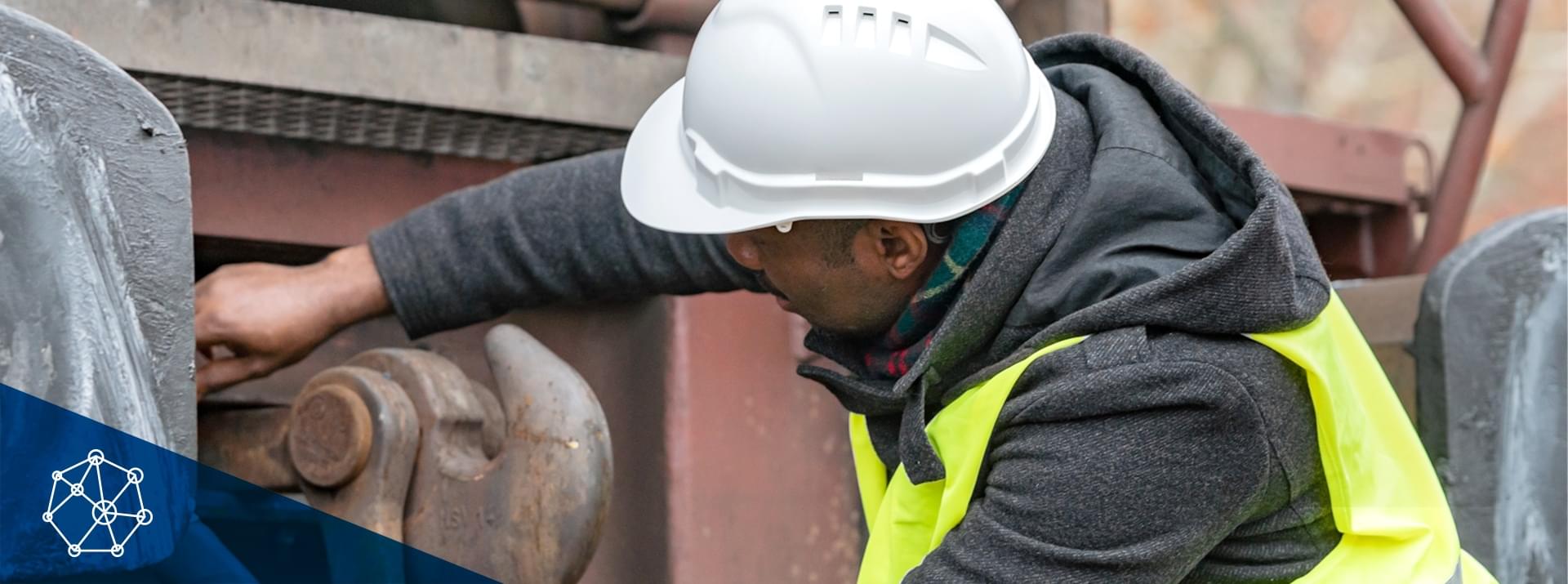
By 2030, the European Union aimes for increasing the proportion of freight transport by rail from just 18 percent today to at least 30 percent in the future. Digitalization and automation of freight wagons is regarded as the single most significant step toward achieving this goal. But to take full advantage of the opportunity represented by the Digital Freight Train and its main enabler, the Digital Automatic Coupler (DAC), to boost rail freight capacity, efficiency and availability, the entire industry shall be involved. Most important of all, the rail industry needs to swiftly establish European standards for coupling and reference test-based qualification.
Rising greenhouse gas (GHG) emissions, global warming, and the accompanying upsurge of environmental disasters such as heatwaves, storms and heavy rain, are threatening the ability of human beings to survive in acceptable living conditions. These climate-related circumstances need no further explanation. The same applies to the German transportation sector’s role – and acknowledged responsibility – as the country’s largest energy consumer and third largest GHG emitter [1]. This is why the climate action plans of both the German federal government and the European Union (EU) quite rightly pay particular attention to the industry. Both plans envisage a large-scale shift from road to rail. The EU’s explicit goal, for example, is to increase the proportion of freight transported by rail from its current level of around 18 percent to at least 30 percent by 2030. This focus on rail makes good sense. In terms of tonne-kilometers, a truck emits about six and a half times more GHGs than a freight train – approximately 111 grams, as opposed to just 17 grams [2].
