Feasibility study demonstrates potential of industrial 3D printing in the rail industry.
Industrial 3D printing opens up some particularly interesting new opportunities in the rail vehicle sector. A feasibility study is being carried out to determine the suitability of this manufacturing technique for producing sanding system control panels. Despite the promising results, the fact that the 3D printing process has yet to be certified constitutes a barrier to its widespread deployment in production.
Contact
80809 München
Deutschland - Germany
carina.smid@knorr-bremse.com
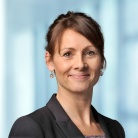
Advances in industrial 3D printing open up new opportunities
The fundamental requirements for new rail vehicle subsystems are well established. Vehicle manufacturers want maximum vehicle integration flexibility, shorter times to market, and the lowest possible cost and weight. Reconciling all of these demands can be a bit like trying to square the circle, but advances in industrial 3D printing are making it a much more realistic prospect.
As a result, Knorr-Bremse Rail Vehicle Systems is currently carrying out a feasibility study to determine whether and, if so, how this technology might be used in the production of sanding system control panels. As well as evaluating the potential of this manufacturing technique, the study also aims to analyze possible barriers to its industrial application in the context of braking systems.
Design and functioning of sanding system control panels
Sanding system control modules combine pneumatic and electro-pneumatic components on a carrier system that usually comprises an aluminum panel. The components are connected to each other via a series of air ducts and holes drilled in the panel. The module is supplied with compressed air via the compressed air connection. The pressure-reducing valve brings the air pressure down to the required operating pressure. Two solenoid valves control the supply of compressed air to the sanding unit, while an inspection nozzle serves as a measuring point.
Summary
