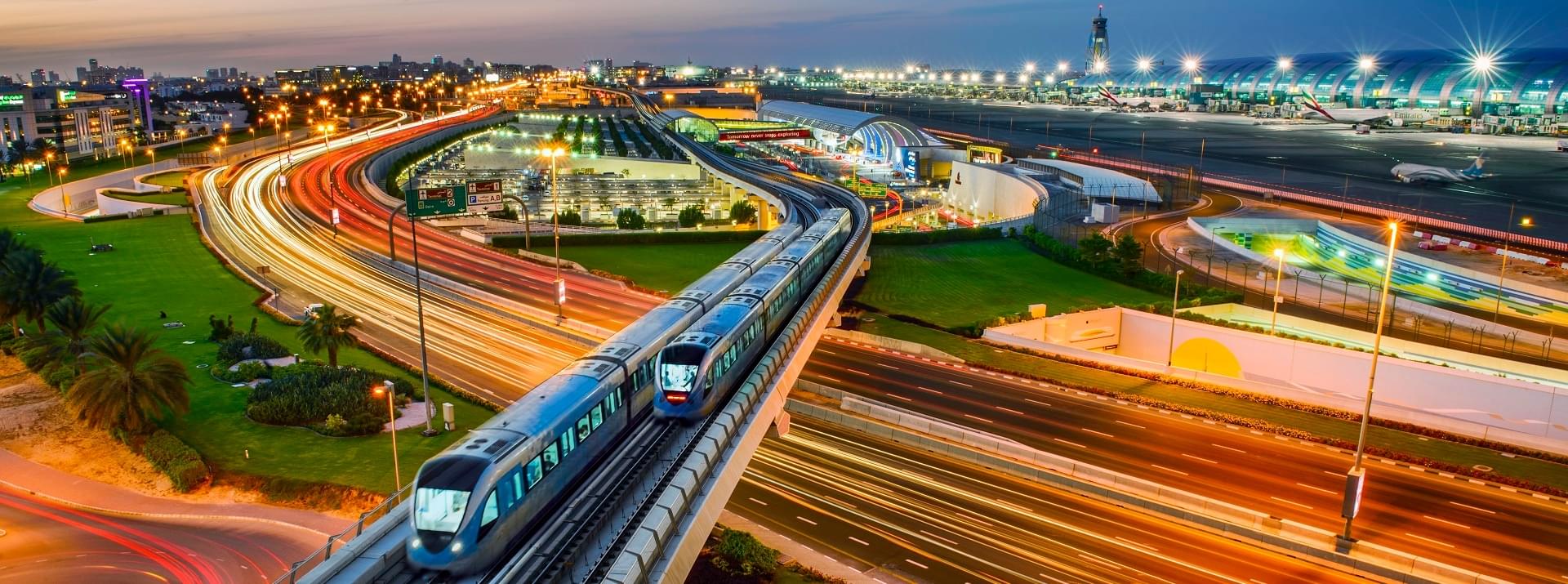
How does the train control provide all the control and monitoring functions of modern trains? What changes are coming the development of railway brake control electronics? In the third part of our article series, engineers from Knorr-Bremse Budapest talk about the challenges presented by train control systems, backbone networks and railway integration.
Contact
Helsinki út 105
1238
Magyarország - Hungary
info@knorr-bremse.com
What are train control systems?
In railway industry jargon, a train control system is called TCMS. TCMS is an acronym consisting of the initials of Train Control and Monitoring System (less commonly Train Control and Management System). This term is used for systems that establish the data link between the electronically controlled subsystems of a train formation. In the related literature, TCMS refers to the communication network, the autonomous electronic units connecting to it and the sum of services they provide.
TCMS functions
All major rail vehicle manufacturers develop TCMS systems that provide control and monitoring functions for the entire train. The devices have standard communication interfaces, ensuring efficient integration with different subsystems from various suppliers. Thanks to a high level of integration, communication takes place on the same central backbone. For train manufacturers, this offers a number of benefits: in addition to easy expansion and improved scalability of functions, it also means that less space is needed for carriage wiring, which simplifies production and maintenance.