Even so, today’s rail freight is not yet a competitive alternative to long-distance transportation by road. In particular single wagon transport no longer meets twenty-first century requirements for flexible supply chains. As things stand, marshalling yard operators must forsee plenty of time to shunt and assemble freight trains. First, the marshalling yard personnel couples manually the individual wagons together. Then they fasten each screw coupling’s drawbar to the respective draw hook. Finally, they connect the pneumatic brake hoses. Once the train has been coupled together, the brake inspector walk up and down it several times, personally checking every single brake to ensure that it works correctly. Meanwhile, the marshaling team is carrying out other manual work – checking the loading doors, for example, or mounting end-of-train devices if required.
The many non-automated operations involved in preparing, assembling and operating freight trains are a major reason why rail freight is too slow, too expensive, too labor-intensive and too inflexible to be competitive. The solution, as it has already become clear, is to automate processes across trains and fleets.
80809 München
Deutschland - Germany
carina.smid@knorr-bremse.com
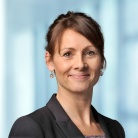
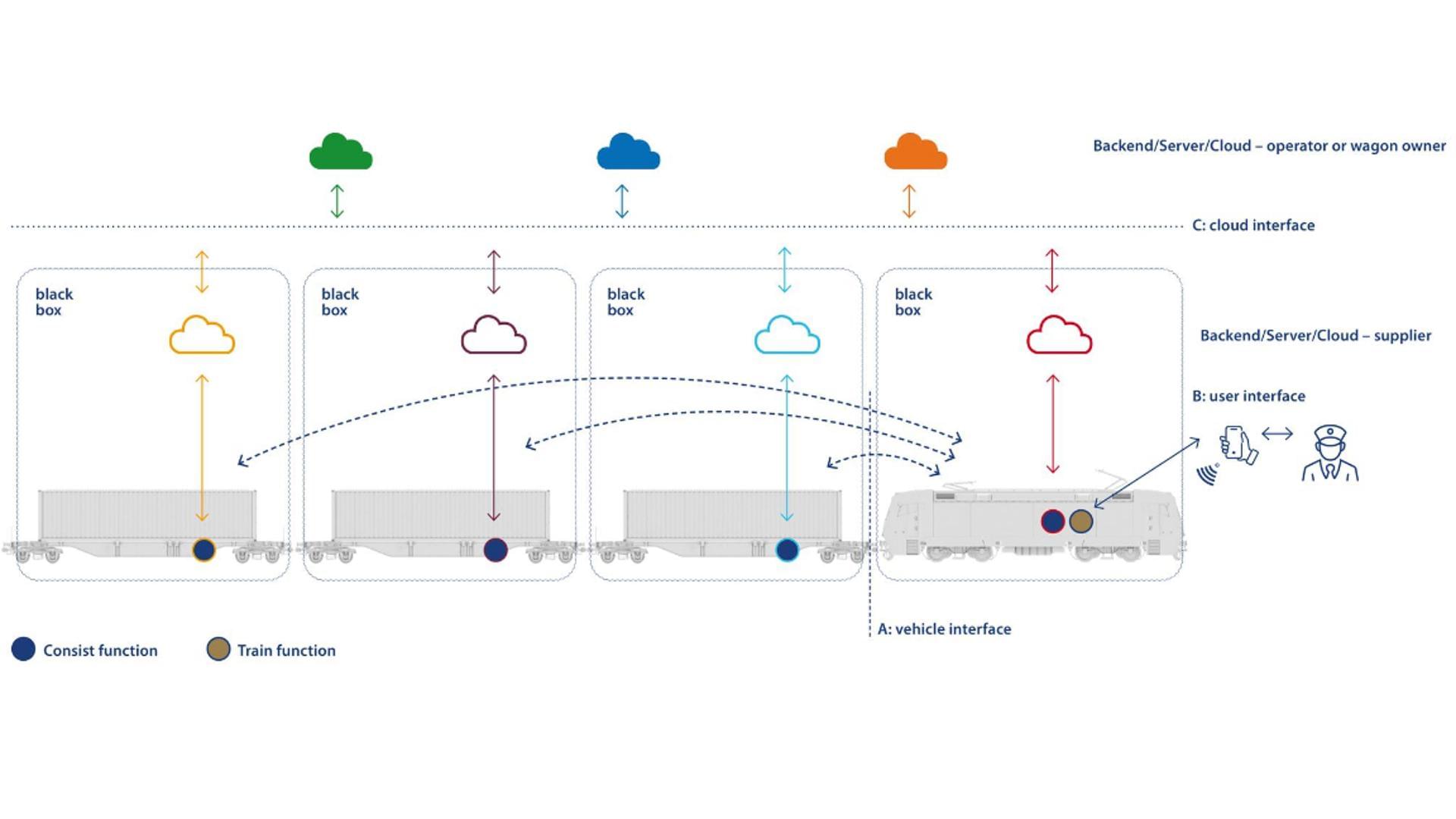
The Digital Automatic Coupler (DAC) is the key enabler of large-scale rail freight automation and digitalization
In terms of functionality, equipping freight wagons and locomotives with Digital Automatic Couplers (DACs) and all the related electronic control systems, sensors and actuators represents the next major step forward. First, because the DAC simplifies the enormously time-consuming train assembly process by automating the mechanical and pneumatical coupling work. And second, because the DAC simultaneously connects the locomotive’s power supply to the rest of the train – and establishes a communications network along the entire length of the train.
At present, two different approaches are under consideration:
- DAC4: automatic coupling with manual uncoupling
- DAC5: automatic coupling with remote-controlled uncoupling
Operators seeking to take full advantage of the new coupling system’s operational benefits – especially for single wagon load – will need a DAC Level 5. DAC5 hugely accelerates the process of assembling and shunting freight trains, in turn boosting overall freight transportation capacity. Operators benefit from streamlined process scheduling and – a not-insignificant point – from improved health and safety conditions for their marshalling yard personnel.
