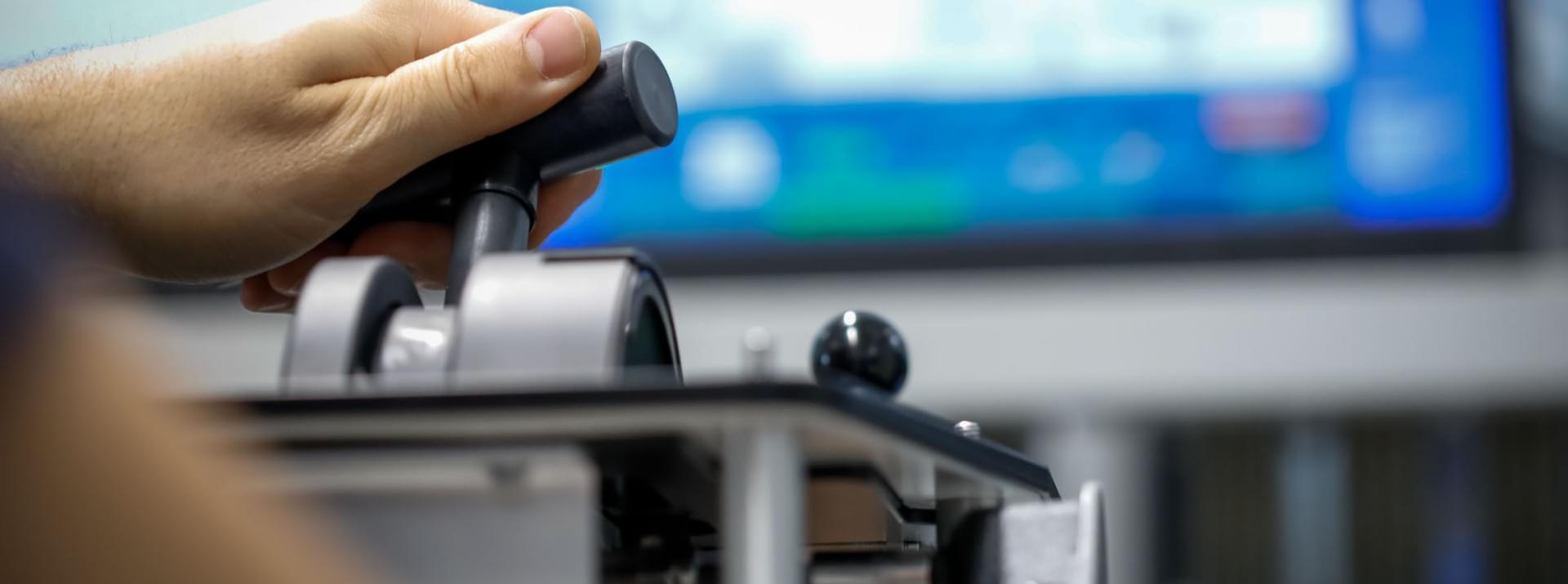
Train drivers around the world use MotionLead levers to accelerate and brake their vehicles. MotionLead systems essentially “translate” a driver’s desire to brake or accelerate into braking and traction commands. Because the systems are based on a modular principle, Knorr-Bremse can adapt the control levers to operators’ specific requirements. But what exactly is MotionLead? We asked our Munich-based expert, Michael Holz…
What tasks and functions does MotionLead perform?
MotionLead is our name for the human-machine interface installed in the driver’s cab, which enables a rail vehicle driver to communicate with his or her vehicle. This is where all driving and braking operations originate. MotionLead takes the form of a traction and/or braking lever that transmits the driver’s wishes to the vehicle’s traction or braking control systems, depending on the lever’s position. The various levers can be used for braking (MotionLead Brake), traction (MotionLead Traction) or as a single, combination lever for driving and braking (MotionLead Master).
KONTAKT
80809 München
Deutschland - Germany
sales.sfs@knorr-bremse.com
What does MotionLead consist of?
MotionLead is made up of a large number of components, which can be assembled entirely as the customer wishes. The basis is our MotionLead Kit, a comprehensive, standardized modular toolkit with numerous individual elements. The lever you see in the driver’s cab is just the proverbial tip of the iceberg – there’s much more beneath the surface. Below the driver’s console, large numbers of mechanical, electrical and pneumatic components are used to transfer signals based on the lever’s position. This is done via a lot of electromechanical switches and an angle sensor. It’s also possible to use pneumatic pressure controllers to regulate the pressure of the master brake line. In emergencies, an emergency braking valve – usually built into the system – can directly vent the main air pipe. If required, we can incorporate a wide range of accessories into the lever, such as locks, interlocks, additional buttons, or lighting. In some cases, we also fit levers with a “dead man” function – an electrical safety device, so that if the train driver doesn’t regularly operate the lever, the braking system triggers emergency braking.
The toolkit is very flexible, so we can combine its subfunctions in all sorts of different ways. Because we use standard parts to do this, we’re talking about higher quantities, meaning we can offer our customers cost benefits. What’s more, the various functions are already prequalified, so we don’t need to obtain project-specific approvals. This cuts down time to market.