Today, on a modern train, all subsystems with programmed controls are connected to the TCMS. Depending on the design, this includes, but is not limited to, the cooling, heating and ventilation system, the braking system, the passenger information units, lighting, diagnostics, door control, intelligent driver information system and various data acquisition modules. The architecture is modular and allows good scalability, with the advantage that a suitably designed TCMS can be easily adapted to different types of trains (tram, high-speed train or metro cars). The operation and maintenance of train formations will become more predictable thanks to the continuously accessible information. The design also offers further possibilities: when supplemented with the appropriate components, trains will be capable of external communication over long distances, allowing remote monitoring or even control.
Take a brake with us
At Knorr-Bremse Budapest, we work every day for a safer and greener future. In our Brake with us series, we not only show you how railway brake controllers and related services and systems work, but also give you a glimpse behind the scenes. Our engineers tell us personally how development and testing is carried out, how the various components combine to form a complete whole at the end of the process, and how passengers only notice that the vehicle stops exactly where and how it needs to.
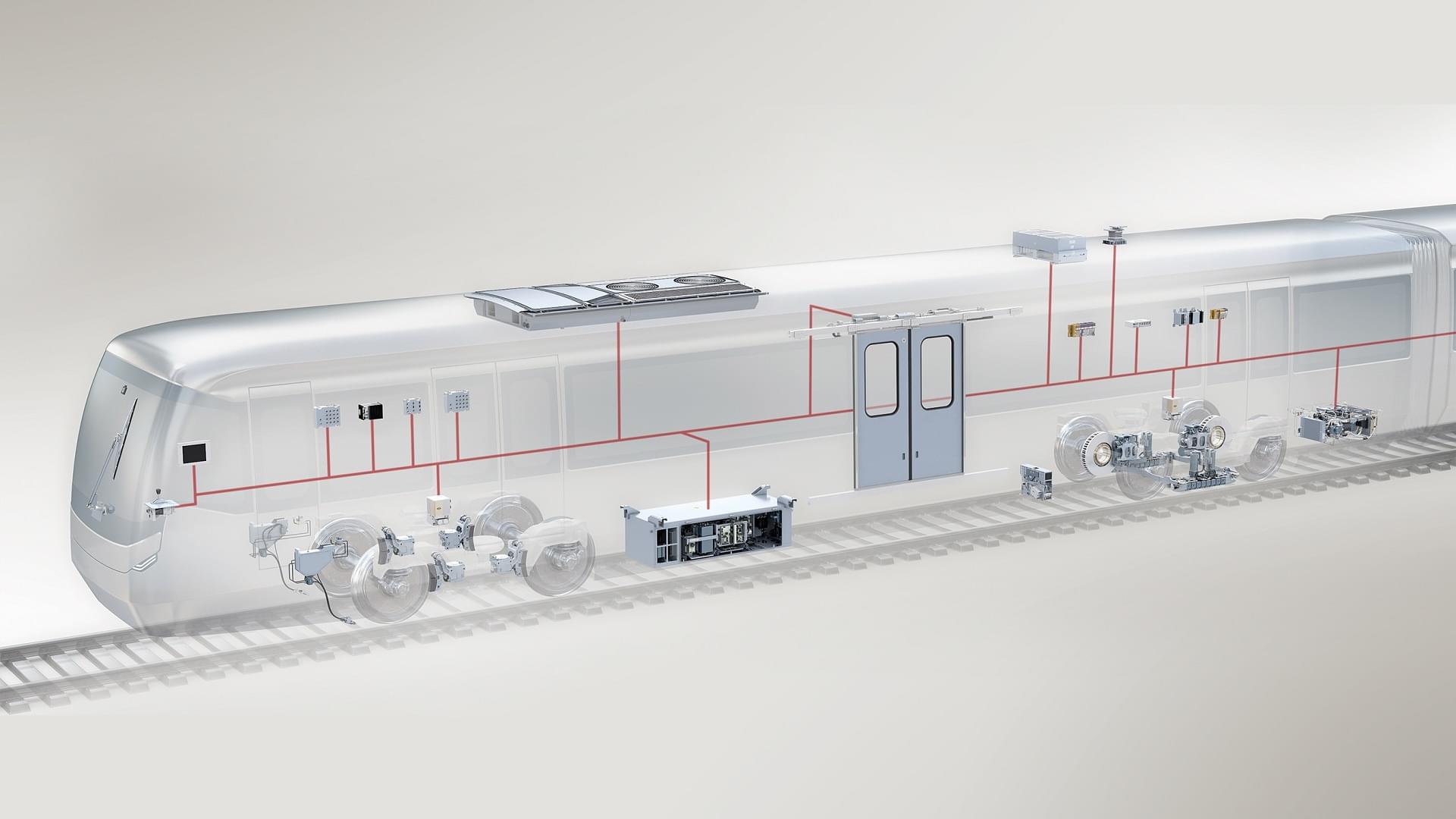
Communication networks
The first communication networks woven into rail vehicles appeared in the early 1990s. Priority objectives in the design included reducing maintenance costs, providing a higher quality of service to the travelling public (helping to increase rail’s market share of passenger transport) and expanding diagnostic capabilities, thus enabling targeted, on-demand servicing.
