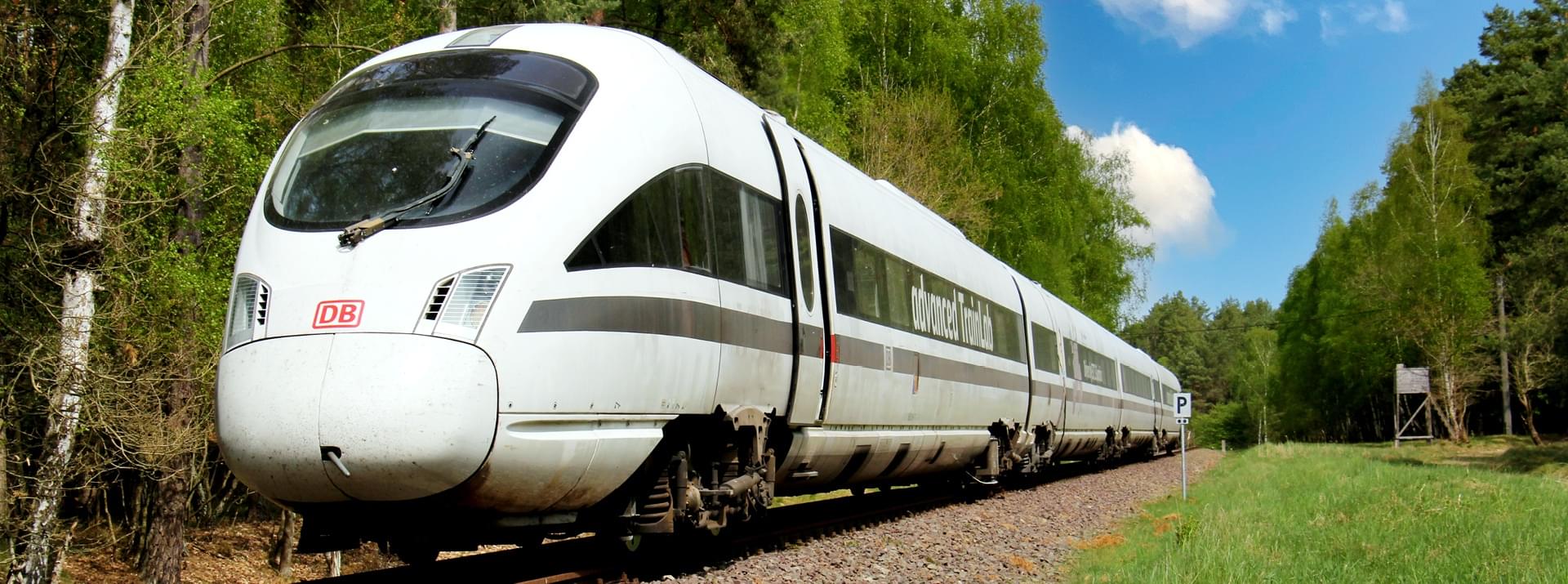
In 2018, Knorr-Bremse launched the Reproducible Braking Distance (RBD) development program. The program involves integrating a new type of deceleration control system with an improved wheel slide protection system and a train-wide adhesion management system with situational adaptivity. Together with a suitably adjusted signaling system, this combination of technologies enables trains to run at more frequent intervals (i.e. with shorter headways) but just as safely, even in adverse environmental and track conditions. This could enable more efficient utilization of existing rail infrastructure. Validations of individual RBD functions, as well as additional findings from test runs and field trials, are now available. Based on a real-world operating scenario, a new study quantifies the potential of these RBD functions for improving network capacity (nominal performance) and network stability (punctuality). It also includes a sensitivity analysis detailing the effects of different levels of RBD equipment within a fleet.
How reducing variance in train braking distances could increase the frequency of rail services
If you want to travel through London and have time to spare, take the car. But London car drivers need nerves of steel: In 2022 alone, they wasted 156 hours of travel time. London is not unique – traffic congestion is having similar impacts around the world. In second place is Chicago (155 hours), followed by Paris (138), Boston (134) and Bogota (122). The most gridlocked German city is Munich, with around 70 hours of travel delays. These figures from the INRIX Global Traffic Scorecard for 2022 reflect the downside of urbanization. If things stay as they are, the situation will soon become even worse.
Increasing the transportation capacity of local public transit services in particular will play a major role in any responses to this issue. Where the rail infrastructure in urban areas has already reached its limits, public authorities are left with two options: either to lay new track (a notoriously expensive undertaking), or to find ways to better utilize the existing rail infrastructure. Knorr-Bremse’s Reproducible Braking Distance (RBD) program represents a highly promising approach to the latter option.
The program focuses on the timing of the intervals between trains, known as headway times. Here, operational limits are determined by signaling technology, infrastructure, operating specifications and in particular, braking curves (braking distances). A not inconsiderable proportion of the margins currently priced into headway times is directly associated with highly variable braking distances, due to a combination of vehicle characteristics and adverse environmental and track conditions. Trains traveling at their maximum authorized speed should always come to a safe standstill within precisely defined limits, even when adhesion is poor.