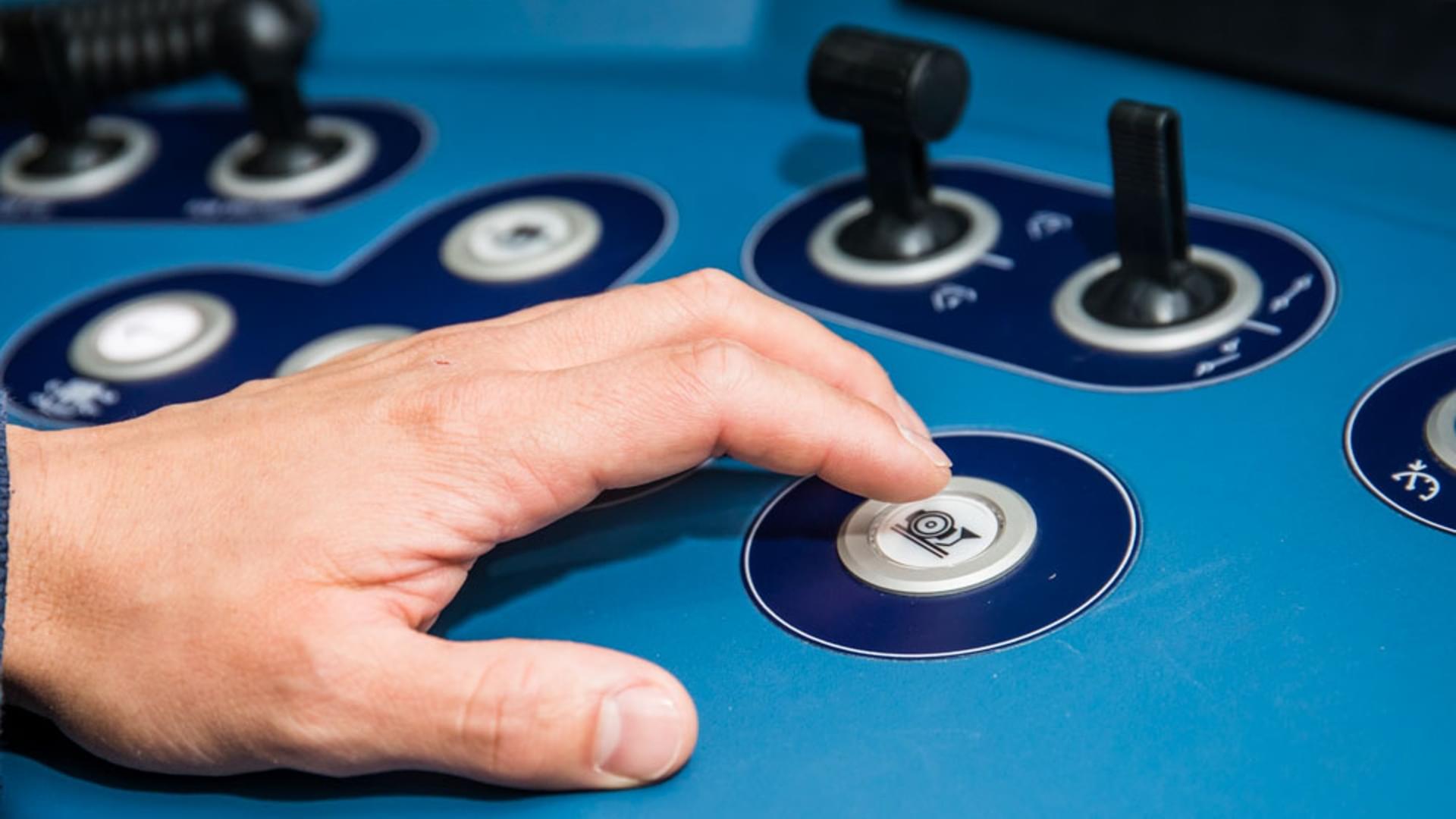
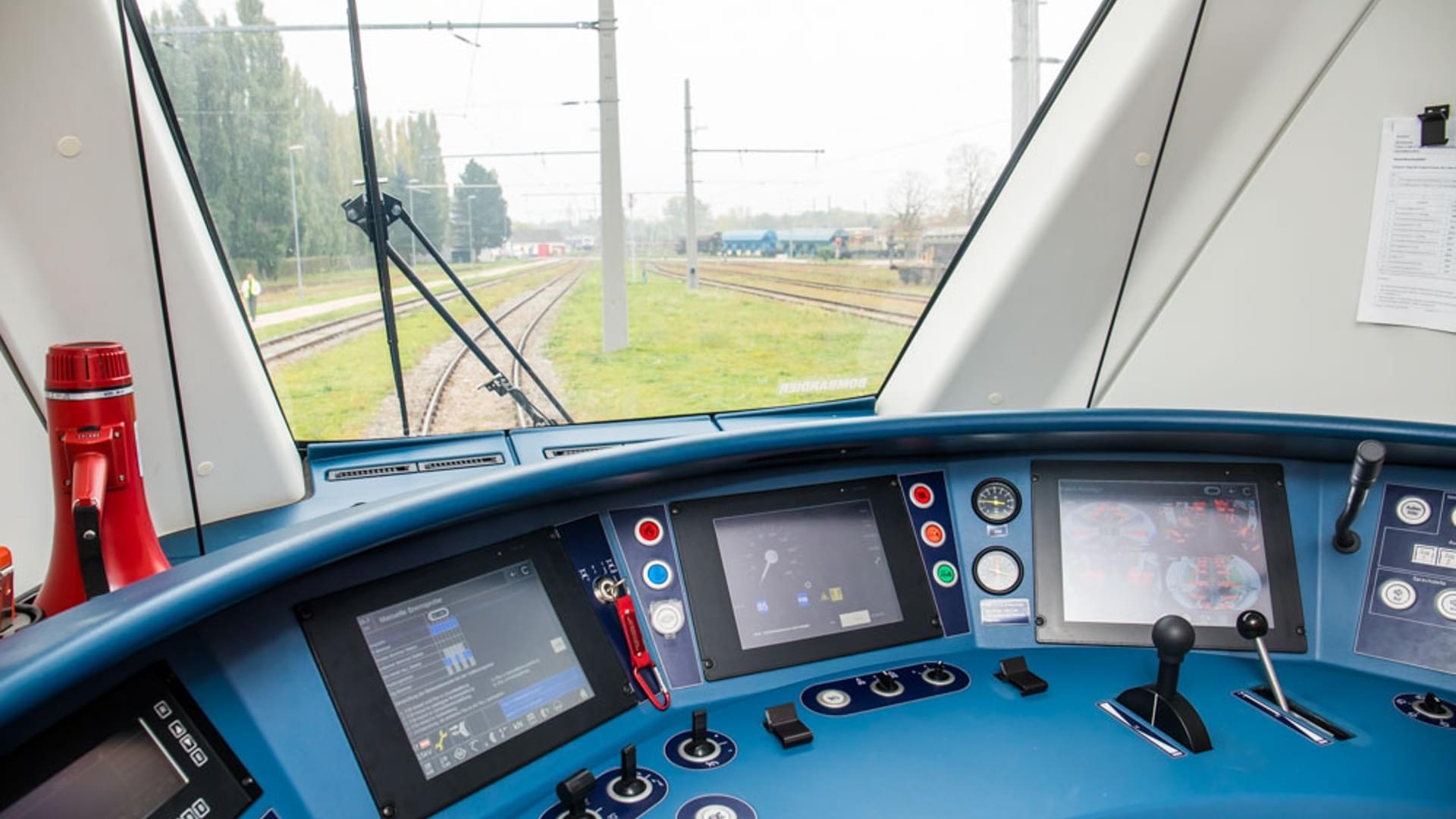
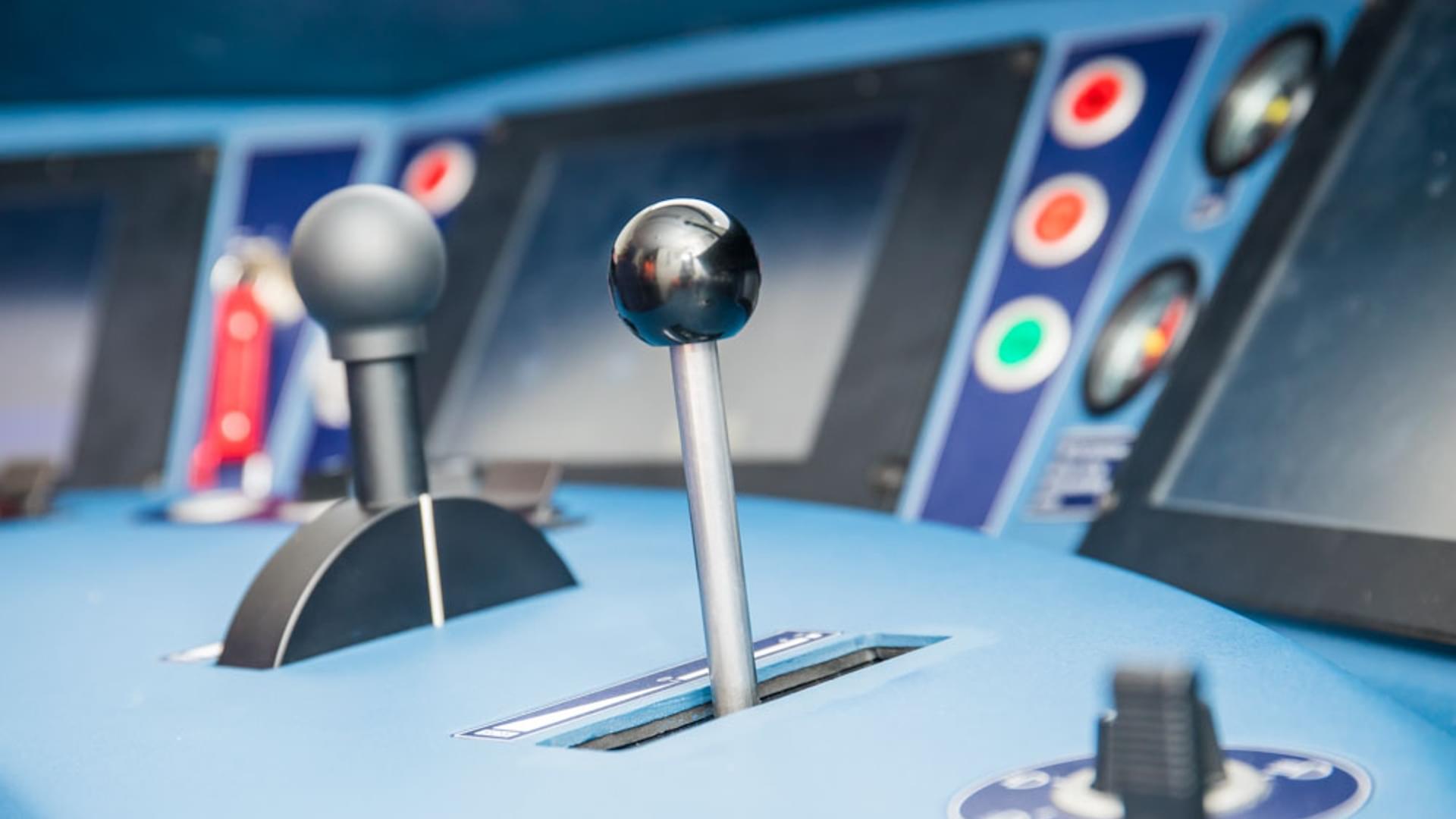
What distinguishes Knorr-Bremse’s systems from the competition?
As so often, our strengths lie in the ability to customize our products to meet customer or operator-specific needs and wishes. Every project is different; every installation has its own special characteristics. Of course all our systems feature Knorr-Bremse’s usual robustness, durability and reliability. After all, the lever’s operational reliability has a direct impact on the vehicle’s availability. Speaking of availability: We also guarantee that the components in our MotionLead Kit will be available over the vehicle’s entire life cycle.
Our USPs also include the integrated pneumatic elements for controlling or pilot-controlling the main air pipe; they’re matched to the respective brake control system. The major advantage of working with Knorr-Bremse? Customers get their MotionLead solutions and pneumatic brake control systems from a single source.