As part of a 3D printing feasibility study, Knorr-Bremse built an innovative, significantly lighter and more compact control panel function carrier for sanding systems. The measured values in the function test sequences carried out with the new part were almost identical to those of conventionally produced panels. The panels are an attractive solution for application scenarios where installation space is tight, such as in low-floor vehicles and future high-speed applications.
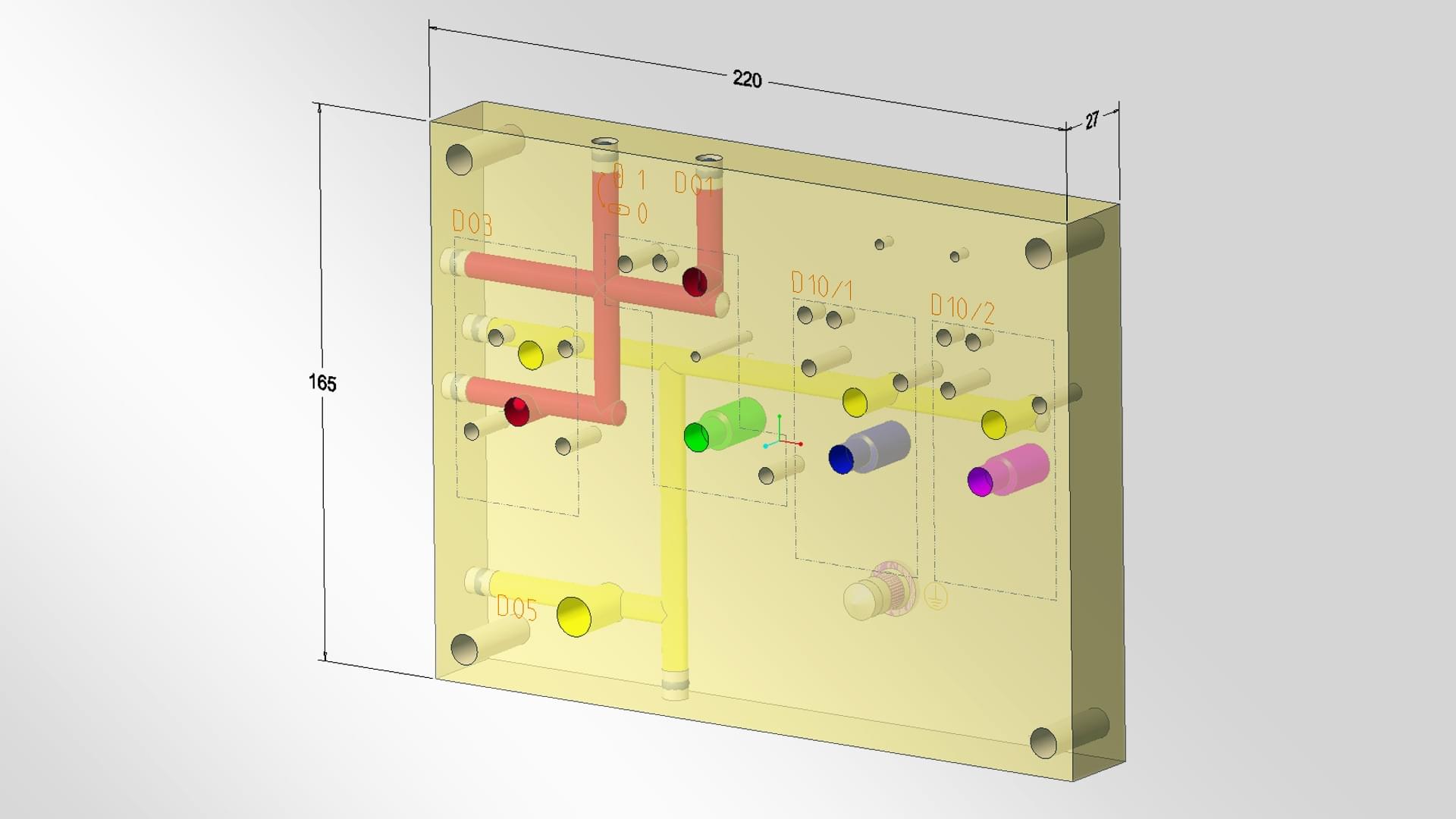
In a typical use case, the structure has a volume of just under 5,700 cm3, while the aluminum panel weighs 2.53 kg. The panel’s bulky design is mostly determined by the limits of the machining processes (milling and drilling) and by the fact that the components are arranged in just a single layer.
Industrial 3D printing enables new design approach
Industrial 3D printing enables design-driven manufacturing, where form follows function rather than vice versa. The greater design flexibility offered by this technique makes it possible to realize highly complex structures and intricate details that would previously have been almost impossible to produce. It was therefore surmised that it should be possible to design a significantly lighter and more compact control panel function carrier using 3D printing.
Instead of mounting the modules on a solid control panel, the goal was to arrange them within a compact frame furnished with the appropriate interfaces for the different components. It took several versions of the design to determine how best to position the components in order to make the frame as compact as possible. The process also involved making some adjustments and improvements to the connection distributor.
One notable feature of the 3D-printed version is that the ducts do not necessarily have to be cylindrical. The shape of the ducts can vary within certain parameters while maintaining the same cross-sectional area. In this specific instance, this meant that ducts could be “laid” next to each other rather than at different component levels as was previously the case. In order to enable the machining of elements such as threaded connections, the feasibility study design included a support frame (also 3D-printed) and additional fixing points.