Viewed from another angle, this gives rise to an attractive idea. If the variance in braking and stopping distances was reduced – that is to say, if braking distances were more consistent, hence reproducible – headway margins could be reduced without compromising safety. They could be optimized by adapting braking curves and deceleration parameters.
A combination of three key braking functions – specifically, a new type of deceleration control system, (DCC), an improved wheel slide protection system (WheelGrip adapt), and an enhanced, train-wide adhesion management system with situational adaptivity (ADM) – could act like the proverbial key in a lock. If this combination proves to be resilient, calculations of braking curves and deceleration could be based on higher deceleration values, reducing headway times without the need to increase physical braking performance. In turn, this would create additional capacity on existing infrastructure, which network operators could then “fill up” with more trains.
80809 München
Deutschland - Germany
carina.smid@knorr-bremse.com
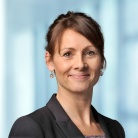
Findings from first DCC field trial: 100% availability and positive feedback from drivers
In real-world rail operations, it is axiomatic that conditions are never constant, let alone ideal. The performance of brake and bogie equipment – especially friction pairings of brake pads with brake disks – is never perfectly consistent during braking operations, and also depends on environmental conditions that change in the course of the day, such as temperature and humidity. Similarly, the effectiveness of brake actuators can vary, and wear and tear make it impossible to precisely calculate the diameters of wheelsets. All these variables result in non-negligible variance (“scatter”) in braking distances.
The job of the DCC is to decouple these variables from the deceleration figures which a train actually achieves. To do so, the DCC function constantly compares the train’s real-world deceleration with the anticipated effect of the braking force applied. It does so by using the acceleration sensors installed in each car and integrated with the brake control system. The brake control system continually compensates for the difference between the train’s calculated deceleration and the target (setpoint) value of the braking force required to decelerate the train. This drastically reduces the fluctuations in braking distances when braking from the same initial speed. This feedback loop results in statistically better braking behavior, which can in turn be used as the basis for calculating the headway times between two consecutive trains. Used in conjunction with the Controlled Emergency Brake (CEB) concept due to appear in future brake control systems, DCC is permanently active during both service and emergency braking maneuvers.
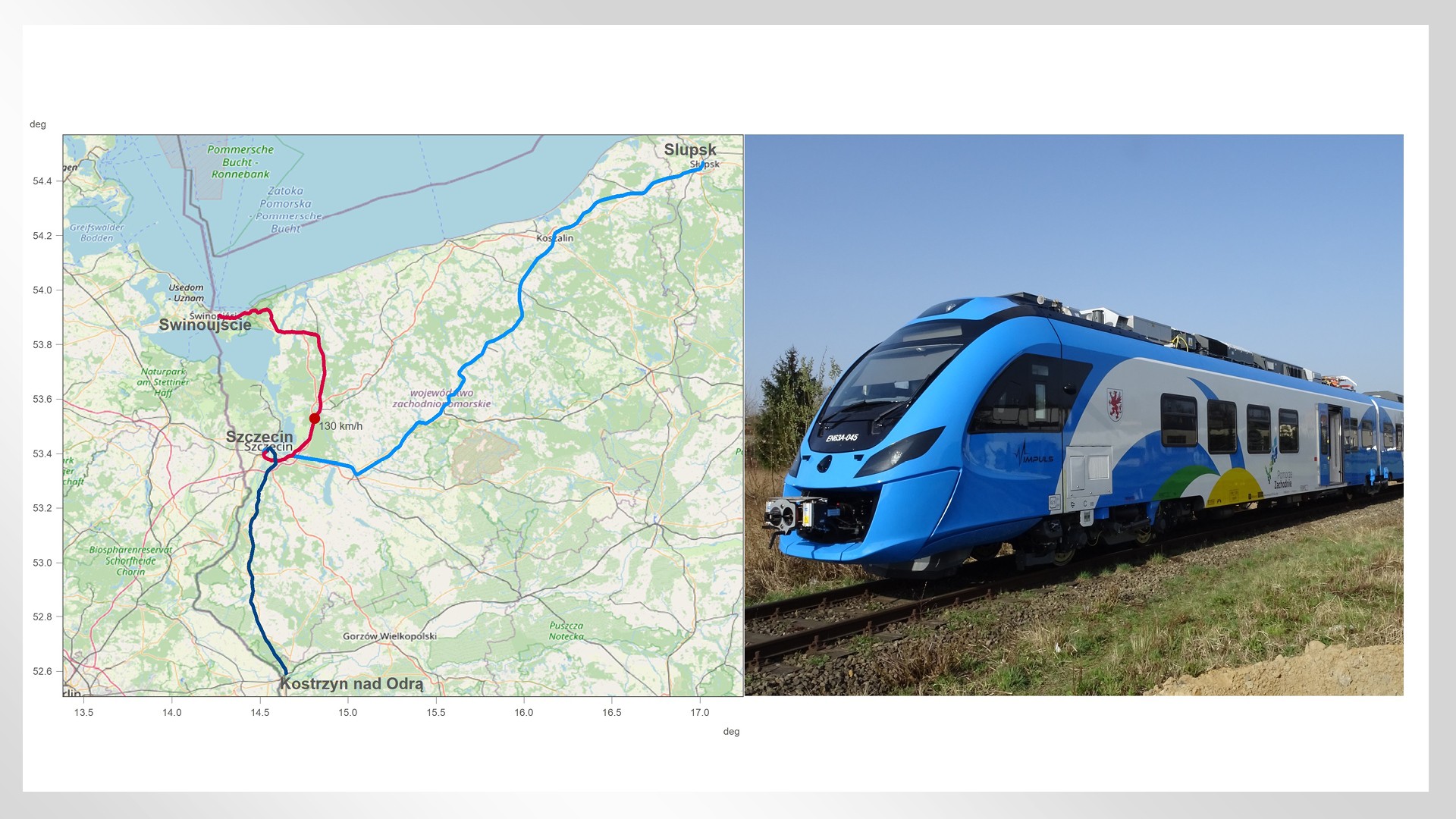
Successful tests in 2018 on the IK test track near Żmigród in Poland were followed by homologation and another two years of field trials in a NEWAG EN63A multiple unit equipped with DCC. The train provided passenger services on the Szczecin–Swinoujscie, Szczecin–Slupsk and Szczecin–Kostrzyn nad Odra lines. The trials focused on validating the full range of DCC functions, concentrating on their performance and operational availability when braking from speeds of up to 130 km/h, both in service braking mode (average deceleration values ranging from 0.35 m/s2 to 0.44 m/s2 on different tracks) and emergency braking mode.
