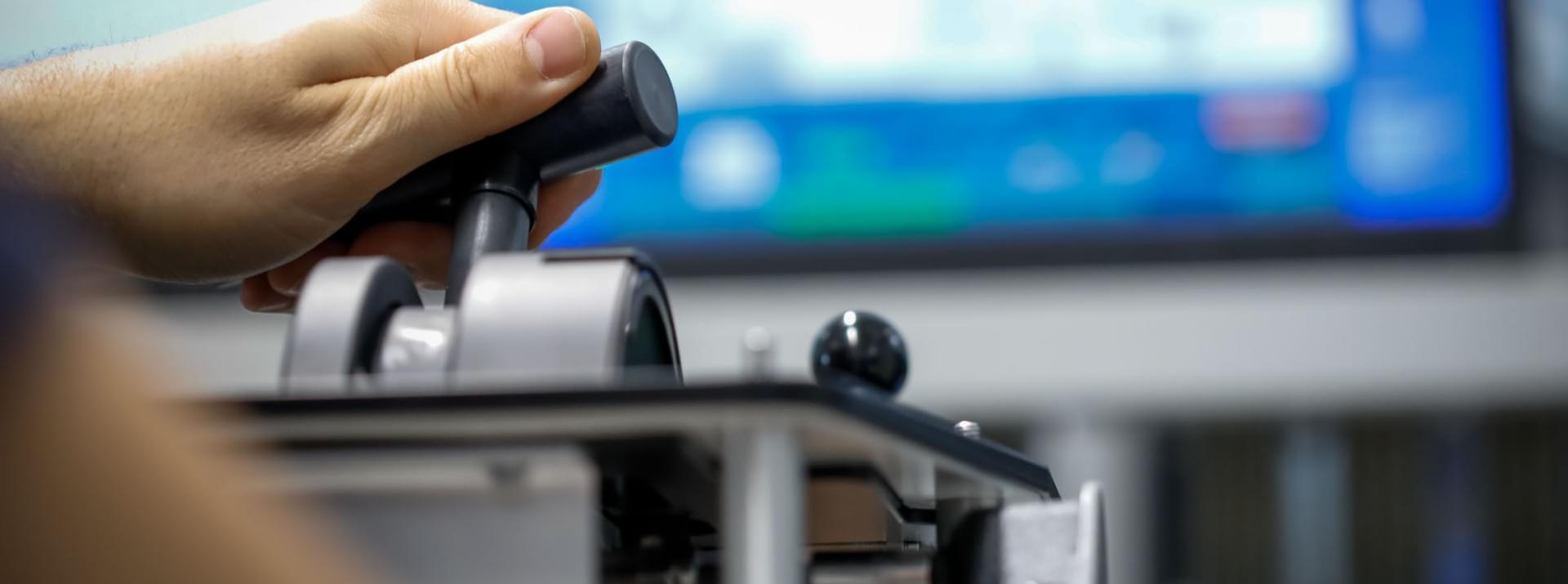
Mit den Fahrhebeln des MotionLead beschleunigen und bremsen Zugführer weltweit ihre Fahrzeuge. Dabei “übersetzen” die Systeme ihren Brems- und Beschleunigungswunsch in Brems- und Traktionsbefehle. Durch ein Baukastenprinzip kann Knorr-Bremse die Fahrhebel individuell an die Bedürfnisse der Betreiber anpassen. Doch was steckt nun genau hinter dem MotionLead? Wir haben unseren Experten Michael Holz aus München gefragt…
Was sind die Aufgaben und Funktionen des MotionLead?
MotionLead lautet die Bezeichnung für die im Führerstand verbaute Mensch-Maschine-Schnittstelle zwischen Fahrzeugführer:in und Fahrzeug. Mit ihr beginnt das Fahren oder Bremsen. Als Fahr- beziehungsweise Bremshebel überträgt der MotionLead – abhängig von der Hebelstellung – den Wunsch der Fahrzeugführer:in an die Traktions- und Bremssteuerung des Fahrzeugs. Die Hebel können zum Bremsen (MotionLead Brake), zur Traktion (MotionLead Traction) oder in einem Hebel kombiniert zum Fahren und Bremsen (MotionLead Master) genutzt werden.
KONTAKT
80809 München
Deutschland
sales.sfs@knorr-bremse.com
Woraus setzt sich ein MotionLead zusammen?
Aus zahlreichen Komponenten, die ganz nach Kundenwunsch aufgebaut werden können. Basis ist unser MotionLead Kit, ein umfassender, standardisierter Baukasten aus zahlreichen Einzelelementen. Der sichtbare Hebel im Führerstand stellt allerdings nur die sprichwörtliche Spitze des Eisbergs dar. Hinter den Verkleidungen geht es weiter: Unterhalb des Führerpults folgen zahlreiche mechanische, elektrische und pneumatische Elemente für die Signalübertragung der Hebelstellung. Sie erfolgt mittels vieler elektromechanischer Schalter sowie eines Winkelsensors. Zusätzlich können pneumatische Druckregler den Druck der Hauptbremsleitung regeln. Ein meist integriertes Schnellbremsventil entlüftet im Notfall die Hauptluftleitung direkt. Bei Bedarf integrieren wir eine Menge Zubehör wie Schlösser, Verriegelungen, Zusatzknöpfe oder Beleuchtung. Teilweise ist in den Hebeln auch die Totmann-Funktionalität verbaut, eine elektrische Sicherheitseinrichtung. Wird sie nicht regelmäßig durch die Triebfahrzeugführer:in betätigt, löst das Bremssystem eine Zwangsbremsung aus.
Die Teilfunktionen des Baukastens können wir sehr flexibel kombinieren. Da dies über Standardteile geschieht, kommen wir auf höhere Stückzahlen und können unseren Kunden Kostenvorteile bieten. Außerdem sind die Funktionen bereits vorqualifiziert und wir müssen sie nicht projektspezifisch nachweisen. Dies führt zu einer kurzen Time-to-Market.
