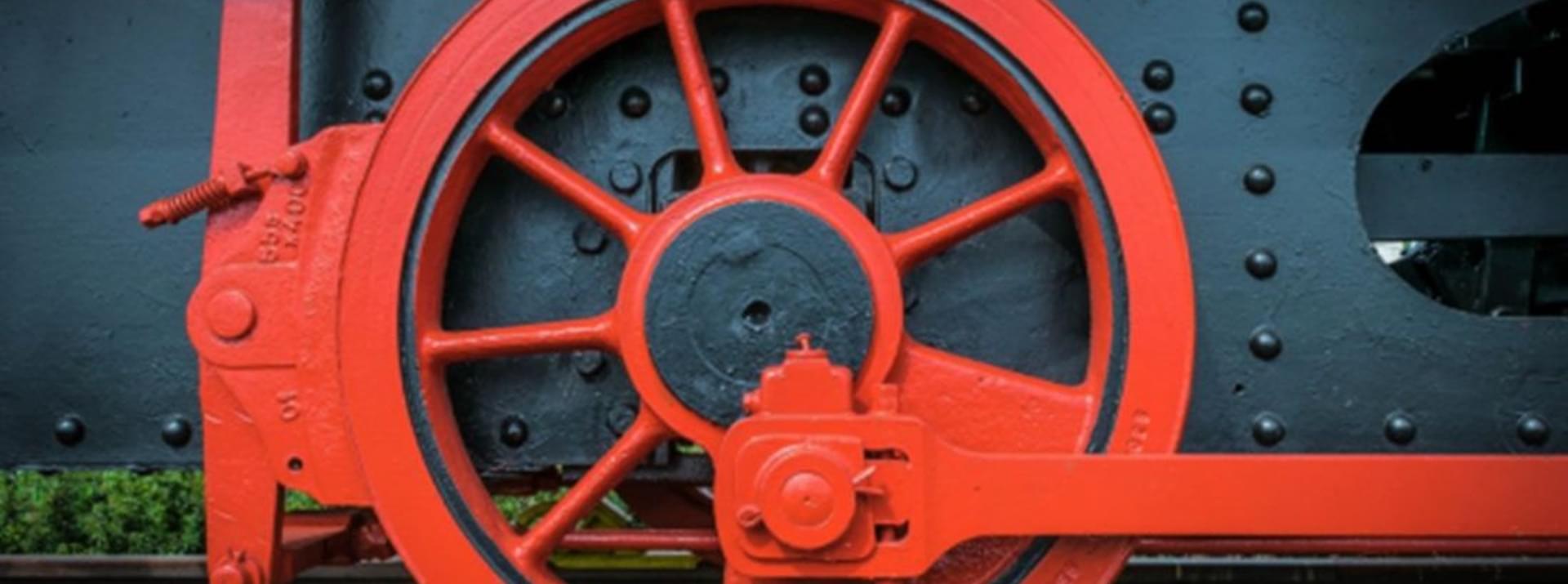
Why do you need train braking software?
We – who work at the Research and Development Department of Knorr-Bremse Budapest – are sometimes questioned by acquaintances, “laypeople”, when work comes up in conversations with friends and family, about what electronics and software developers do at a railway brake company. “Well, a hundred years ago, a train stopped in just the same was as today: the driver pulls the lever and the train brakes. What needs to be and what can be developed further about it?”
Indeed, most railway passengers can see that the vehicles have become more beautiful, faster, comfortable and quieter over the years – and it’s obvious that a train can start, travel and stop. Still, in recent decades, railway traction – and braking – have also undergone enormous technical development. Just like most of the devices that surround us today, railway vehicles are unable to operate at all without electronic controls and software. If the electronics and control software do not work properly, no modern train can move an inch. Of course, they can stop – as everything stops once – but it does matter how.
Contact
Helsinki út 105.