Subsequently, a standardized questionnaire completed by 36 multiple-unit drivers provided insights from a train driver’s point of view. Of the 17 drivers who, according to their own statements, drove the field-trial vehicle occasionally or often, 53% rated its braking behavior as “better”, another 41% as “identical”. Stopping precision at the platform was rated as “better” by 47% of the drivers, and as “identical” by the remaining 53%. Equally important in obtaining a perspective are the excellent availability figures for the control system: Both the DCC and the CEB emergency braking function demonstrated 100% availability over the entire trial period.
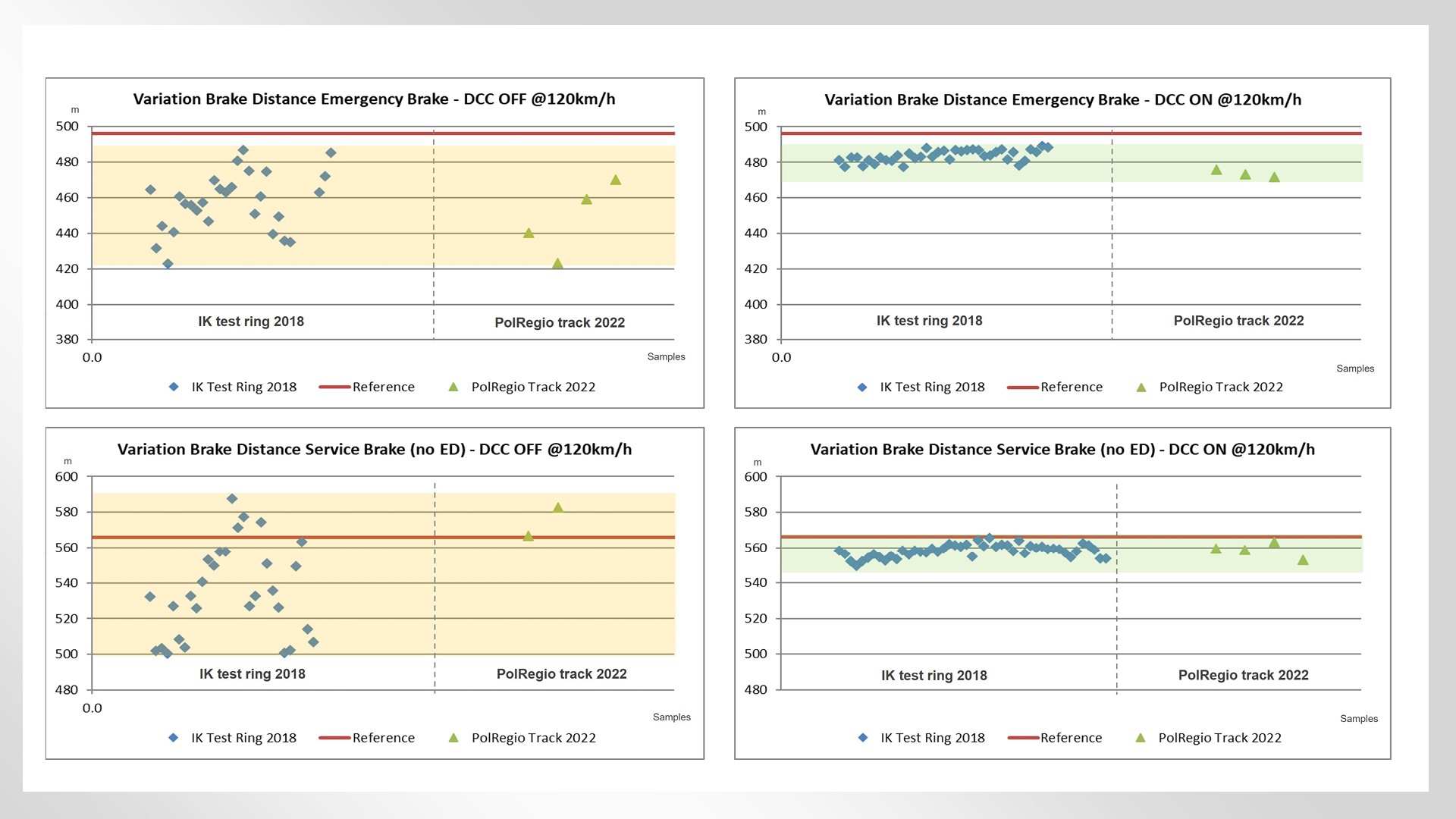
New functions subjected to integrated driving tests aboard advanced TrainLab (aTL)
While the technical benefits of DCC apply primarily to braking maneuvers in conditions of adequate adhesion, the WheelGrip adapt and Adhesion Management systems are designed for situations where wheel-rail adhesion is reduced. These situations are currently mitigated by operational measures and/or by the adoption of a defensive driving style by train drivers. In the future, and especially when considering automated train operation (ATO) at GoA3/GoA4 level, purely technical solutions should be capable of identifying and managing such situations. This is where the improved wheel slide protection system and the new train-wide adhesion management system with situational adaptivity perfectly complement each other.
