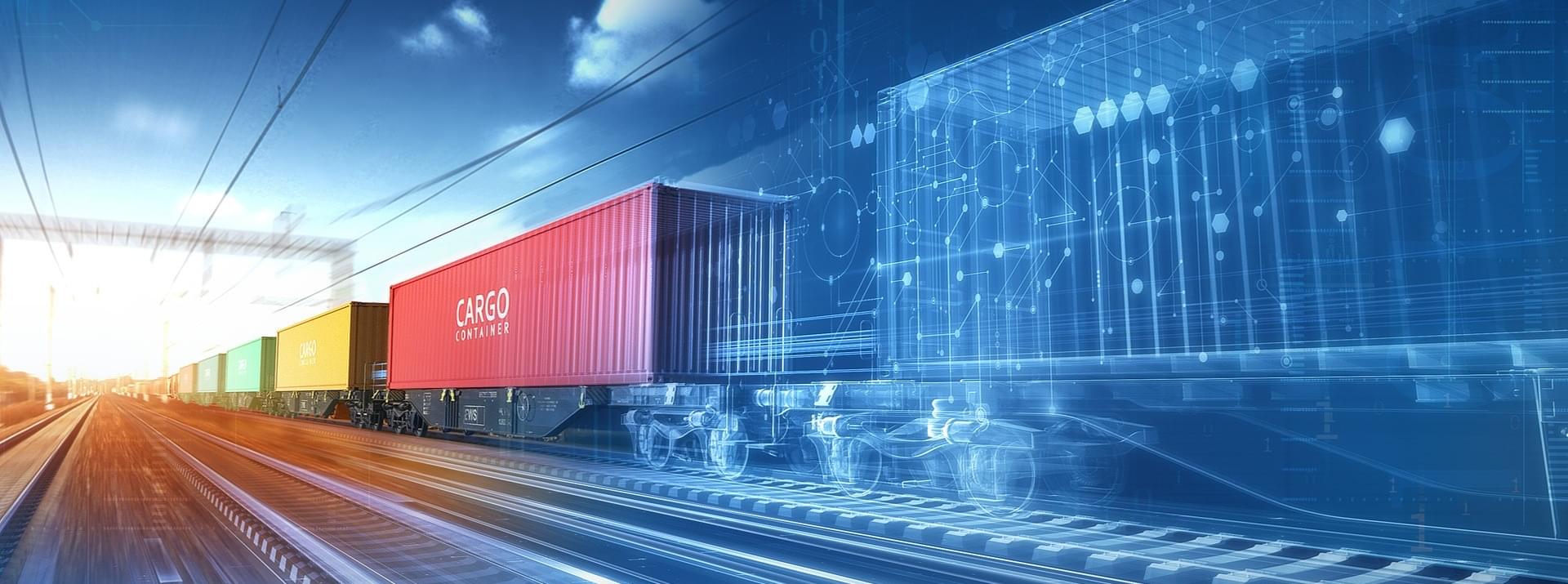
If Europe is to achieve its 2030 target – to increase the proportion of freight transported by rail to 30 percent from 18 percent today –freight cars and their supporting infrastructure must be digitized. This is the aim behind the Digital Freight Train (DFT) and other solutions on which Knorr-Bremse engineers are currently working.
“In Europe, we still couple together freight trains – unlike passenger trains – in much the same way as we did 130 years ago,” says Andreas Leiber, Director of Sales & Train Coupling Systems at Knorr-Bremse Systeme für Schienenfahrzeuge GmbH. “One of the shunting crew stands between two cars, hooks the screw coupling’s 30-kilo drawbar to the draw hook, tensions the link, and then connects the brake hoses.” Assembling a 25-car train can easily take a full hour. Other preparatory work is also done manually. For example, every single brake on a newly assembled train must be tested to ensure it is working perfectly – taking another three quarters of an hour.
