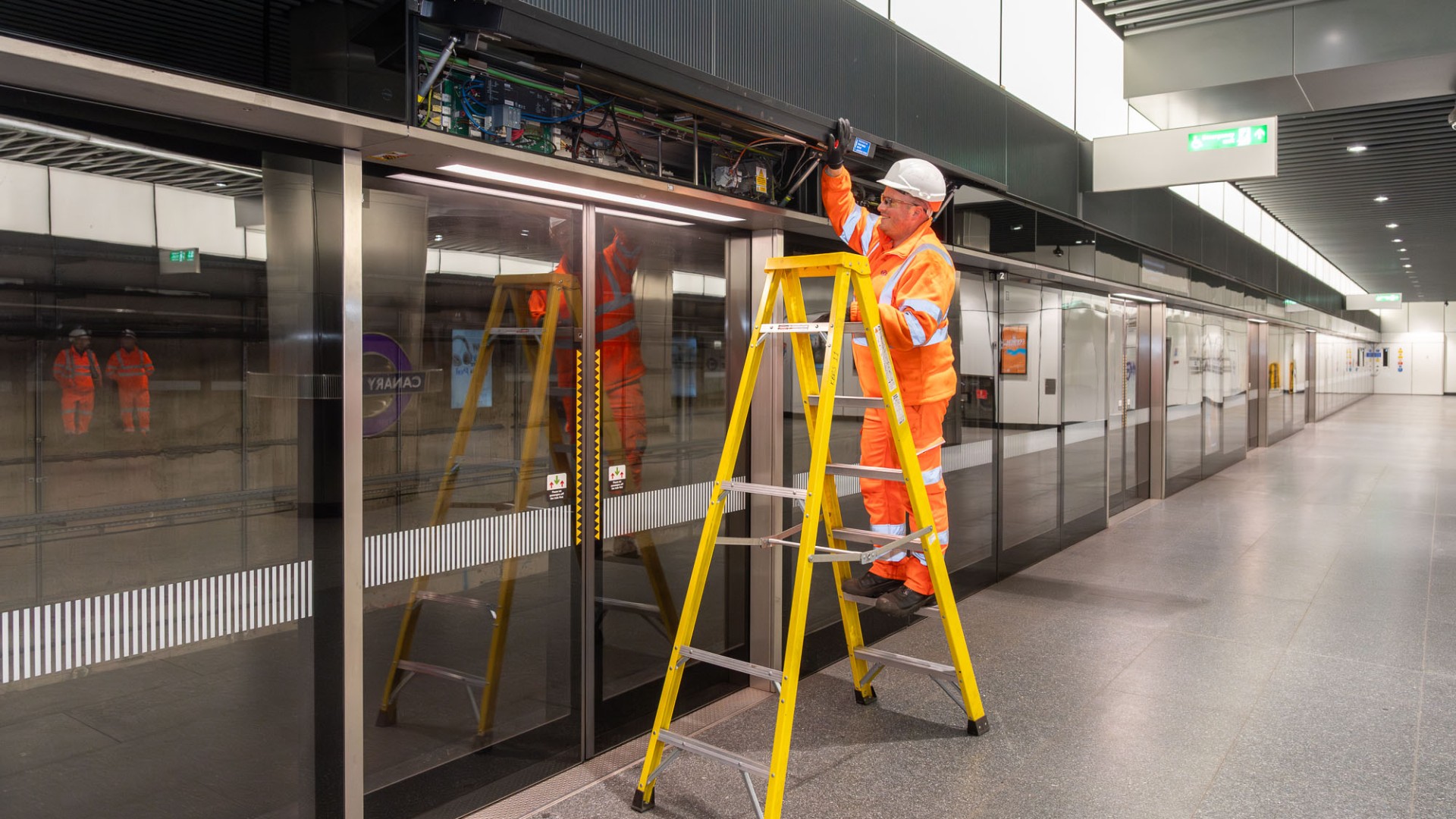
These Platform Screen Doors have offered real benefits in terms of safety and improved passenger environment. They were installed in a difficult location using an innovative method that Knorr-Bremse plans to replicate on other projects and which it believes can significantly cut the time taken to install such equipment and therefore also cut the costs of such projects.
The Platform Screen Doors in use on the Elizabeth Line show what is possible. Knorr-Bremse has the experience not only of designing these for the new railway, but it has also developed an innovative way of installing the system which can save not only time significant time but also significant money for networks interested in using the technology.