To generate the input information required to develop these functions, Knorr-Bremse had already conducted a series of tests in 2019, as part of the Shift2Rail PINTA2 project in partnership with DB Systemtechnik. During the test campaign, foundational research was carried out aboard the advanced TrainLab (aTL), a DB Class 605 multiple unit converted into a test train, to reliably quantify the effects of train-wide sanding. The experiments focused in particular on tests in conditions of extremely low adhesion, on track prepared with leaves or paper (xnH, µ < 0.03). Braking maneuvers with and without an active sanding system made it possible to determine a reference condition for wheel-rail contact, as well as the effects of applying different quantities of sand (400g/30s, 2g/m, 4g/m, 7.5g/m of sand) .
Still in collaboration with DB Systemtechnik, Knorr-Bremse then took the next logical step – this time under the aegis of Shift2Rail’s PIVOT2 project – by conducting further tests in 2022. The test campaign focused on validating the newly developed WheelGrip adapt and ADM functions, as well as the DCC subfunction Deceleration Measurement (DMM) for measuring train-wide deceleration. The tests also examined the interactions between these functions. For the tests, additional electronic hardware was installed in parallel with the brake control hardware already aboard the vehicle, and the new functions and algorithms were implemented on the newly installed equipment. The output parameters manipulated for validation purposes included track conditions (prepared by applying water/soap, oil, and paper), and braking profiles that prioritized emergency braking and initial braking speeds (ranging from 60 km/h to 120 km/h). With respect to functionality, various ADM modes and wheel slide protection settings were tested.
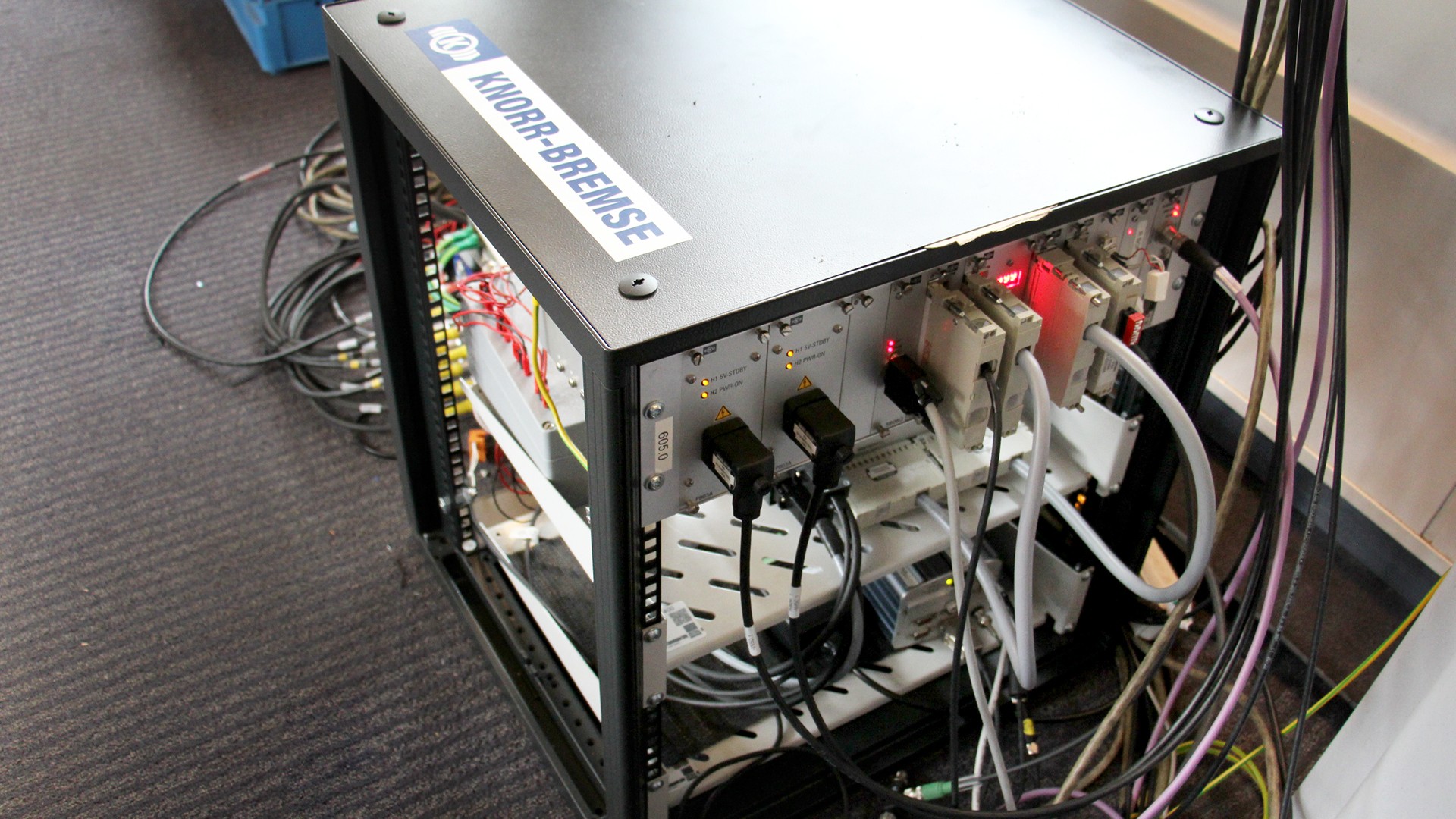
This made it possible to demonstrate, for the first time, the operation and benefits of ADM functions integrated into a standard ESRA brake controller and combined with a sanding system as a way to improve the wheel-rail adhesion of a multiple unit operating in real-world conditions. Using these functions resulted in significantly improved stopping distances. Furthermore, the results obtained from the real-world vehicle confirmed the results of previous tests on, for example, Knorr-Bremse’s ATLAS test rig.