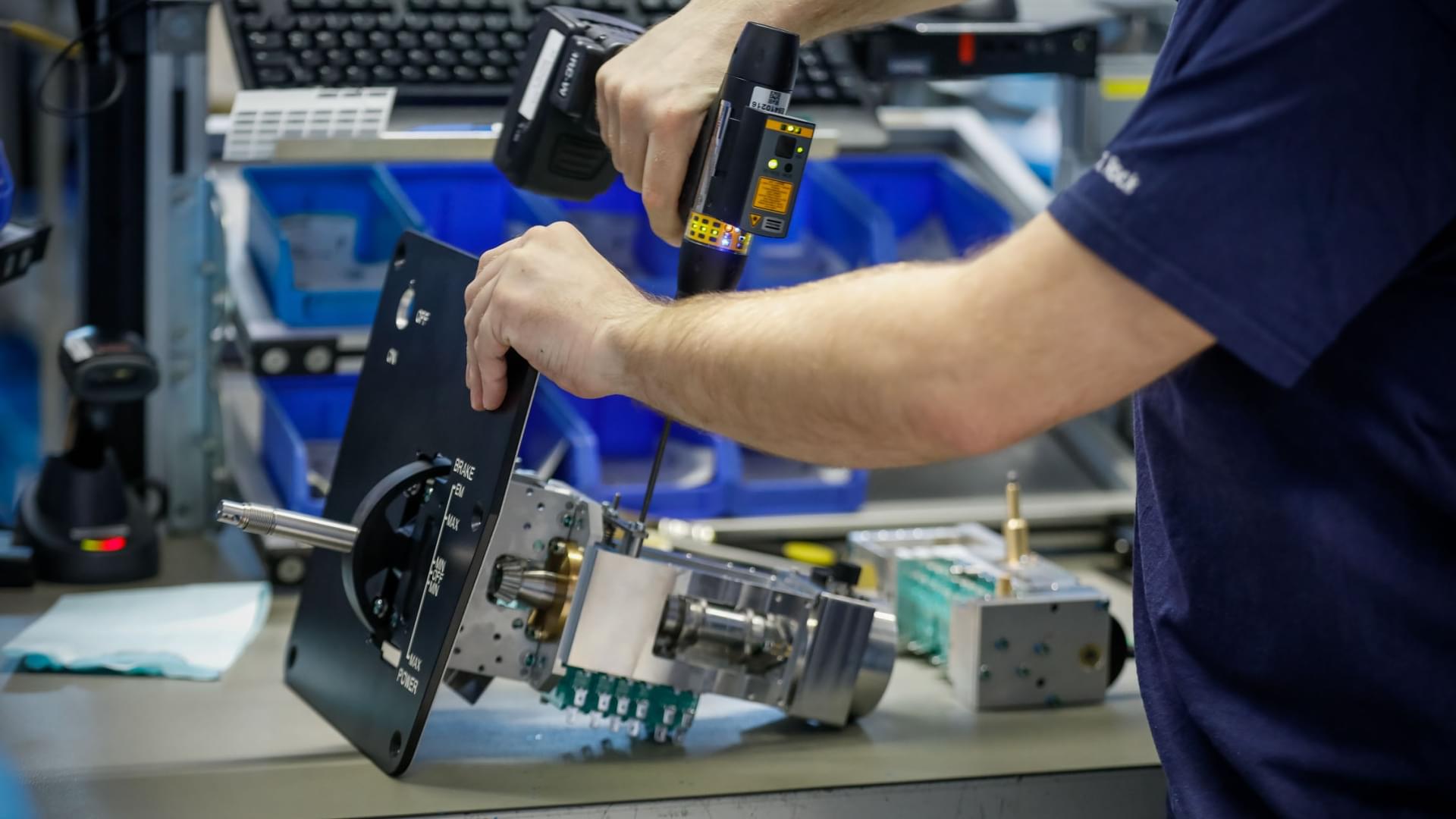
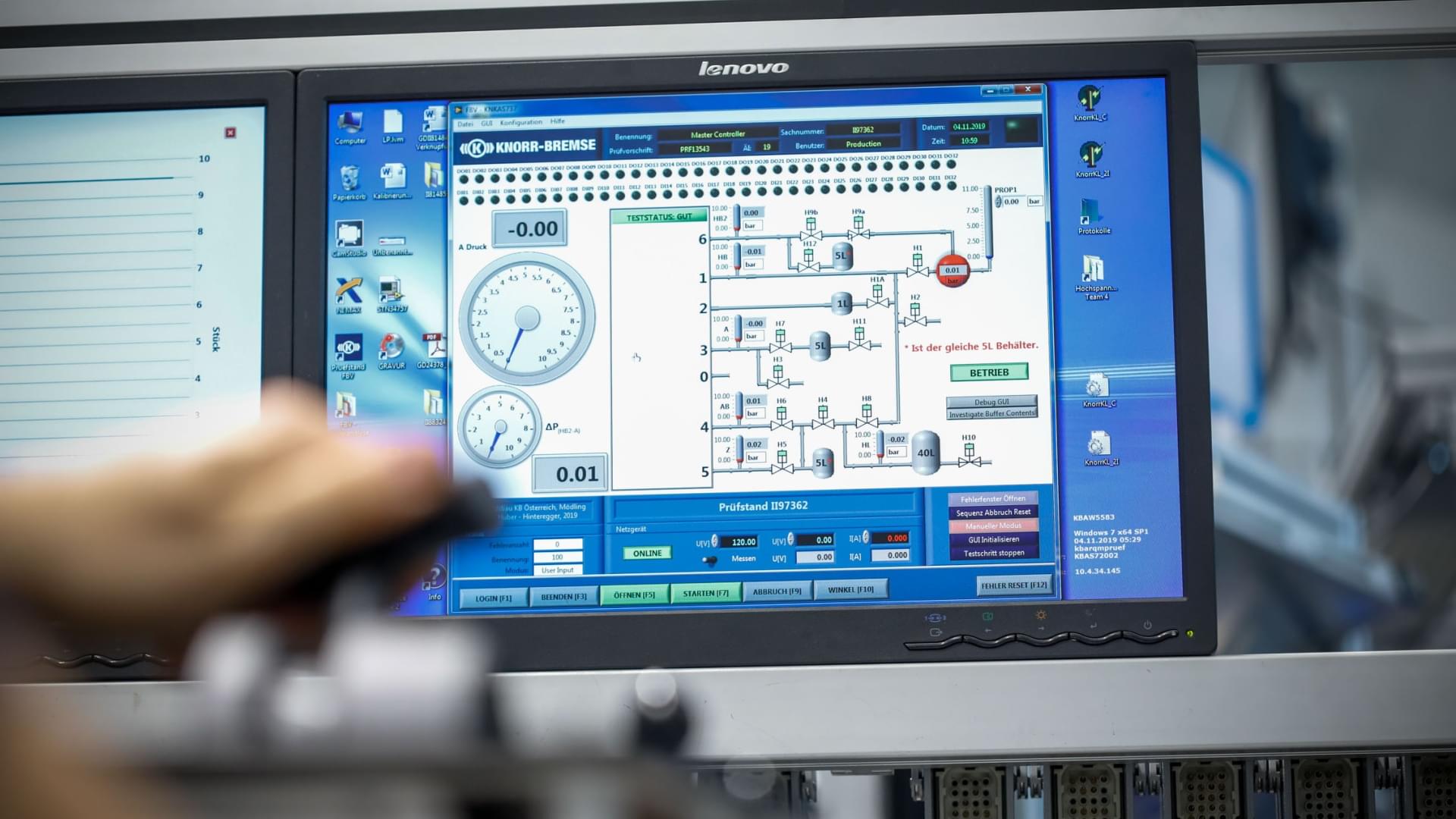
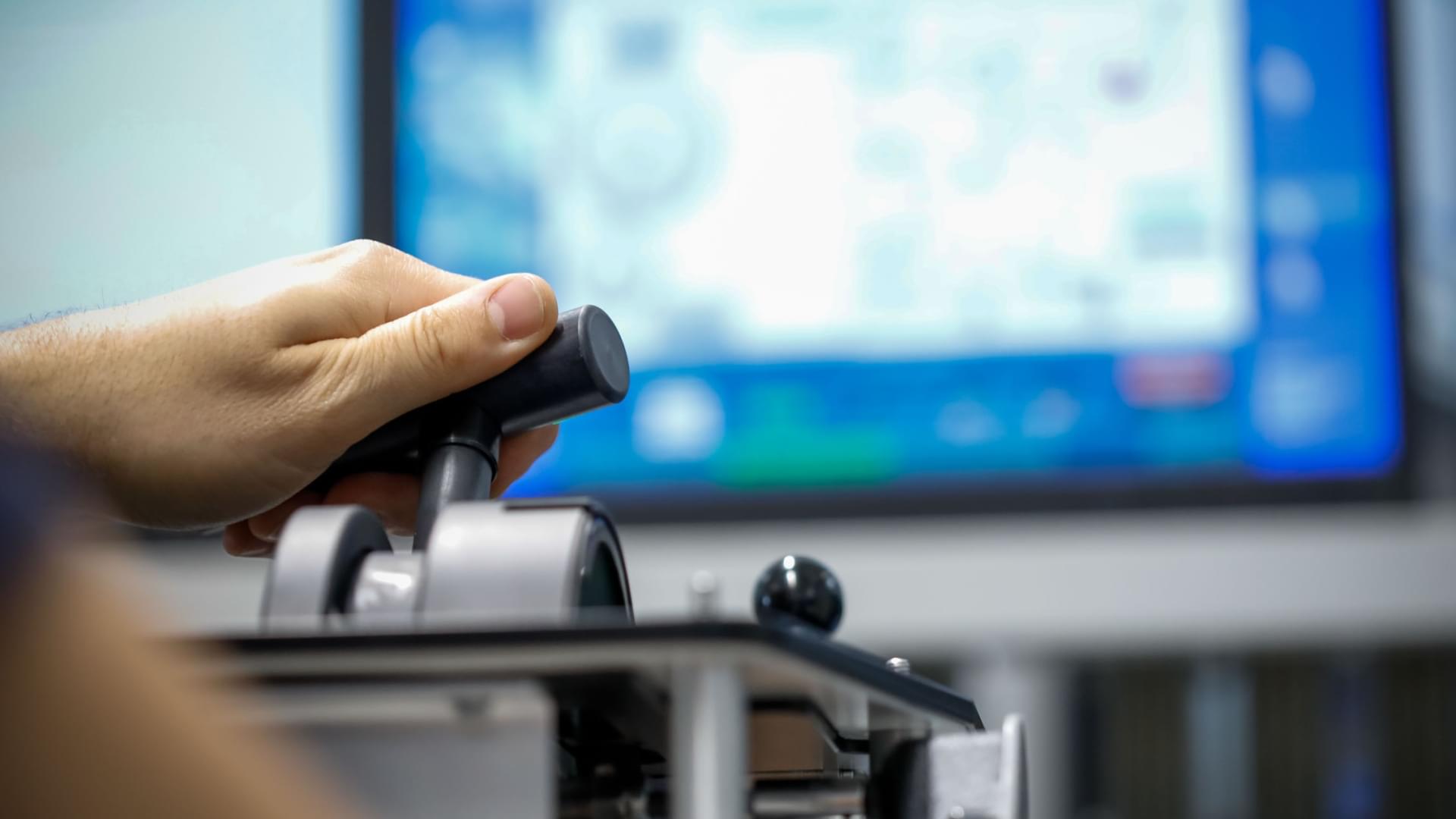
What does “single source” mean in this case, and how does it benefit the customer?
What it means is that as well as sending electrical signals to the brake control system, we also send pneumatic signals directly to the main air pipe controller – all from a single lever. So it’s a single source in that sense. But the entire chain of functions from lever to control system to the actual brake on the wheel – that is, every function in the braking system – also comes from a single source: Knorr-Bremse. And because of that, they’re all optimized to work together perfectly. This one-stop-shop approach means customers don’t have to depend on different suppliers.
Why is customization so important?
Just like the actual vehicles, driver’s consoles are individually designed. They can be very different, depending on the type of vehicle. Also, we often have to implement country or vehicle-specific specifications, or fit different types of handles such as ball knobs, conical handles, or T-bar handles. And depending on where they’re being used, lever operating forces may differ significantly. Levers in metro trains, for example, are constantly being actuated by the train driver, so they need to move smoothly and easily. In other applications, such as shunting locomotives, the levers must be designed so they’re extremely precise and sensitive to the slightest movement. Many customers want to fit extra functions like a lock with mechanical interlocks so people can’t misuse the lever, or directional switches with forward, reverse and neutral settings.