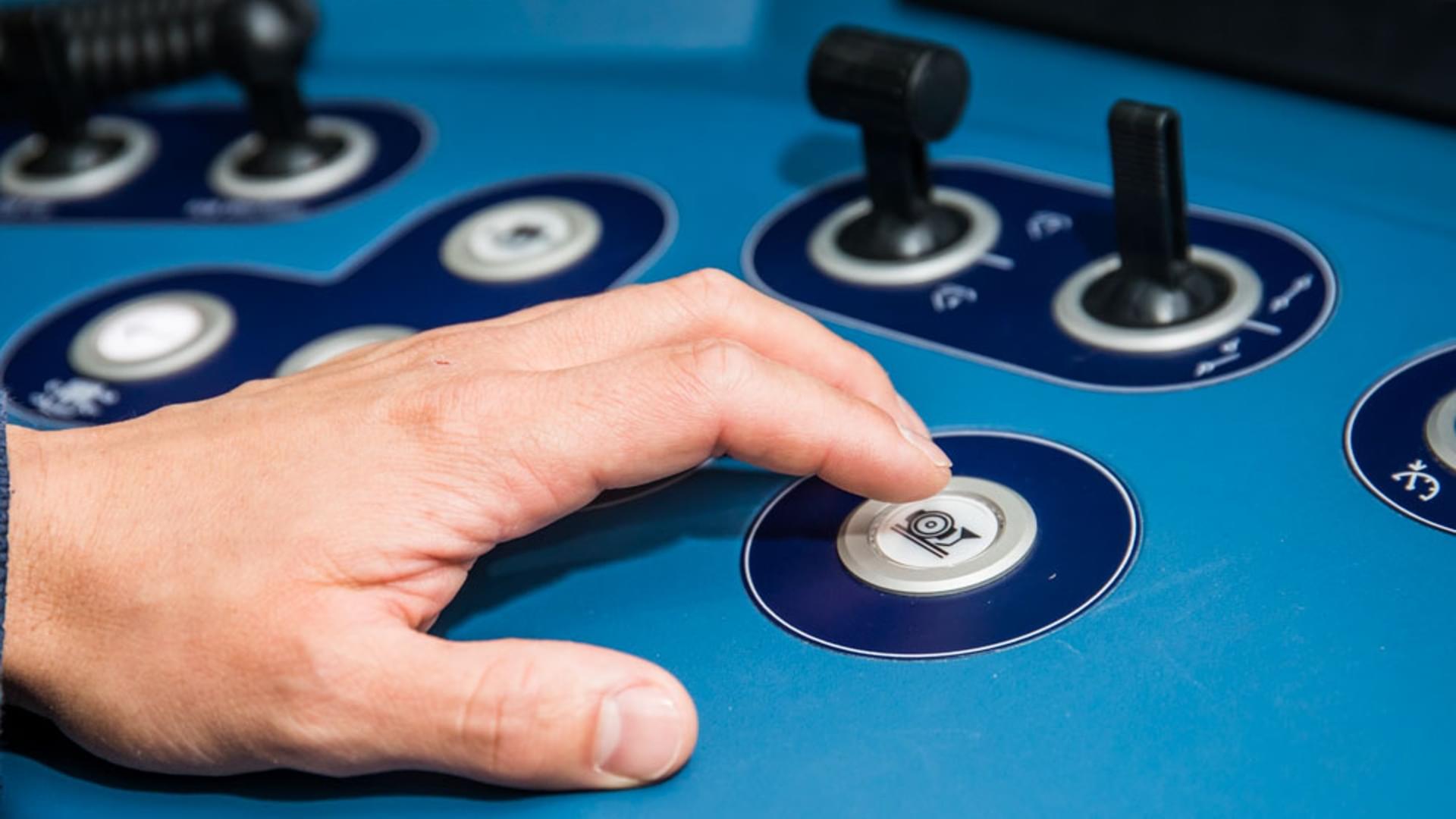
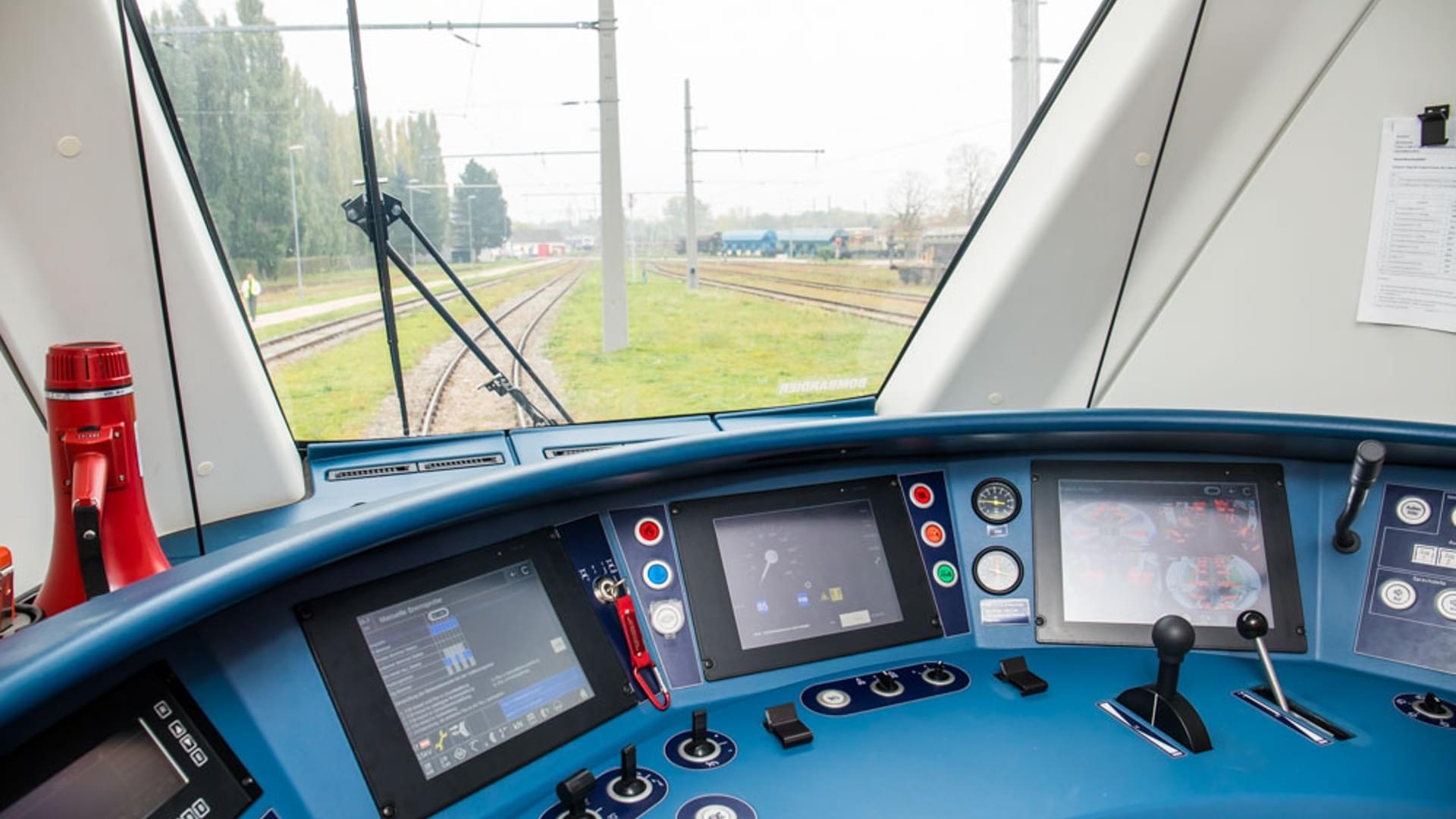
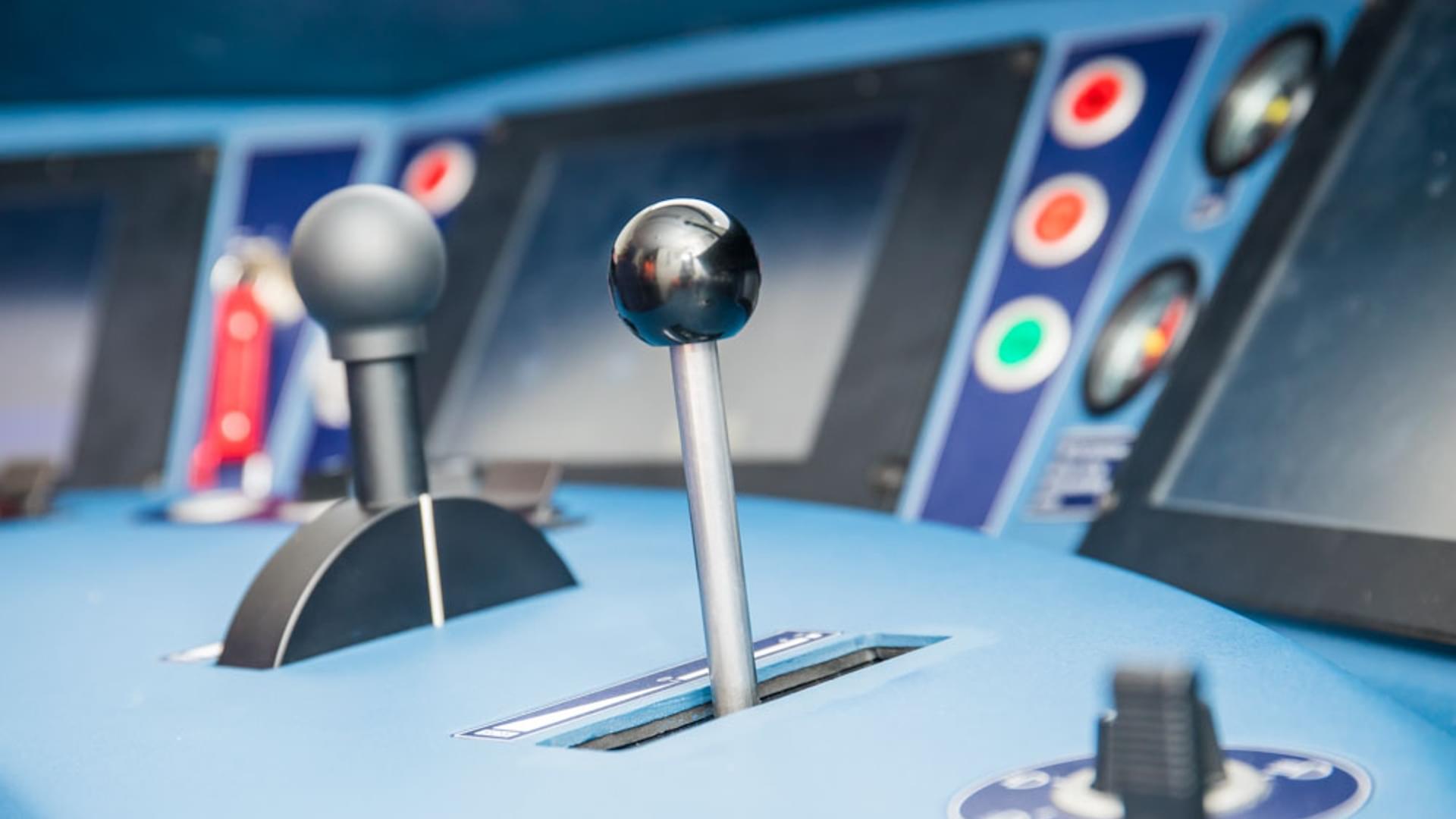
Was unterscheidet die Systeme von Knorr-Bremse vom Wettbewerb?
Wie so oft liegt unsere Stärke in der Individualisierung unserer Produkte an kunden- oder betreiberspezifische Anforderungen und Wünsche. Jedes Projekt ist unterschiedlich, jede Einbausituation verschieden. Natürlich kommen unsere Systeme mit der von Knorr-Bremse gewohnten Robustheit, Langlebigkeit und Zuverlässigkeit. Die Funktionssicherheit des Hebels hat schließlich direkten Einfluss auf die Fahrzeugverfügbarkeit. Die Verfügbarkeit, der im Motion Lead Kit verbauten Komponenten, gewährleisten wir im Übrigen über den gesamten Fahrzeuglebenszyklus.
Zu unseren Alleinstellungsmerkmalen gehören auch die integrierten und auf die Bremssteuerung abgestimmten, pneumatischen Elemente zur Regelung oder Vorsteuerung der Hauptluftleitung. Großer Pluspunkt von Knorr-Bremse: Kunden bekommen die MotionLeads zusammen mit der pneumatischen Bremssteuerung „aus einer Hand“.