Fig. 5 shows an example of the ADM system’s effect on a track prepared with oil. The red data set shows the deceleration figures for a test vehicle without adhesion management. The brakes are applied before the vehicle reaches the prepared section of track. When it reaches the oil preparation, optimal braking force transmission becomes impossible, as does the desired rate of vehicle deceleration. Only once the vehicle leaves the prepared section does adhesion return and braking deceleration start to increase again. But if adhesion management is activated (blue data sets), this sharp drop in vehicle deceleration is avoided; the system is capable of maintaining deceleration at a constant level over the oiled section of track. To compare the new system’s performance with braking performance in ideal conditions, the diagram also shows a data set measuring a braking maneuver on dry track (black data set). Despite a significant improvement in braking performance, it is not possible to achieve nominal braking deceleration using the adhesion management system alone, because of the drastically degraded adhesion conditions. But by using all RBD functions simultaneously, it should be possible to achieve further improvements.
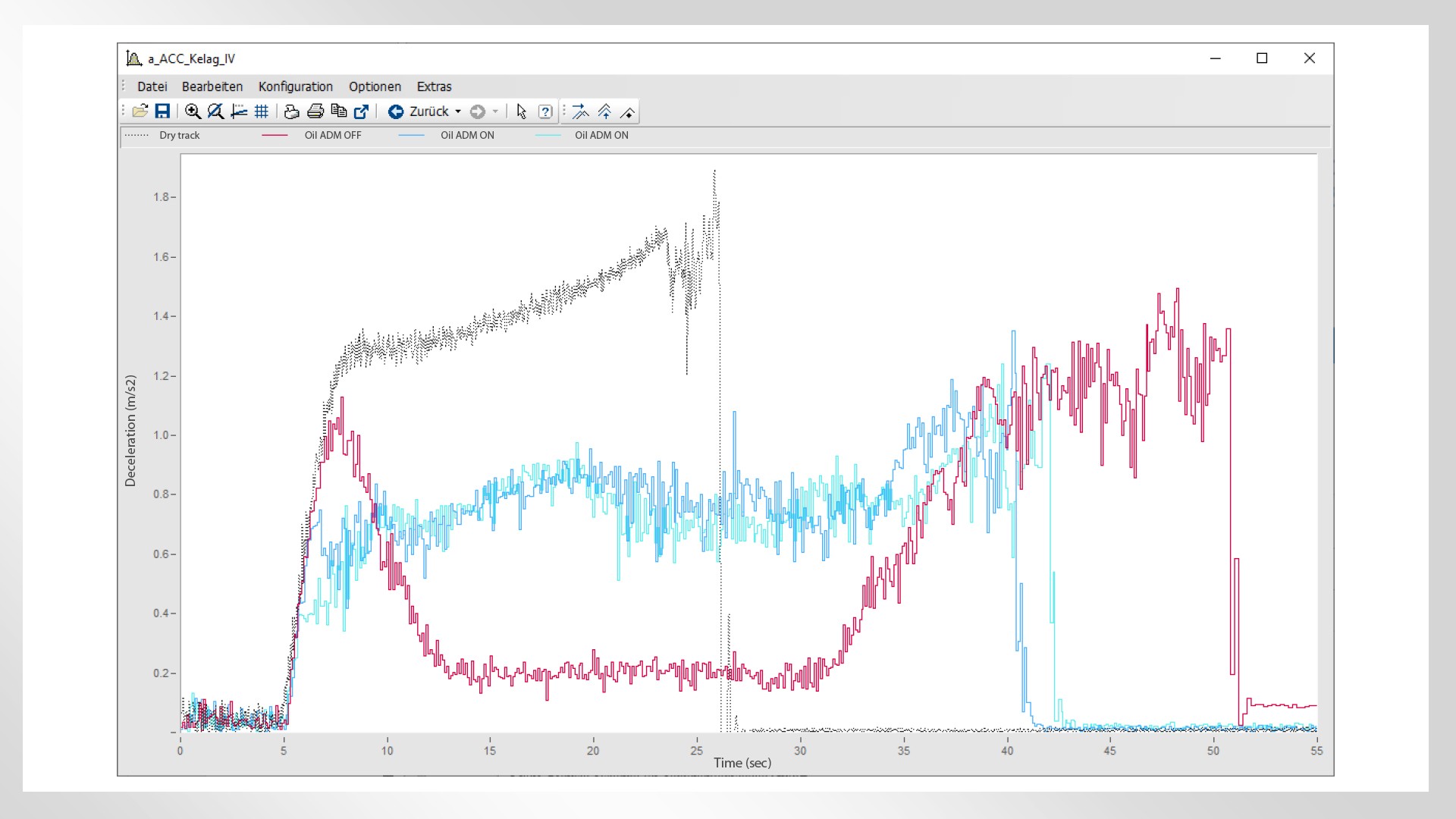
In addition, tests involving the use of WheelGrip adapt confirmed the latter’s advantage over existing wheel slide protection systems – an advantage already demonstrated in passenger coaches – in a multiple unit. In a system with the same performance rating, operating in UIC-compliant reduced adhesion conditions, the new algorithm resulted in improved braking performance in extremely low adhesion conditions (xnH). On average, over the test campaign as a whole, the system was able to achieve improved deceleration compared with existing systems, especially in this low adhesion range (initial adhesion <5%). Fig. 5 shows examples of the mean vehicle deceleration achieved