But all projects have one thing in common: From one vehicle to another, every time you install levers in a driver’s console, the conditions are different – and there’s never enough space. That’s why our modular toolkit is so important: It gives us maximum flexibility so we can made optimum use of the space available, even when we’re having to incorporate a lot of functions.
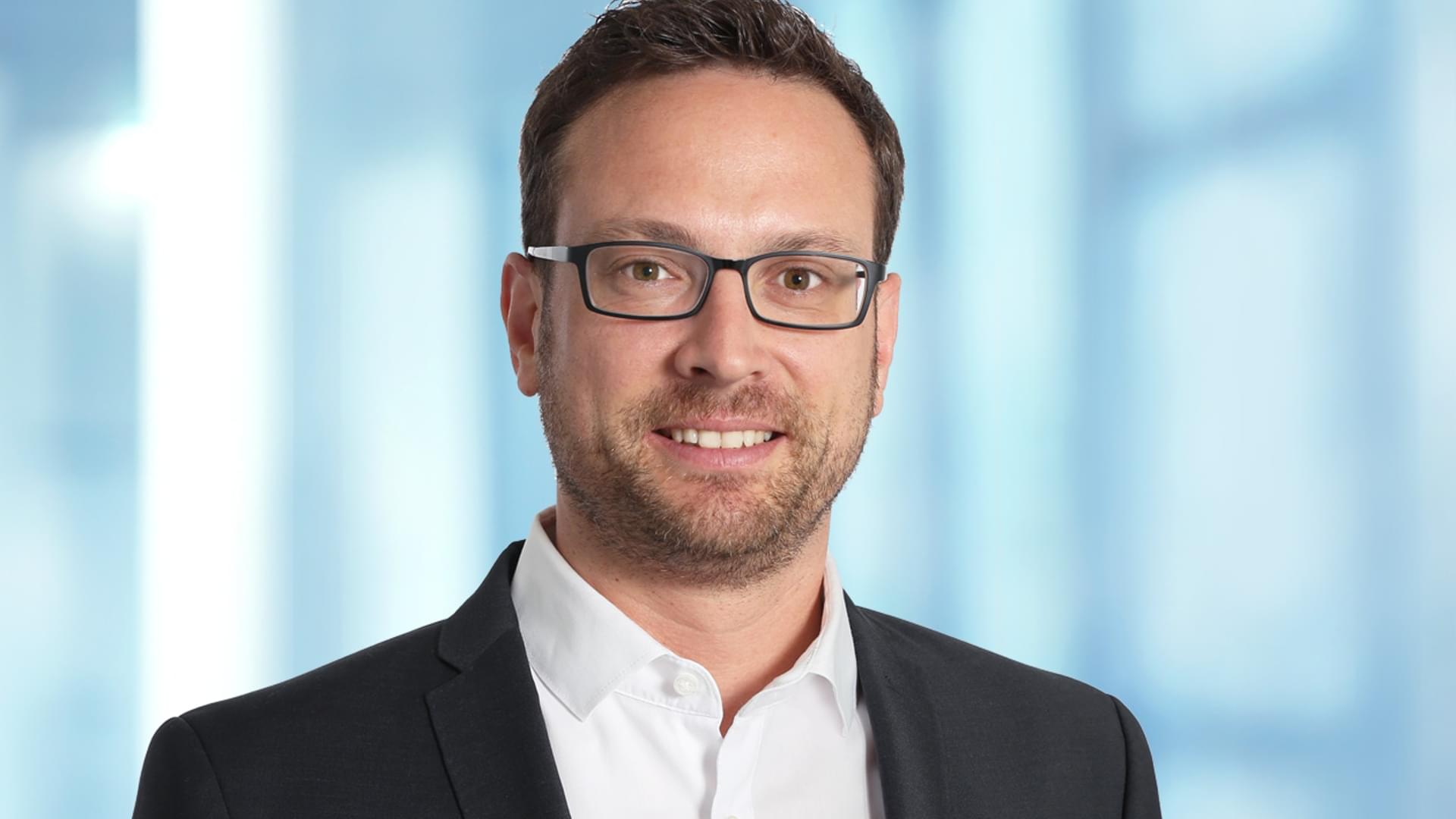
Thanks to our modular principle, we’re very quick – especially compared with our competitors. We can usually present a 90-percent solution after just two weeks.
Michael Holz – Teamlead Development Mechatronics / Electromechanics
How does this customization process work – and how long does it take from initial inquiry to delivery?
Again, thanks to our modular principle, we’re very quick – especially compared with our competitors. We can usually present a 90-percent solution after just two weeks. And by then, we’re also in a position to provide the customer with a preliminary installation model so they can run initial installation tests. Once the design has been frozen, it usually takes just a few weeks before we send parts lists and designs to production. Bottom line: From our production facility in Mödling near Vienna, we can deliver our systems anywhere in the world within a few months of the initial inquiry.
What makes the collaboration between the Mödling facility and Knorr-Bremse’s head office in Munich so special?
Engineering in Munich and production in Mödling work together as equals, sharing ideas and information with genuine team spirit. Weekly coordination sessions and regular in-person meetings make it easy to provide direct feedback on production experiences to the development team. If problems arise, both sides tackle them immediately, together. And thanks to the team members’ years of experience, clearly defined roles and competencies, and the very high levels of motivation across the whole organization, our customers always end up with flawless products.