The specific conditions of railway operations present designers with a number of constraints that are not features of other industries. First of all, due to the length of train formations, the backbone network requires the ability to operate reliably and deterministically with end-point distances of up to 1,000 metres. The delay in the data must not exceed the delay required for real-time communication.
To achieve the required Safety Integrity Level (SIL), redundancy of several units with the same function may also be required to avoid a situation where the failure of a single high-priority unit could compromise the safe operation of the whole system. A further important factor is that the lifetime of the trains can be up to 30-40 years, and, during this period, both maintenance of the subsystems and product support must be guaranteed. For electronic devices, maintaining a supply of parts is a challenge in itself over such a timeframe.
In response to these requirements, the IEC 61375 standard system, consisting of several parts, was developed specifically to meet the internal communication requirements of train formations, and it defines the logical structure and main characteristics of the backbone network. In addition to the description of the general TCMS architecture, the document package includes protocol definitions (for example MVB – Multifunction Vehicle Bus, TRDP – Train Real Time Data Protocol) and compliance test specifications.
Multifunction Vehicle Bus (MVB)
MVB (Multifunction Vehicle Bus) was the first really widely used communication protocol on TCMS networks. It is described in detail in the IEC 61375-3-1 specification and is still used today for exchanging messages between devices in many TCMS networks. The prominent role of MVB buses is due to the robustness of the protocol and the parameters designed for railway use. MVB networks always have a 'master' device, which is responsible for scheduling communication in the system. Communication primarily takes place through cyclical messaging. Data always runs on two redundant lines, and in many cases safety-critical elements are installed in duplicate, so that if one fails, the second can take over immediately.
There is a growing demand, however, for increased functionality on modern trains, which the MVB can no longer meet due to its limitations (for example, low bandwidth). For these reasons, they are no longer used on newer trains and are being replaced by Ethernet-based networks and communication protocols (for example TRDP, Ethernet/IP). Their adaptation to rail – while offering advantages – also poses new issues.
Railway integration challenges for Ethernet networks
One of the main issues is to provide real-time operation. This can be ensured by advanced topology solutions and proper network design: on the one hand, safety-critical functions are separated (even physically) from less time-sensitive data in the design. On the other hand, the data communication required to transmit critical information - because it is typically based on cyclical operations - can be planned accurately. Furthermore, it is possible to assign different priorities to the information packages; in this way, the network can prioritize the more important data during transmission.
Another important aspect is data security, i.e. how secure is the system on train formations against external attacks. For now, the data exchange between safety-critical functions still takes place on a separated part of the network, but the main task for TCMS and subsystem developers in the coming years will be to increase the sophistication of protection against malicious intrusions.
In conclusion, TCMS systems and the development of rail brake control electronics themselves are about to undergo significant changes. Earlier bus systems will be replaced by Ethernet-based solutions, and a much higher level of integration of different functions, including safety-critical ones, will become standard on train formations as well. It also means that the network and its constituent components must meet a number of new 'Cybersecurity' requirements to prevent possible malicious manipulation.