over the prepared section of track in xnH conditions as recorded by two consecutive series of measurements. In the course of the tests, a sequence of emergency braking maneuvers was performed in both directions of travel with a different wheel slide protection configuration in each case. As the vehicle repeatedly drove over the test section while braking, it became clear that the mean deceleration steadily improved. In each series of tests, a new preparation was applied to the rails prior to test 1 and test 16. The metrics show that higher deceleration can be achieved in similar adhesion conditions using the adaptive WheelGrip adapt wheel slide protection system. Performing two series of tests in different initial directions of travel confirms the directional independence of the result.
With respect to DCC, the main test focus was on validating the DMM subfunction –integrated into a prototype of Knorr-Bremse’s new CubeControl brake control system – in a real-world multiple unit. More specifically, this refers to the CubeControl’s local measurement of deceleration, the latter’s automatic calibration in operation, plus the calculation of a train-wide deceleration value based on the information supplied by the interconnected local control units. The outcome of the test showed that the function delivered stable, plausible results, although it also identified potential for further improving signal quality and DMM precision.
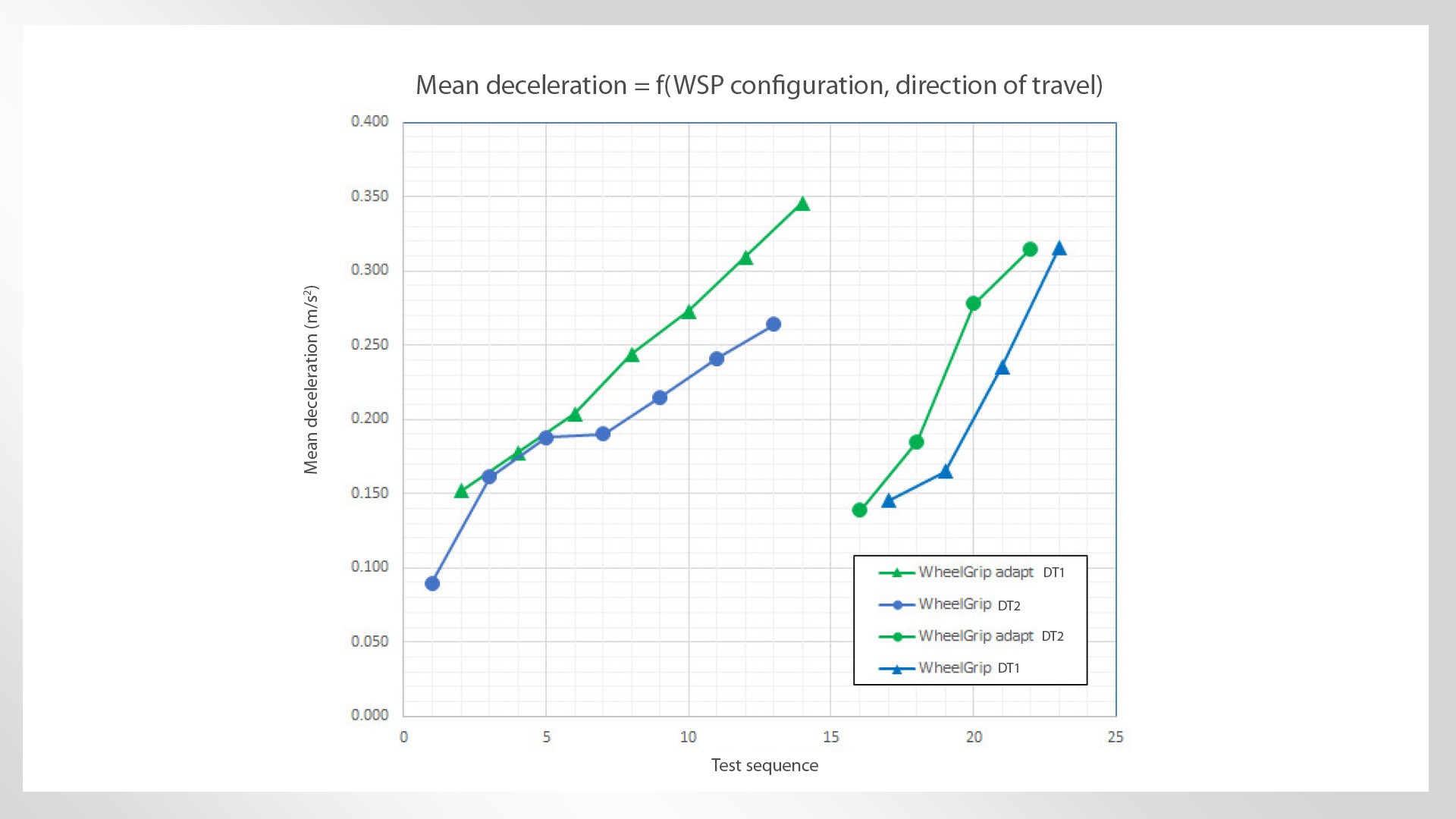
RBD potential simulated for first time on real-world transit network with fleet equipped to different levels of RBD functionality
Although they can be demonstrated in test runs, the practical benefits of these new functions only really become apparent when in operation aboard an actual passenger train. At the start of the development project, Knorr-Bremse and IFB Institut für Bahntechnik GmbH began by assessing the potential of RBD using generic operational simulations. Early results already suggested that RBD was capable of reducing theoretical train headway times on dry track by the following margins: metro: 9–19%, suburban rail: 9–16%, regional rail with multiple units: 1.5–4%, and high-speed rail (China): up to 20%. In reduced adhesion conditions, the margins were 10–13% for metro, 10–12% for suburban rail, and 4–7% for regional rail with multiple units. High-speed trains (China) achieved a similar margin to dry track: up to 20%.