The "DAC5" level in particular shall provide solutions with the highest functional safety requirements against unintented uncoupling or movement. Irrespective of this, further requirements for the automation systems to be newly integrated shall be defined, above all with regard to energy management, train communication as well as communication from and to the cloud, including over the air services. This necessarily also requires adequate measures to defend against cyber attacks.
Automation of train operations by upgrading freight wagons with electronics
More specifically, developers are currently focusing on the following functions:
- Automated brake test: This should hugely improve the efficiency of train preparation and assembly by rendering labor-intensive, on-foot inspection of the entire train by technical and brake test personnel obsolete. Designed as an end-to-end monitoring system, the brake test system captures all relevant brake conditions and displays them on mobile devices in real time via an user-friendly interface.
- Remote-controlled uncoupling (DAC5): As the name suggests, a remote-controlled uncoupling system should also make it possible to uncouple wagons or wagon groups of the train. For this to happen, additional actuators are required on couplers that already comply with DAC4.
- Parking brake management: Parking brakes lock axles of freight wagons to prevent them from unintended movement. On freight wagons that are already equipped with an onboard electronic system, the system could also be used to control the (additional) actuators needed to manage the parking brake.
- Automated train inauguration and integrity monitoring: In case of a fully equipped Digital Freight Train, all train functions would ultimately depend on an automated train inauguration and integrity monitoring. There would be no further need to use additional end-of-train devices.
Given that the operational benefits justify the additional expense, the DFT could also pave the way for the introduction of an electropneumatic freight train brake. After all, the basic onboard prerequisites would already be in place, in the form of a suitable electronic infrastructure. In addition to its original functions, this automation framework could positively impact the Digital Freight Train’s profitability in other ways – by serving, for instance, as a platform for flexible, condition-based maintenance (CBM).