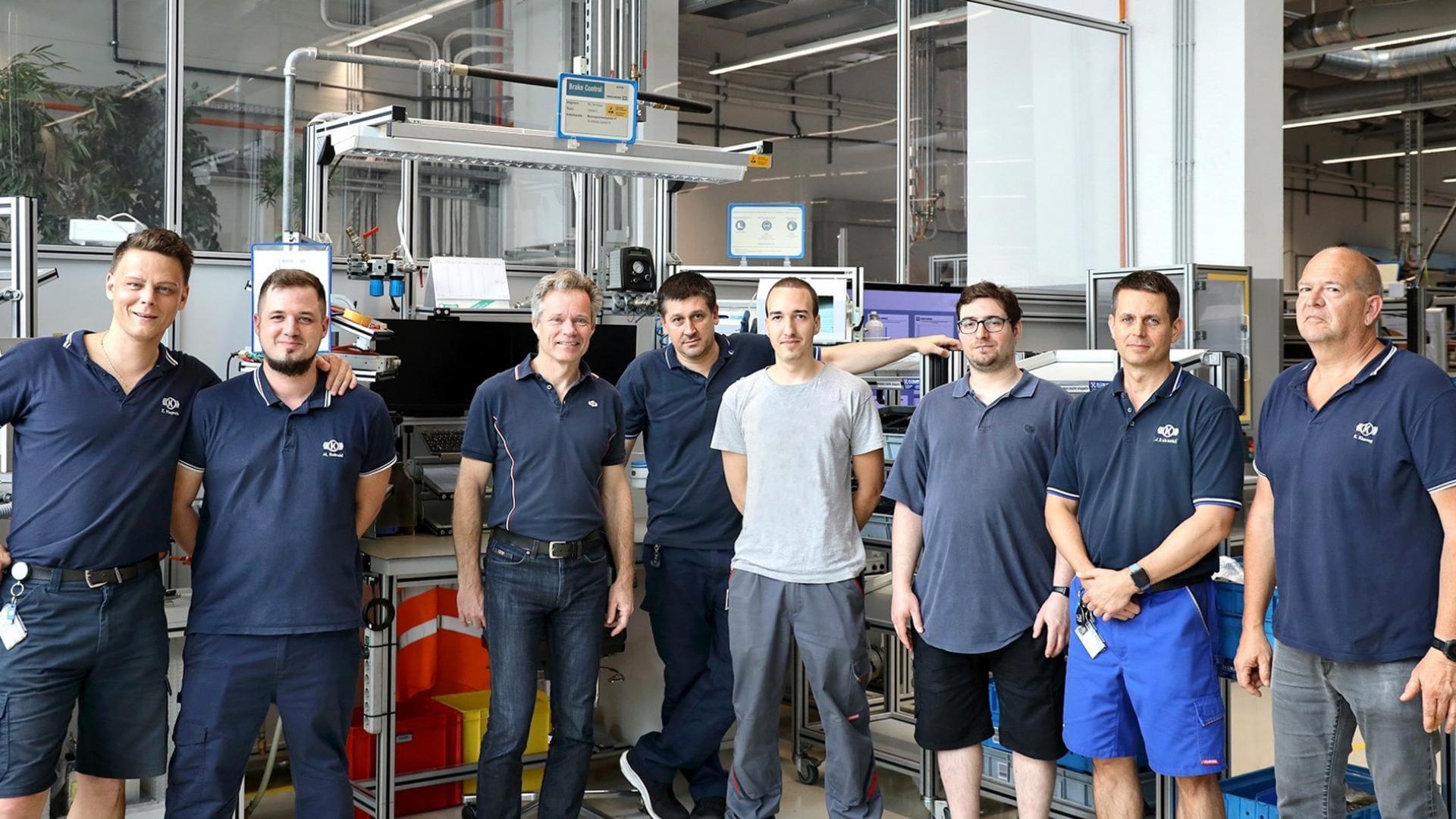
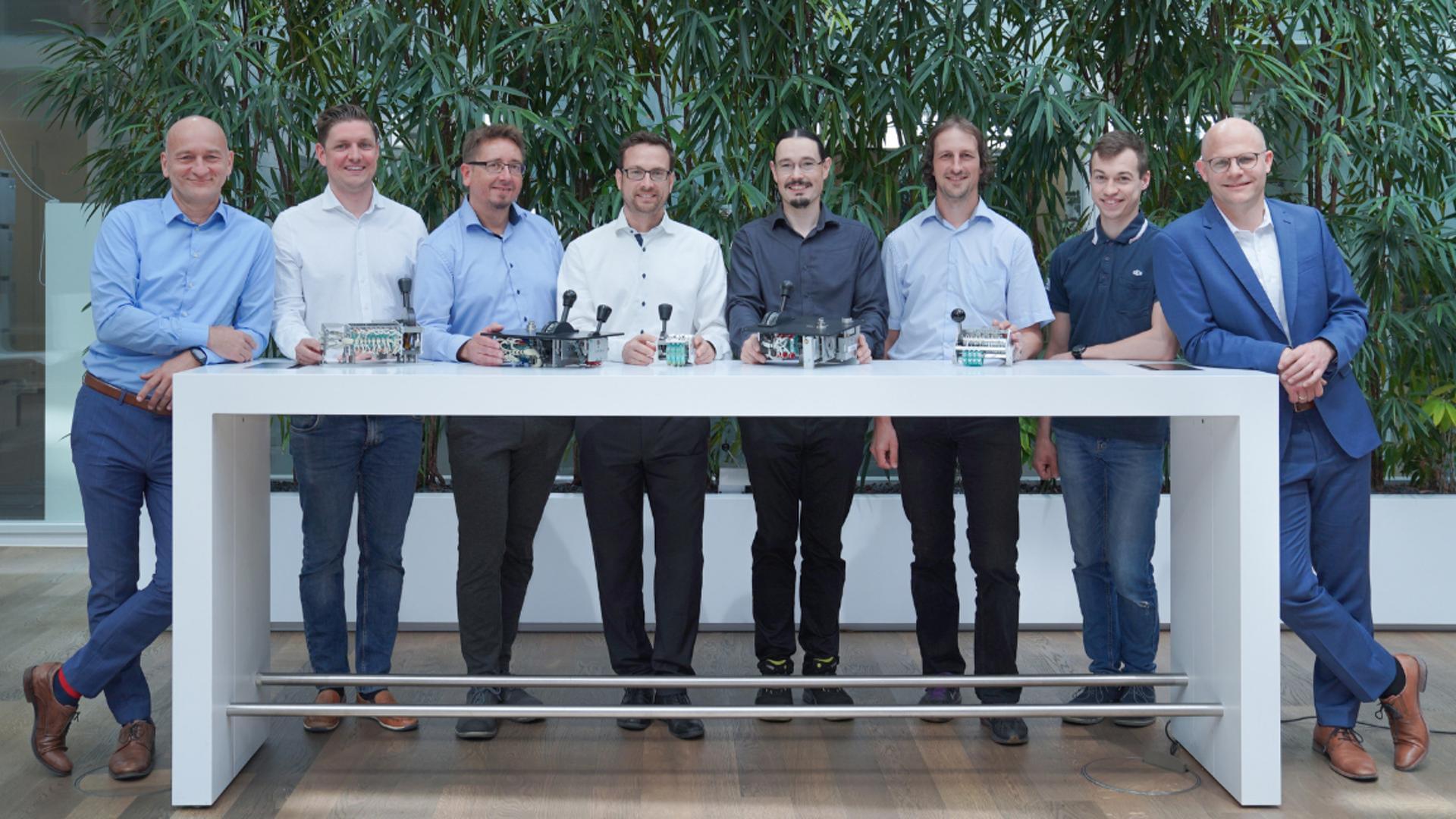
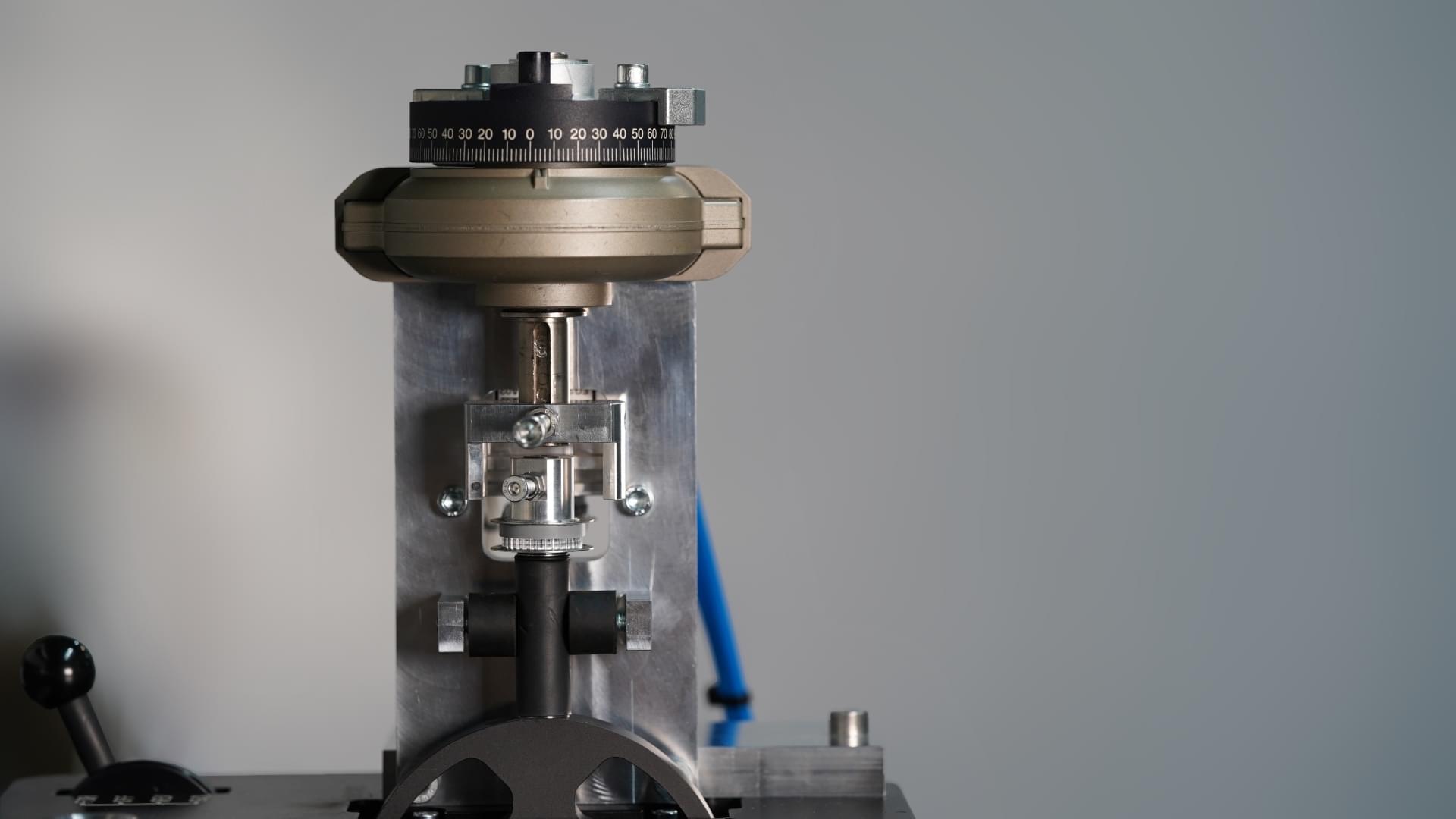
What tests do MotionLead Kits have to undergo before they’re dispatched?
Well, of course we test them extensively. In terms of objective results, our automated test rigs meet the very highest standards. To pass their operating life tests, the levers and their components must withstand up to three million actuations – significantly more than the stresses they’d be subjected to in real-world operation – and still work perfectly even after surviving the test.
But let’s be clear: Our employees are well aware of how important they are in assuring the quality of our products and systems. Everybody working in development and production knows what a vital role control and brake levers play in vehicle operation. They must work perfectly in all conditions and circumstances – anything else would immediately cause the vehicle to fail. Our excellent team spirit helps us to overcome the constant challenges, devise the best possible solutions for each customer’s individual needs, and constantly optimize our production processes and workflows.