Knorr-Bremse then took the next logical step in collaboration with rail consulting firms NEXTRAIL and VIA-Con, carrying out a detailed study to quantify the potential of RBD functions using the example of an actual rail network. To do so, a comparative scenario and an RBD-optimized scenario were simulated for braking maneuvers in both normal conditions (“dry track”) and reduced adhesion conditions (“wet track”), and the resulting headway times were calculated. The simulations were based on Hamburg’s suburban rail network, taking into account automated train operation (ATO over ETCS L2, GoA2) as currently projected for the network. The results reconfirmed the orders of magnitude achieved in the 2019 study of RBD potential: RBD can reduce minimum headway times by valuable seconds while preventing any deterioration of punctuality in adverse environmental conditions.
It is already well known that technical train headway times (TTHT) can be significantly reduced with the help of ETCS block compression. But as ETCS block lengths are steadily minimized, there will come a time when this option is exhausted. But if, in addition, RBD is used to cut down platform approach times, it should be possible to further reduce supposedly optimized TTHT. According to the simulations, it would be realistic to expect mean TTHT reductions of 3% on dry track and 9% on wet track (in degraded adhesion conditions).
On dry track, this equates to improving nominal performance (network capacity) through a combination of shorter TTHTs with improved service quality/punctuality by 12 percentage points (corresponding to just under 10% by reference to the initial calculation). For the Hamburg City region, this represents 1.5 additional trains per hour and direction of travel. On wet track, the improvement would be as much as 26%, corresponding to a nominal performance almost identical to that on dry track.