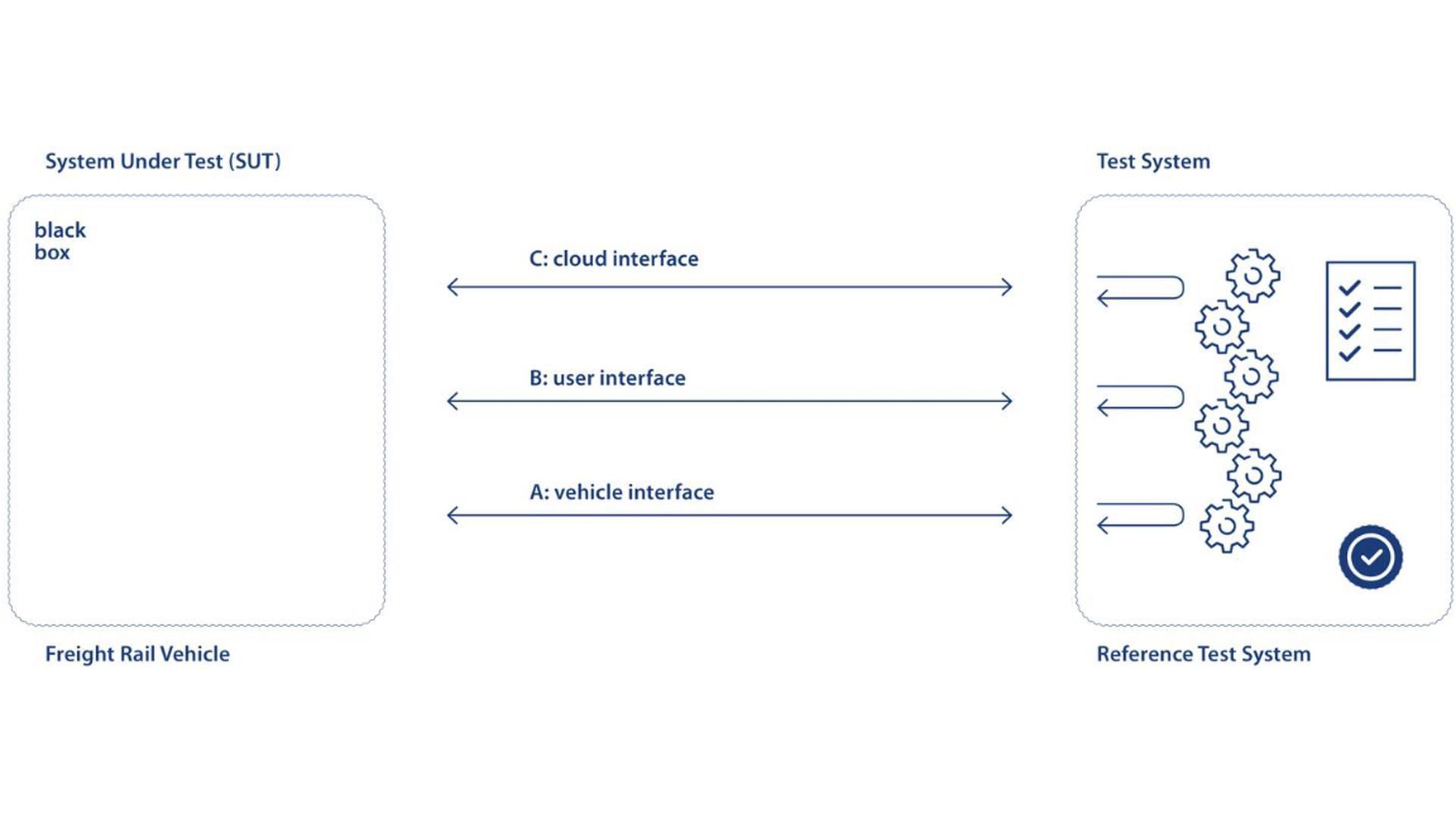
Consistent standards for vehicle interfaces and train functions across the entire European rail freight market
While the value added by a Digital Freight Train is undoubtedly attractive, developing the necessary technology is a highly complex process – especially in view of the underlying requirement for freight rail vehicle interoperability in Europe. Just as UIC regulations and EN standards for pneumatic brake systems make it possible to, for example, operate distributor valves produced by different manufacturers in a train, so a similar set of rules and standards is required for DFTs before they can go into operation. And once standards have been defined for network communications and application profiles, as well as the onboard power supply, it should become technically feasible to standardize the specifications for freight vehicles’ electromecanical couplers.