Too slow, too cumbersome, too complicated: Why rail freight needs a makeover
From marshaling yard to… Brussels. By 2030, the EU aims to boost the proportion of freight transported by rail to 30 percent, from just 18 percent today. This is scarcely surprising. No other mode of transportation is as green as rail or as capable of rapidly transitioning to 100 percent renewable energy following the green energy transition. Per tonne-kilometer, a truck emits around 111 grams of greenhouse gases, whereas a freight train only emits 17 grams.
But to reach the EU’s 30 percent target, rail freight must first meet a clear condition: It must become much, much more competitive. Because they aren’t automated, the processes currently used to prepare trains make the whole industry too slow, too cumbersome, too expensive, too awkward, and too inflexible. To pick just one example: Freight cars don’t even have a power supply.
Digital Freight Train (DFT): automated processes, digital solutions
The Digital Freight Train – or DFT for short – is the key to achieving this 30 percent target. Starting with individual freight cars, automated processes and digital solutions are expected to boost freight transportation capacity, efficiency, and availability. The final result would be smart, intermodal fleet operations in which individual freight orders would appear to find the fastest route to their destinations as if by magic. But using smart, automated processes to run entire trains and train fleets presupposes a smart, automation-compatible freight car.
As a member of Europe’s Shift2Rail technology initiative and the Technical Innovation Circle for Rail Freight Transport (TIS), Knorr-Bremse is one of the driving forces behind the Digital Freight Train. From freight car to train, from train to train assembly, DFT developers are focusing on three main action areas:
- FreightLink: the Digital Automatic Coupler (DAC)
The 21st century solution for transporting freight by rail is the digital automatic coupler (DAC). Long since standard in the passenger rail industry, the technology will now be used to automatically couple together freight cars, too. This doesn’t just cover the mechanical coupling process or connecting the braking system’s compressed-air pipes. The DAC will also automatically connect new cables carrying electricity and data signals.
These new connections are vital prerequisites for digitizing rail freight transportation – because they enable the new technologies needed for autonomous train operation (ATO). Multiple DAC variants produced by various manufacturers are currently undergoing field trials. And once the process of upgrading some half a million European freight cars is kicked off mid-decade, Knorr-Bremse’s automatic freight car couplers will join the party. - FreightControl: electronic hardware and software for freight cars
In the future, all freight cars will be equipped with electronics (hardware and software) supporting a wide range of digital functions. The electronics will also process data collected by multiple sensors and aggregate it across the entire train before transferring it to the rail operator’s cloud-based train management system. This will make comprehensive condition-based maintenance (CBM) available for freight cars, too. Digital or automatic brake testing will be another onboard feature.
And once digital automatic couplers (DACs), digital brake testing and smart environment detection are all working together, at a stroke it becomes feasible to run highly automated shunting and marshaling yards. In short: These digital features hold the key to substantially reducing the long-drawn-out processes that still characterize freight car operations. - Electropneumatic braking system of the future (EP brakes)
Precisely because they are not fitted with onboard electronics, freight trains in Europe are still braked using exclusively pneumatic mechanisms. Compressed air is used to transfer both braking signal and braking force at the same time. The major downside? The signal only travels relatively slowly along the full length of the freight train.
The electropneumatic braking system of the future on which Knorr-Bremse is currently working is based on a passenger train solution. Equipped with electrical wiring, the system will transfer braking and control signals electronically, even in freight trains, so that pneumatic braking is applied to all bogeys simultaneously. This will enable longer, heavier trains to travel faster – while maintaining the same braking distances. An important factor in view of the planned increase in rail transportation capacity.
No doubt about it – the steps required to actualize the Digital Freight Train are highly complex. Given the need for interoperability, this makes industry-wide cooperation all the more vital to the project’s success. The various mechanical, electrical and digital elements (software, DACs, pneumatic braking systems, EP brakes for freight cars) must all be designed so that multiple manufacturers can produce them – and yet still be 100 percent compatible with the Digital Freight Train system as a whole.