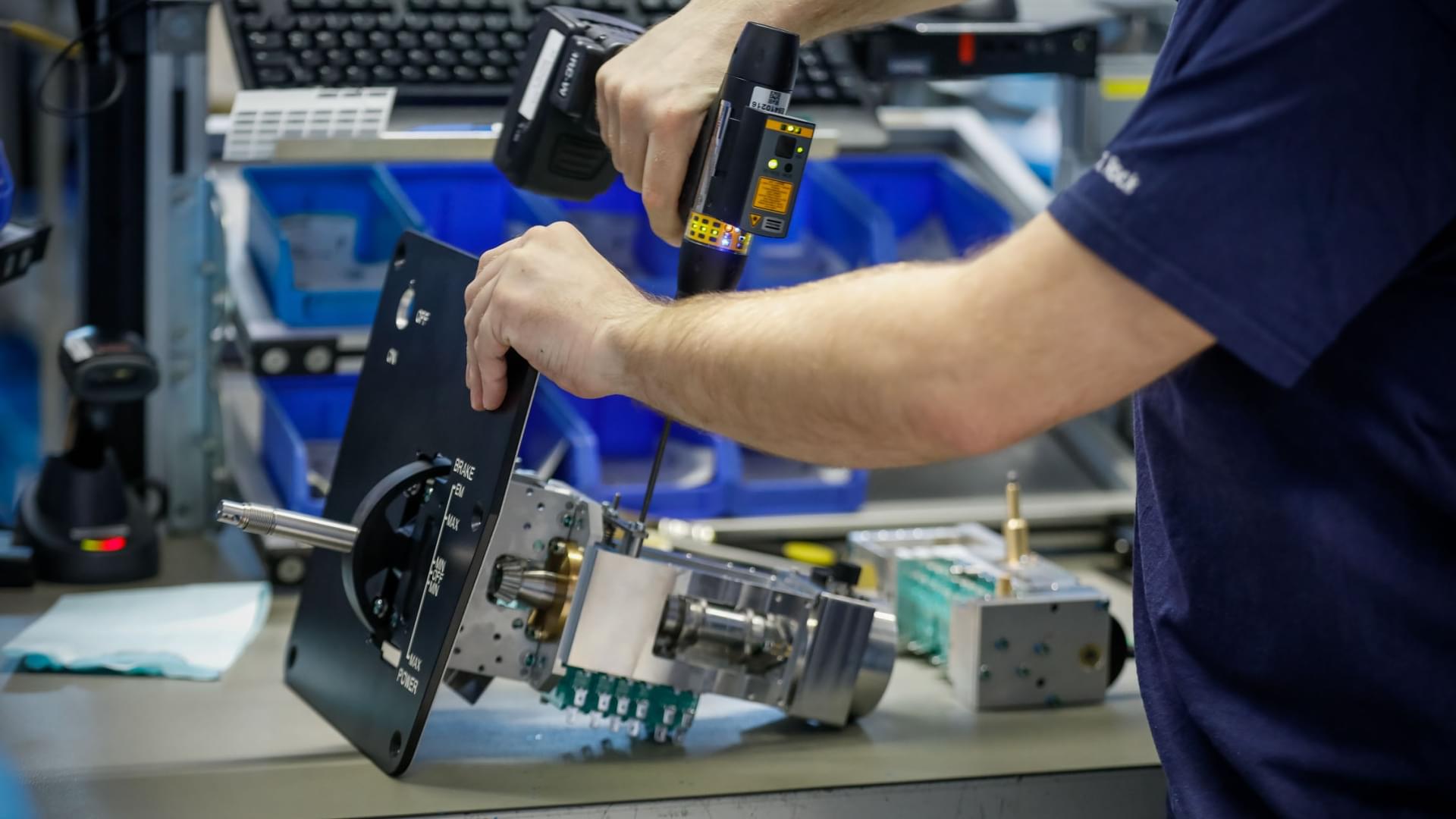
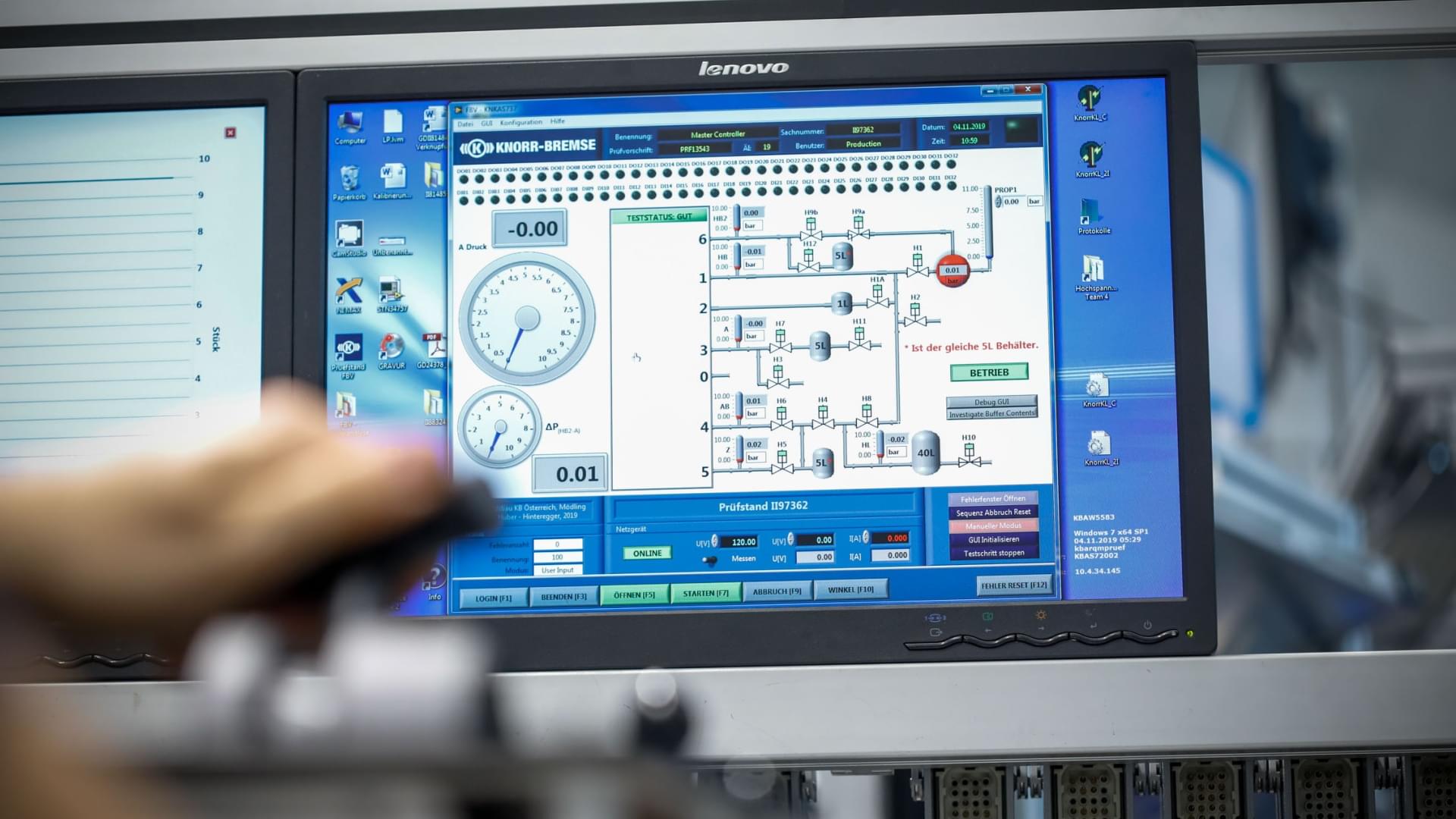
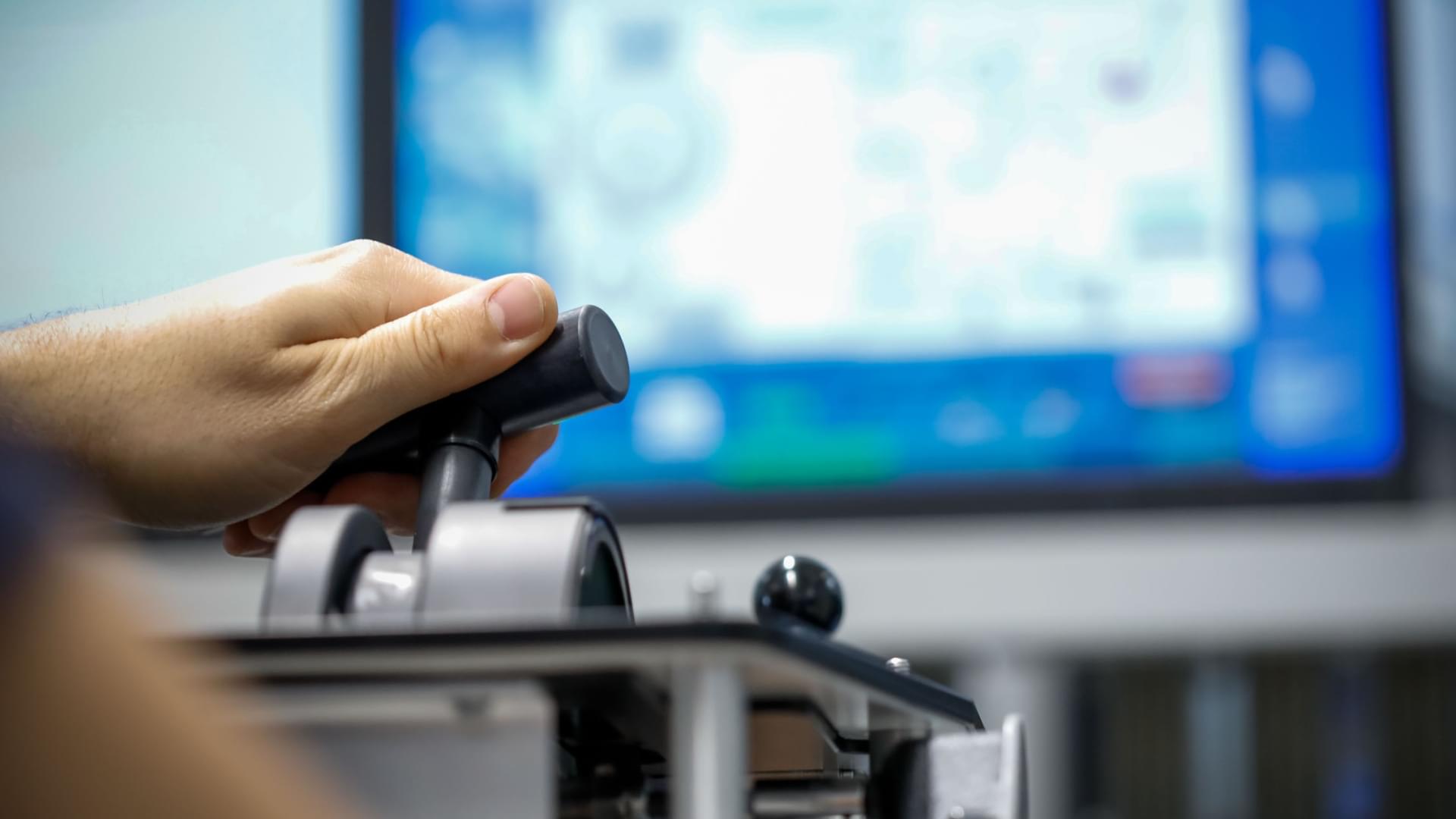
Was bedeutet „aus einer Hand“ – und was sind die Vorteile?
Gemeint ist, dass wir neben den elektrischen Signalen an die Bremssteuerung auch pneumatische Signale direkt an die Hauptluftleitungssteuerung übertragen – mit einem einzigen Hebel. Zudem kommt die gesamte Wirkkette vom Hebel über die Steuerung bis zur Bremse am Rad – und damit die Gesamtfunktionalität des Bremssystems – optimal aufeinander abgestimmt aus einer Knorr-Bremse Hand. Dadurch entfällt die Abhängigkeit von verschiedenen Lieferanten.
Warum sind kundenspezifische Anpassungen so wichtig?
Genauso wie die Fahrzeuge selbst sind auch die Führerpulte individuell konzipiert. Je nach Fahrzeuggattung unterscheiden sie sich erheblich. Oft müssen wir auch landes- und fahrzeugspezifische Vorgaben umsetzen oder verschiedene Griffformen wie Kugelgriffe, konische Griffe oder T-Griffe. Zum Beispiel sind Bedienkräfte oft je nach Einsatzort sehr unterschiedlich. Dazu kommen Hebel, die, wie etwa in Metros, permanent vom Fahrzeugführer bewegt und daher leichtgängig sein müssen. Anderswo, zum Beispiel bei Rangierlokomotiven, müssen Hebel hochpräzise und sehr feinfühlig ausgelegt sein. Manche Kunden wünschen Zusatzfunktionen, zum Beispiel ein Schloss mit mechanischer Verriegelung zum Schutz vor Missbrauch oder Fahrtrichtungsschalter mit den Stellungen Vorwärts, Neutral und Rückwärts.