Magyarország - Hungary
info@knorr-bremse.com
Today, even on the railway, it’s natural to expect that a vehicle will stop smoothly, comfortably, accurately, and safely, and also that it will be energy-efficient; that is, as little (kinetic) energy as possible will be lost. It’s important for the operator, and the manufacturer and designers of the vehicle, that the brake system will be reliable, universal, and easily configurable; it should fit in with the characteristics of the particular vehicle and, at the same time, it shouldn’t cost much either.
The most important task of the first electronic brake controllers was similar to that of the ABS function in cars (although it was a “standard accessory” much earlier here): the vehicle should stop safely and quickly, even if the adhesion conditions are unsuitable; that is, the wheels shouldn’t slide along the rails. The controller can adjust the braking force quickly and effectively through the electro-pneumatic valves, which preventing the wheels from sliding. Over time, this function has been complemented by the fast, accurate and carriage-distributed control of the braking force and many additional features that had previously been put in place using large, slow, complicated and expensive mechanical or electrical control elements.
What is the brake controller’s task?
For decades, railway vehicles have operated without any electronics or software, only with mechanical (pneumatic, hydraulic, electromechanical, etc.) braking systems – and they are still capable of doing this today. Today’s railway brakes basically operate on the same principles as before and, for safety reasons, a vehicle can stop using traditional mechanical means, even when it so happens that the electronic control systems are out of order.
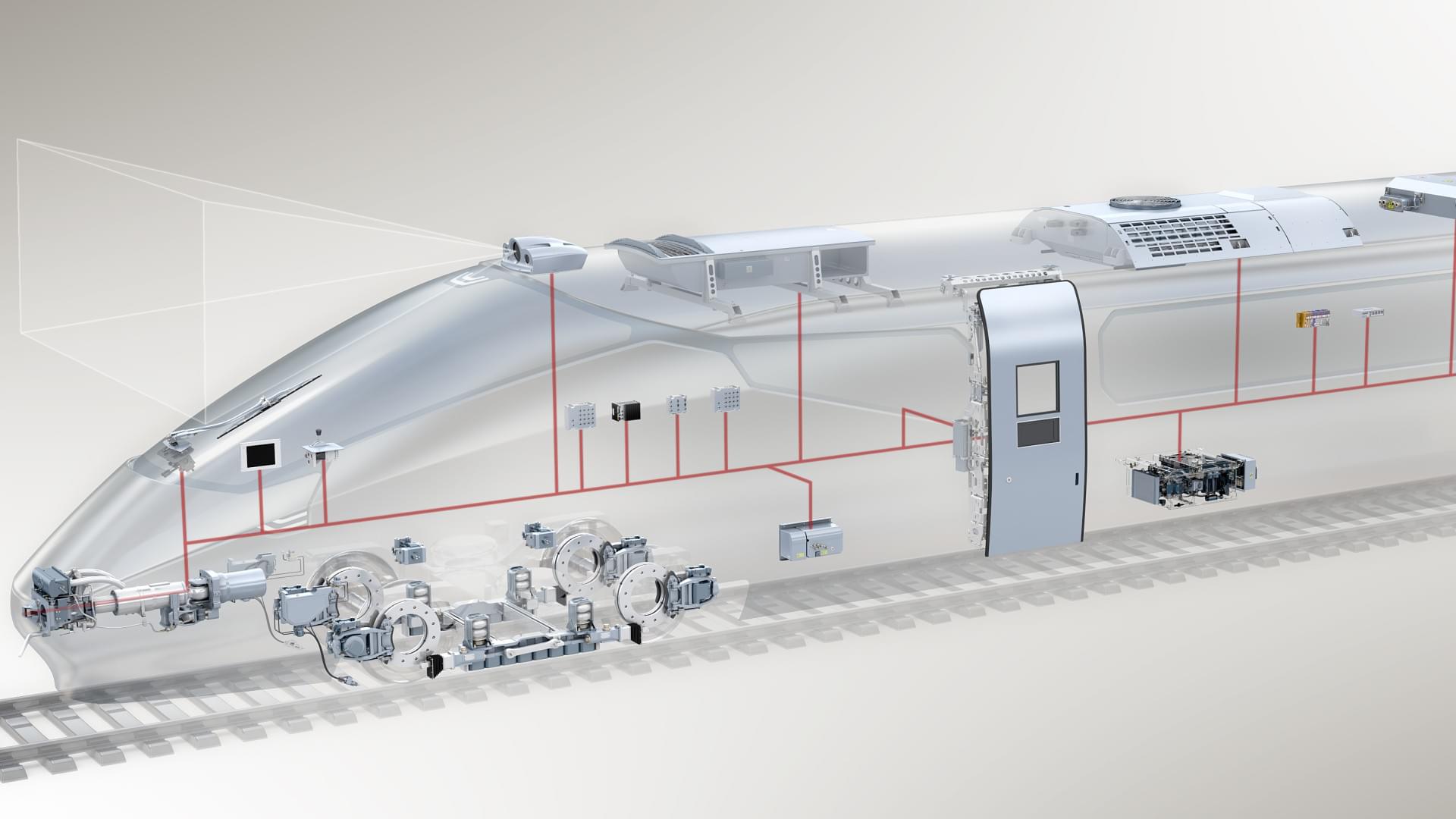
Normally, however, they do operate and perform a variety of tasks. These include – but are not limited to:
- wheel slide protection
- fast, accurate, and jerk-free control of the braking force according to the driver’s command
- synchronisation of the various brake systems (e.g. electrodynamic and pneumatic brakes)
- distribution of the brake force between carriages according to different algorithms
- communications with the vehicle’s other systems (vehicle controller, drive controller)
- speed calculation
- diagnostics, fault indication, fault and data storage
- control of other brakes (e.g. magnetic track brakes, parking brake)
- control of the air supply system (compressors)
- slide prevention
- automatic brake tests, brake weight calculation