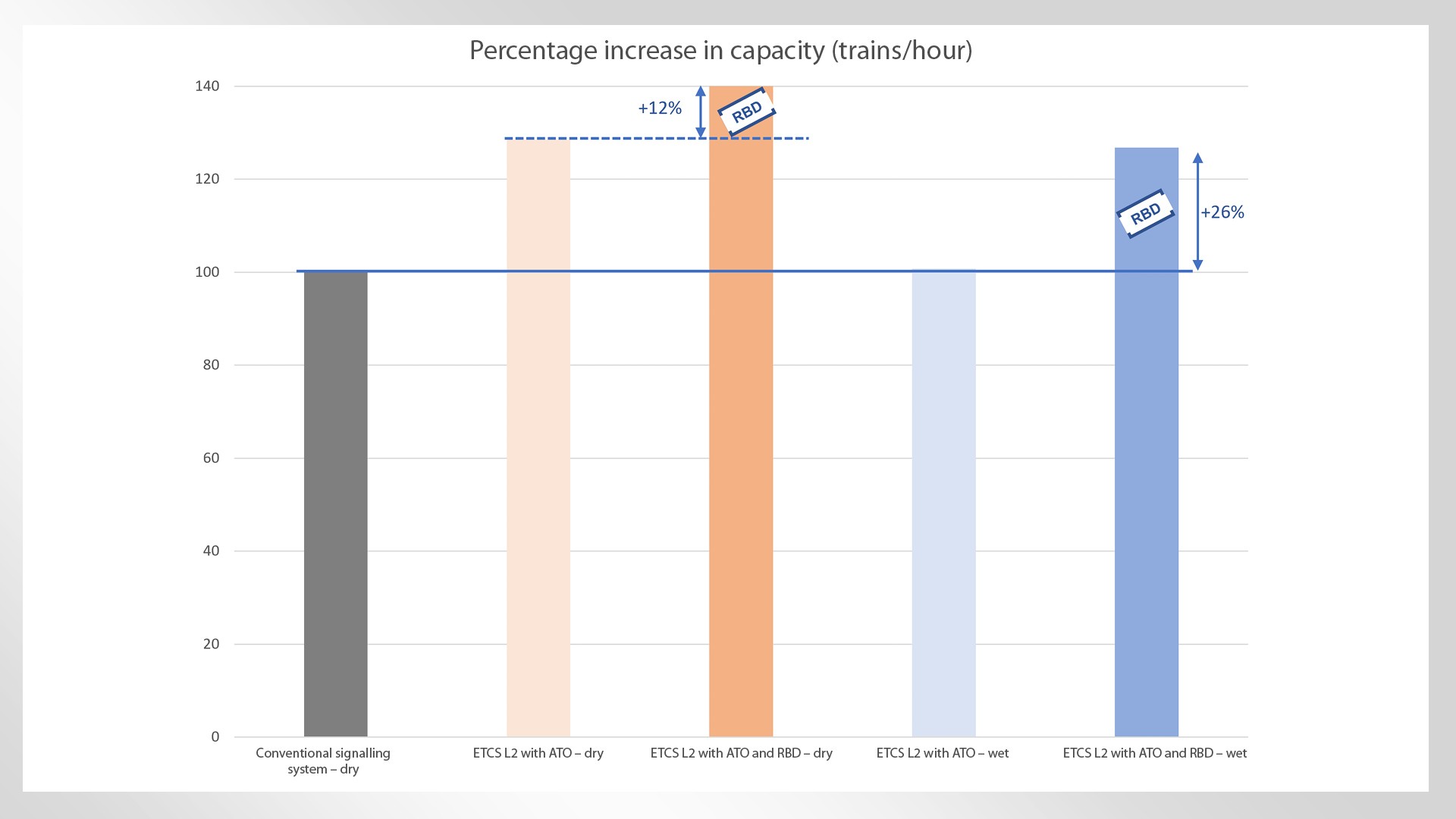
With respect to service quality/punctuality (in ATO over ETCS Level 2 with and without RBD), RBD can reduce the total volume of uncompensated delays on dry track by 18%. Three-minute punctuality can be improved by one percentage point. On wet track, RBD can reduce the total volume of uncompensated delays compared to wet track without RBD by more than one half (-57%). This essentially means that a level of punctuality similar to dry track is feasible on wet track.
Because it is unreasonable to assume that every vehicle in a train fleet will be simultaneously upgraded to full RBD functionality, the next step was to quantify the benefits of RBD by performing a sensitivity analysis for a given suburban rail fleet equipped to different levels of RBD functionality (25%, 50% and 100%).
Taking into account existing reserves in the timetable, a train equipped to a level of RBD functionality of around 50% achieves comparable service quality to a train equipped with full RBD functionality. On the other hand, equipping a train with just 25% of full RBD functionality only has a very minor effect on 3-minute punctuality.
The effect on the network’s nominal performance (capacity) turned out to be more or less linear: Where trains are fully equipped with 100% RBD functionality, nominal performance is 10% higher compared with trains that are not equipped with RBD. When equipped with 50% RBD functionality, the increase is 5%; when equipped with 25% RBD functionality, the improvement is just 2.5%.
Authors: Jörg Braeseke; Dr. Marcus Fischer; Ulf Friesen; Johannes Graeber
Litrature:
[1] INRIX, „Global Traffic Scorecard 2022“, https://inrix.com/scorecard/
[2] Ulf Friesen, Ralf Furtwängler, Norman Kreisel, Jörg Braeseke, Dariusz Ciesielski: Verzögerungsgeregeltes Fahrzeug ermöglicht ein stabileres Bremsverhalten in allen Geschwindigkeiten. ZEVrail, 02/2020
[3] Dr. Marcus Fischer, Kurt Haselsteiner, Dr. Ferenc Szekely, Sebastian Heinz, Felix Kröger. Mehr Mobilität auf der Schiene: Erhöhung der Transportkapazität durch Optimierung des Kraftschlusses. ZEVRail, 10/2020
[4] Kerstin Büker, Dr. Marcus Fischer, Johannes Gräber. Verbesserung von Kapazität und Betriebsqualität durch reduzierte Streuung der Bremswege. ETR 11/2022