Was für alle Projekte gilt: Die Einbauverhältnisse im Führerpult sind bei jedem Fahrzeug anders, Platz ist immer Mangelware. Deshalb ist unser Baukasten so wichtig: Er erlaubt maximale Flexibilität, damit wir die Platzverhältnisse trotz umfangreicher Funktionen optimal ausnutzen.
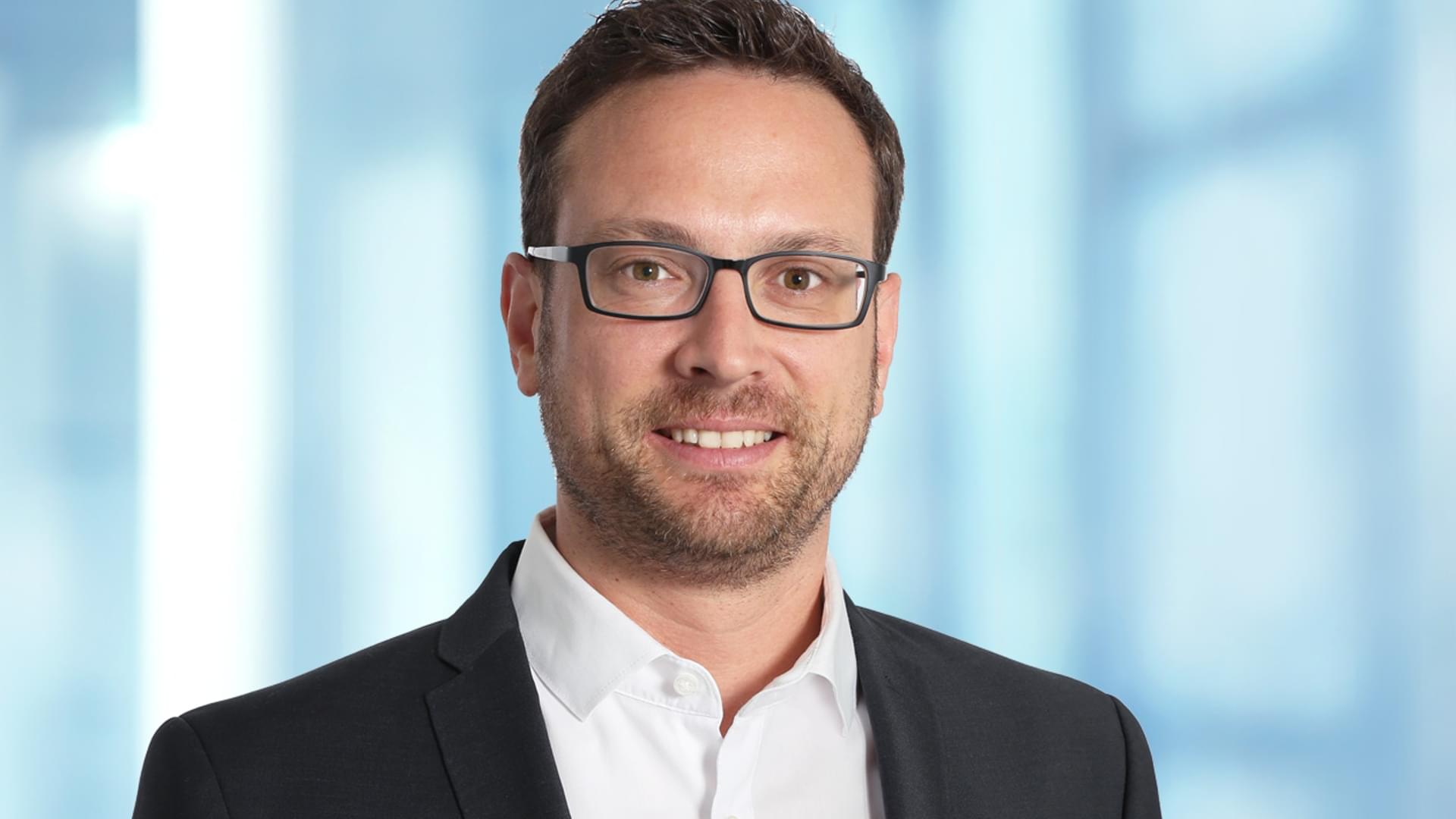
Dank des Baukastenprinzips sind wir – gerade auch im Vergleich mit dem Wettbewerb – sehr schnell. Eine 90-Prozent-Lösung können wir meistens schon nach zwei Wochen vorlegen.
Michael Holz – Teamleiter Development Mechatronics / Electromechanics
Wie funktioniert dieser kundenspezifische Anpassungsprozess – und wie lange dauert es von der Anfrage bis zur Auslieferung?
Dank des Baukastenprinzips sind wir – gerade auch im Vergleich mit dem Wettbewerb – sehr schnell. Eine 90-Prozent-Lösung können wir meistens schon nach zwei Wochen vorlegen. Schon zu diesem Zeitpunkt sind wir in der Lage, dem Kunden ein vorläufiges Einbaumodell für erste Einbauuntersuchungen zur Verfügung stellen. Nach dem „Design Freeze“ braucht es in der Regel nur wenige Wochen, bis die Stücklisten und Zeichnungen an die Produktion gehen. Unterm Strich können wir von unserem Produktionsstandort in Wien-Mödling aus innerhalb weniger Monate hinaus in alle Welt liefern.
Was macht die Zusammenarbeit zwischen dem Standort in Mödling und der Knorr-Bremse Zentrale in München so besonders?
Das Engineering in München und die Produktion in Mödling arbeiten mit hervorragendem Teamgeist und einem Austausch auf Augenhöhe zusammen. Wöchentliche Abstimmungstermine und regelmäßige persönliche Meetings erlauben eine direkte Rückkoppelung von Erfahrungen aus der Produktion in die Entwicklung. Wenn es Probleme gibt, packen wir sie unmittelbar gemeinsam an. Dank langjähriger Erfahrung der Mitarbeiter:innen, klar definierten Rollen und Kompetenzen sowie einer hohe Motivation quer durch die Organisation bekommen unsere Kunden stets einwandfreie Geräte geliefert.