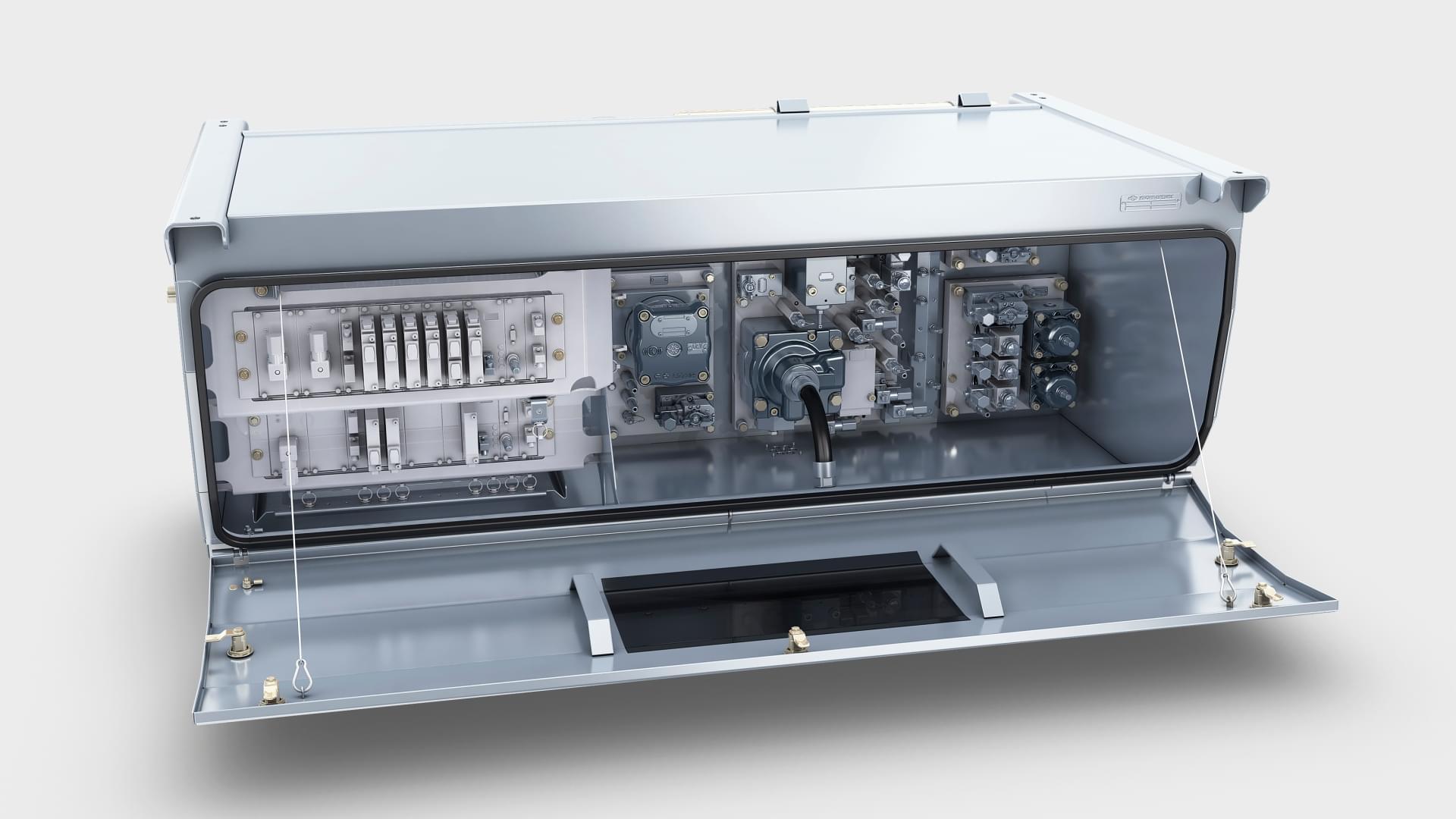
So many vehicles so many brake types
As a global market leader, Knorr-Bremse covers practically the entire railway vehicle industry, including urban, suburban and heavy rail traction, and special (e.g. track maintenance) vehicles as well. This requires flexible, modular control systems that can be used universally and safely on a German locomotive, Indonesian metro stock or even a Japanese bullet train. Unlike in the automotive industry, railway vehicles are made in small series and have to meet a lot of unique requirements. Every vehicle’s system is different: the vehicle control, the drive system, the communication network and the mechanical (pneumatic/hydraulic) elements of the brake system vary and the tasks and functions related to brake control are different as well. Added to this are the particular regulations of the operators or the countries and regions. These requirements can only be met if the tools, hardware and software components and development processes are universal, modular, easy and quick to configure, and can be adapted to the different vehicles.
Of course, we also keep up with technological developments, so we not only develop our products and tools project by project, but constantly improve them over time as well.