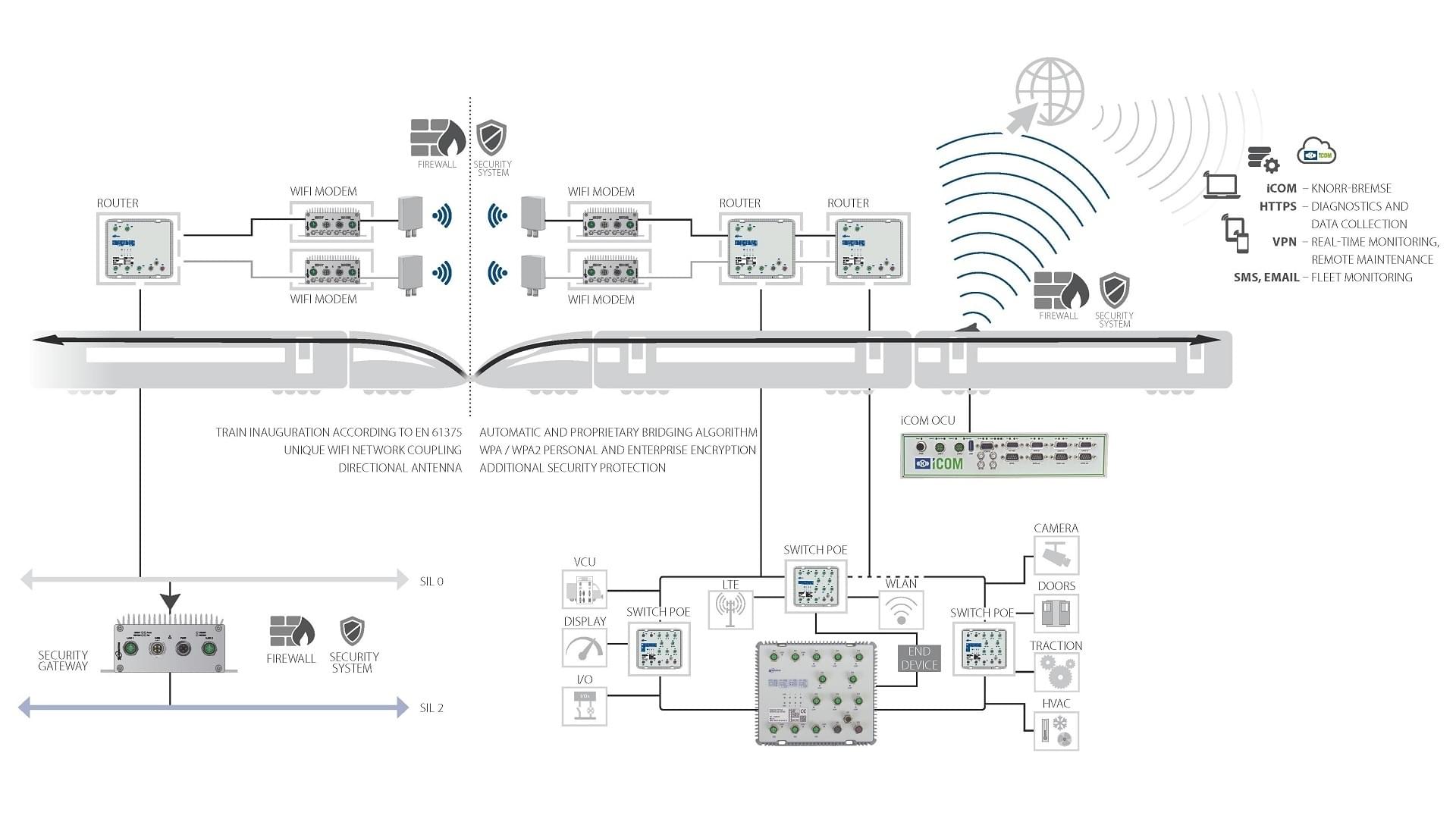