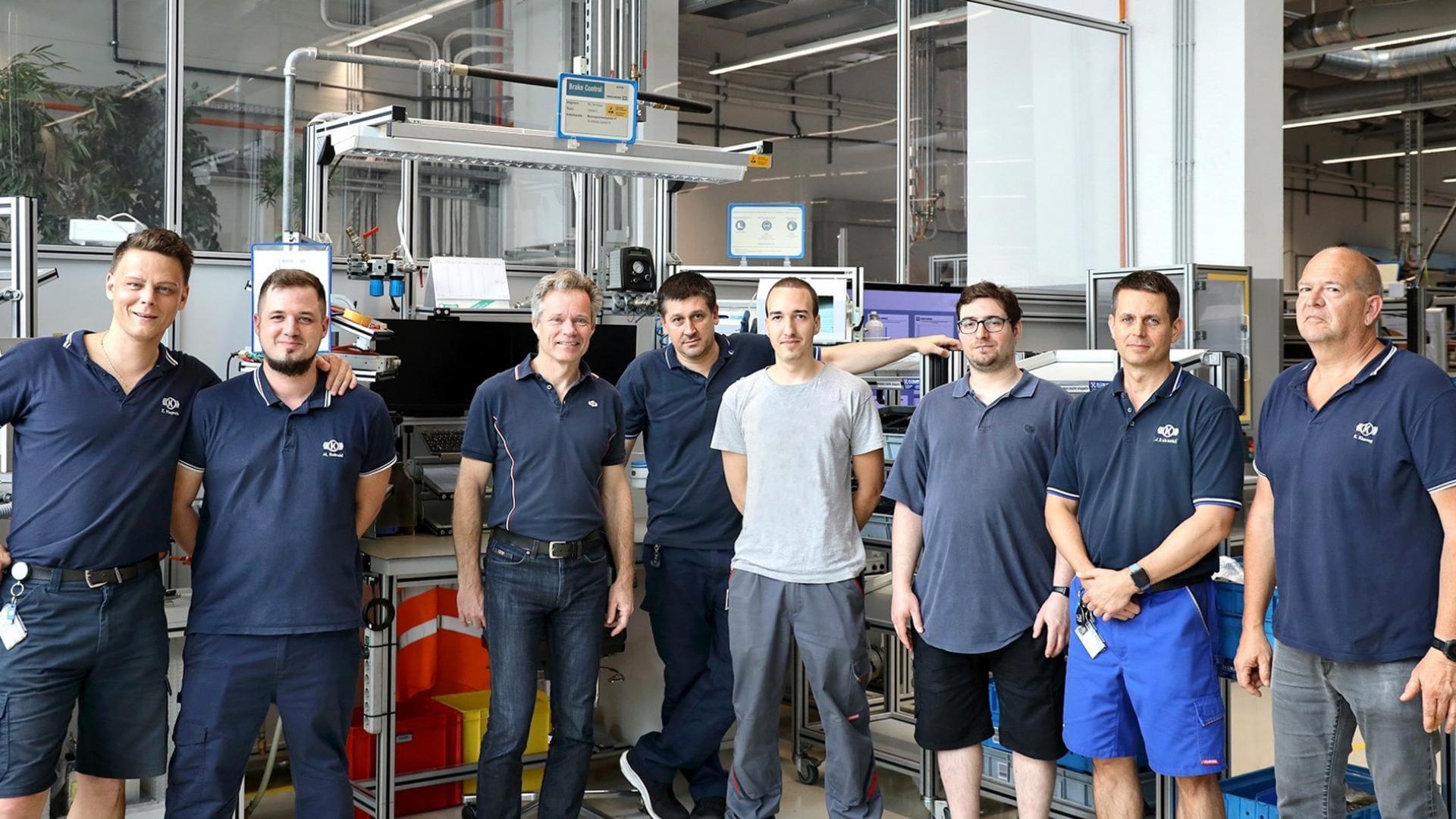
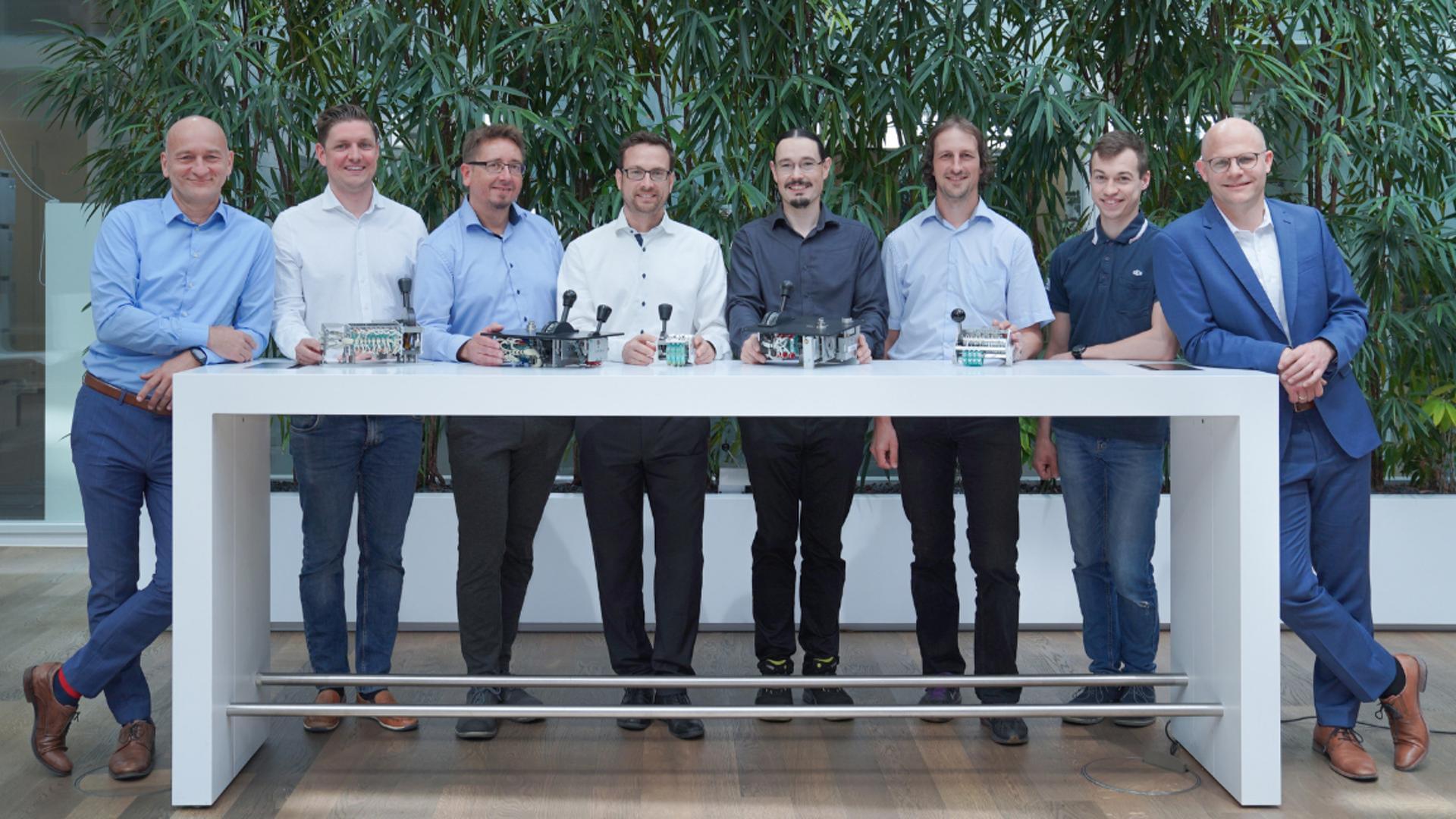
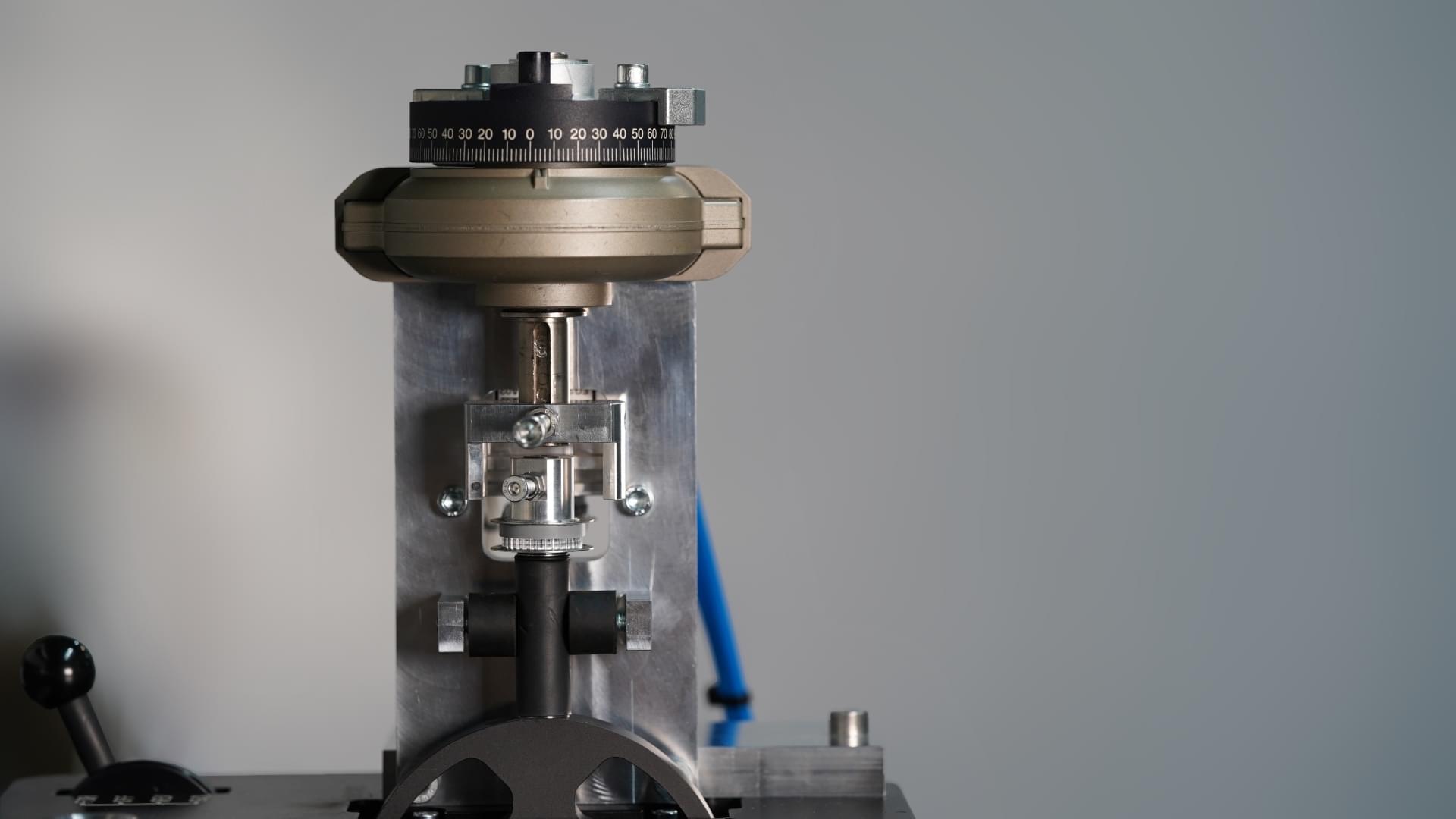
Welche Testverfahren durchlaufen die MotionLead Kits vor ihrer Auslieferung?
Selbstverständlich testen wir sie ausgiebig. Unsere automatisierten Prüfstände stehen für ein Höchstmaß an objektiven Ergebnissen. Um ihren Lebensdauertest zu bestehen müssen die Komponenten bis zu drei Millionen Betätigungen absolvieren, deutlich mehr als die im realen Betrieb auftretenden Belastungen. Auch nach einem solchen überstandenen Lebensdauertest muss ein Hebel noch ausgezeichnet funktionieren.
Doch gerade auch unsere Mitarbeiter:innen sind sich ihrer Bedeutung für die exzellente Qualität unserer Produkte und Systeme bestens bewusst. Alle Mitarbeiter aus Entwicklung und Produktion wissen, welch zentrale Rolle ein Fahr-/Bremshebel bei der Bedienung eines Fahrzeugs spielt. Er muss unter allen Umständen einwandfrei funktionieren. Alles andere hat einen unmittelbaren Fahrzeugausfall zur Folge. Mit Teamgeist meistern wir die alltäglichen Herausforderungen, erfüllen individuelle Kundenwünsche bestmöglich und optimieren unsere Produktionsabläufe permanent.