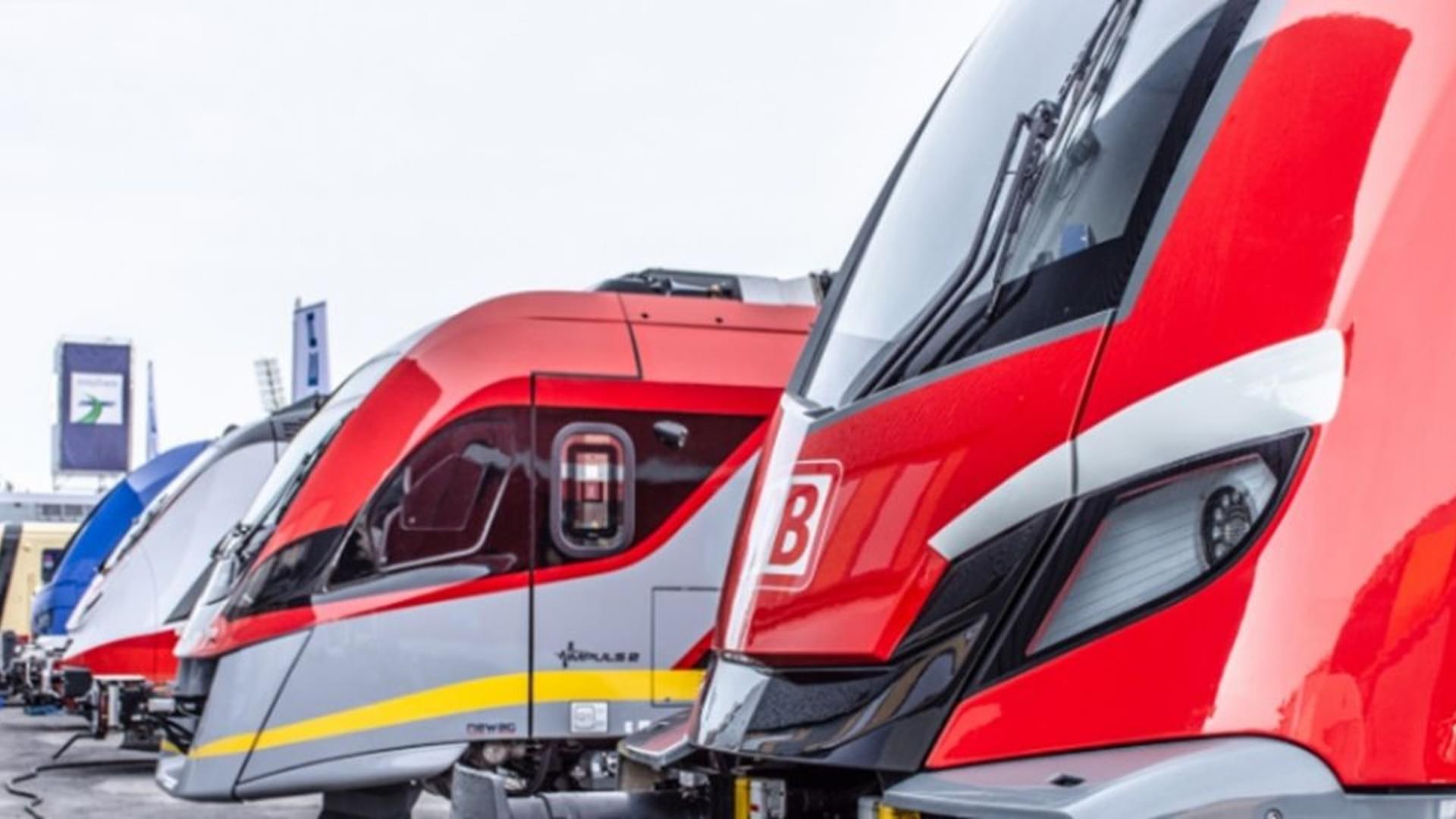
The brake control – and what is behind it
The functions described above require systems and development/testing processes that ensure stable and safe vehicle operation and meet the most rigorous railway standards. The hardware and software used and delivered by Knorr-Bremse are made in accordance with the regulations applicable to safety-critical systems and undergo multiple inspections and tests. A number of different teams therefore work in the Budapest Research and Development Department to ensure that both the products delivered to customers and the subsystems, services, tools, and processes required by them operate reliably and are constantly improving. These include the hardware for brake control electronics, the embedded operating system, the development of vehicle-specific functions and testing all of these. Furthermore, we’re constantly improving the tools and services used for testing and development, or indeed systems that are not directly related to brake control (e.g. service software, driver advisory service and collision avoidance systems).
In our topics series, we would like to introduce why and how railway brake controllers and related services and systems work, what processes are involved in their development and testing, and how the various systems combine into a whole, of which a passenger can only perceive that the vehicle eventually stops right where it should and as it should, and the question of how the brakes on a train work does not even arise.