While agreeing on hardware standards seems to be complicated, however, the true complexity of the standardization required only becomes apparent at the level of software-driven functions. This is because long-term interface compatibility – while essential – must not be allowed to hamper the ongoing technical development of the system as a whole. To achieve such flexibility, it is vital to clearly separate technical vehicle functions from the operational responsibilities of the personnel in charge – and, once again, to establish appropriate standards for doing so. That this should go hand in hand with, as far as possible, end-to-end standardization of operating processes throughout Europe is both obvious and – in view of the hundreds of rail transportation companies involved – extraordinarily challenging.
Another cluster of issues surrounds safety and availability considerations at the functional train level. While the safety and availability targets to be aligned between vehicle manufacturers, rail operators and equipment suppliers under the new Europe’s Rail Joint Undertaking (ERJU) initiative should be as generic as possible, the actual safety cases used for authorization must be valid for the individual vehicles – in this case, for the individual freight wagons and locomotives.
A quick glance back into the recent past makes it clear just how much time pressure the industry is now under. Although one might think that standardizing mechanical DAC interfaces would be relatively straightforward, industry players have already spent several years negotiating this aspect alone.
Certification and reference testing
Yet another, related consideration concerns the issue of how to manage the entire life cycle of DFT vehicles in the best way. A key point here is how best to integrate a modern maintenance approach according to which any workshop in Europe should, in principle, be capable of servicing or repairing any freight wagons . This is a requirement for which suitable answers – such as mobile maintenance – still need to be found.
It is also important to ensure that new or refurbished vehicles continue to fit seamlessly into interoperable rail freight traffic across Europe – even over the long term. With this in mind, the industry is already considering whether to introduce a reference test procedure, whereby vehicles equipped with automation technology should be subjected to a comprehensive functional test of all three interfaces using a reference test system. As part of the safety case, the reference test procedure could subject the train functions of all new or modernized freight wagons and locomotives to comprehensive, manufacturer-independent validation. To make this possible, the required interface specifications shall also include adequate acceptance criteria for all train functions.
Even after its market launch, the Digital Freight Train will still require substantial further development. Similarly, the reference test system would also require ongoing extentions – in particular, to make it ever more backward-compatible, so that further changes could be regularly introduced throughout the life cycle of DFT vehicles and vehicle generations.
Summary:
Today’s rail freight traffic is no longer competitive with road transportation. With its Digital Automatic Coupler (DAC) and high-performance automation systems, the Digital Freight Train (DFT) is expected to lead a shift back to rail – by adding functions that are totally new to rail freight such as automated brake tests, park brake management and remote-controlled uncoupling, as well as train inauguration and train integrity monitoring. The requisite technologies are still under development. But the plan stands and falls according to how swiftly consistent, European definitions and standards can be established for the DFT rollout. The European Union’s ERJU program provides a perfect framework for making all this possible – we should all get behind it right now!
Authors: Dr. Thomas Anton, Steffen Jass
References:
[1] Energy consumption by energy source and sector. German Federal Environment Agency (in German): https://www.umweltbundesamt.de/daten/energie/energieverbrauch-nach-energietraegern-sektoren#entwicklung-des-endenergieverbrauchs-nach-sektoren-und-energietragern
[2] Levels of greenhouse-gas emissions in German freight traffic by mode of transportation in 2019. Statista (in German): https://de.statista.com/statistik/daten/studie/881600/umfrage/co2-emissionen-im-deutschen-gueterverkehr-nach-verkehrsmitteln/