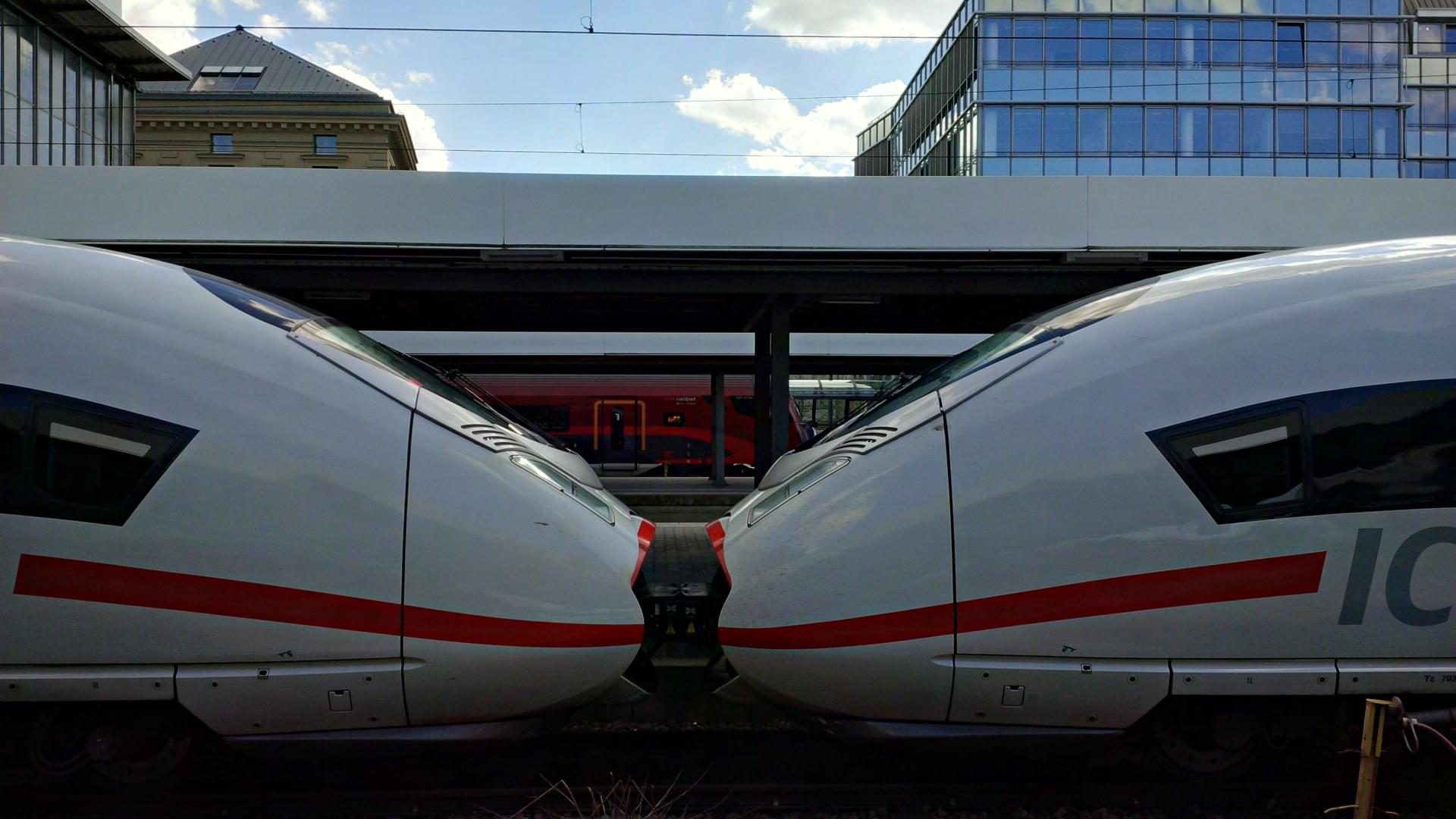