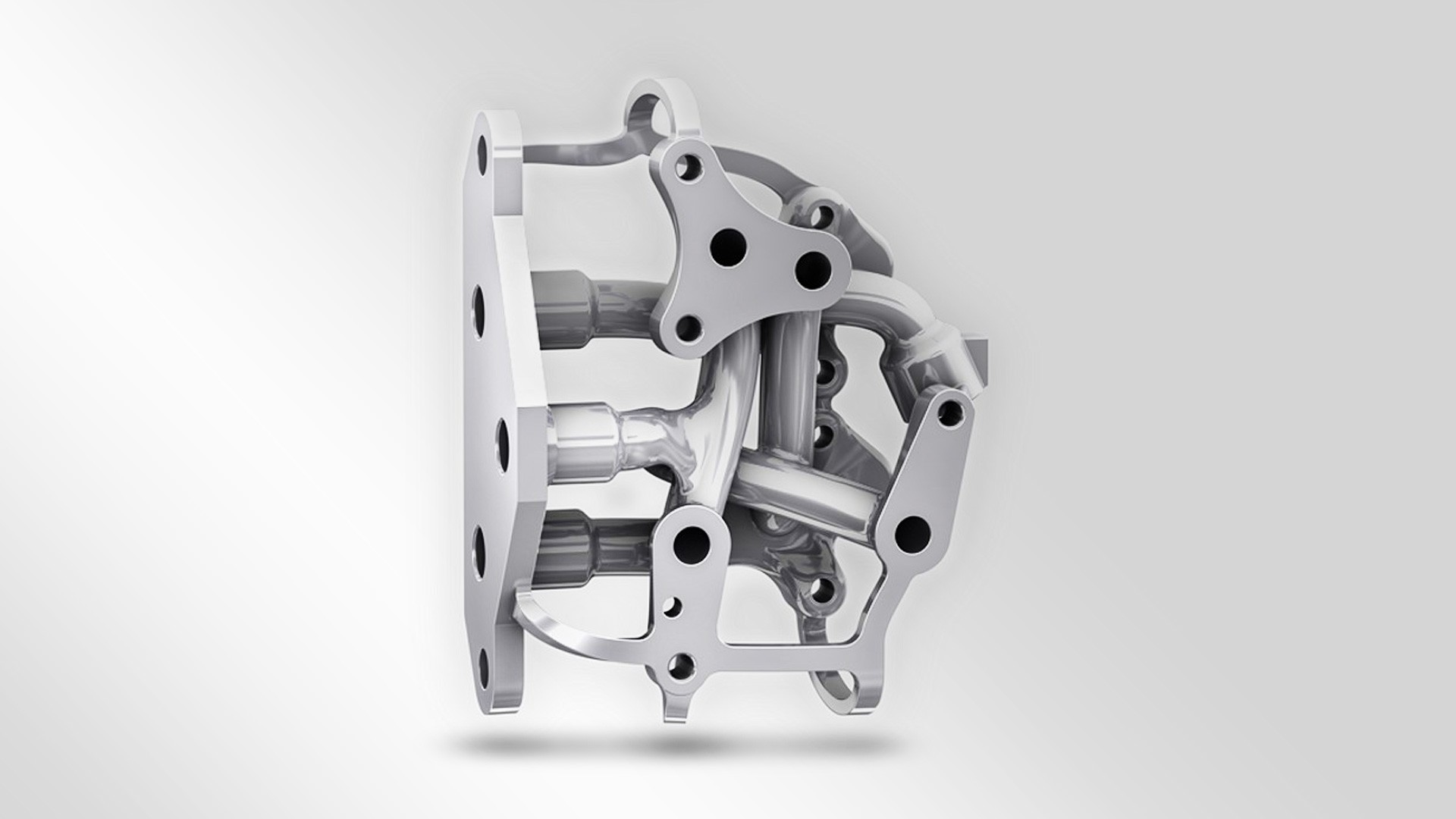
Technical specifications of the 3D-printed control panels
The experimental carrier had to meet most of the specifications of conventional brake panels. The pneumatics functionality had to match the performance of the conventional control panels, while the unit had to comply with the structural requirements of EN 12663 (Category L) and the mechanical requirements of EN 61373 (Category 1, Class B). It also had to successfully complete a 720-hour salt spray test as specified by DIN EN ISO 9227. The lowest natural frequency of all the components had to be at least 30 Hz, and the ducts had to remain free of water pockets at all times. The engineers validated the design before the unit was built, employing the finite element method to analyze static and dynamic component behavior.
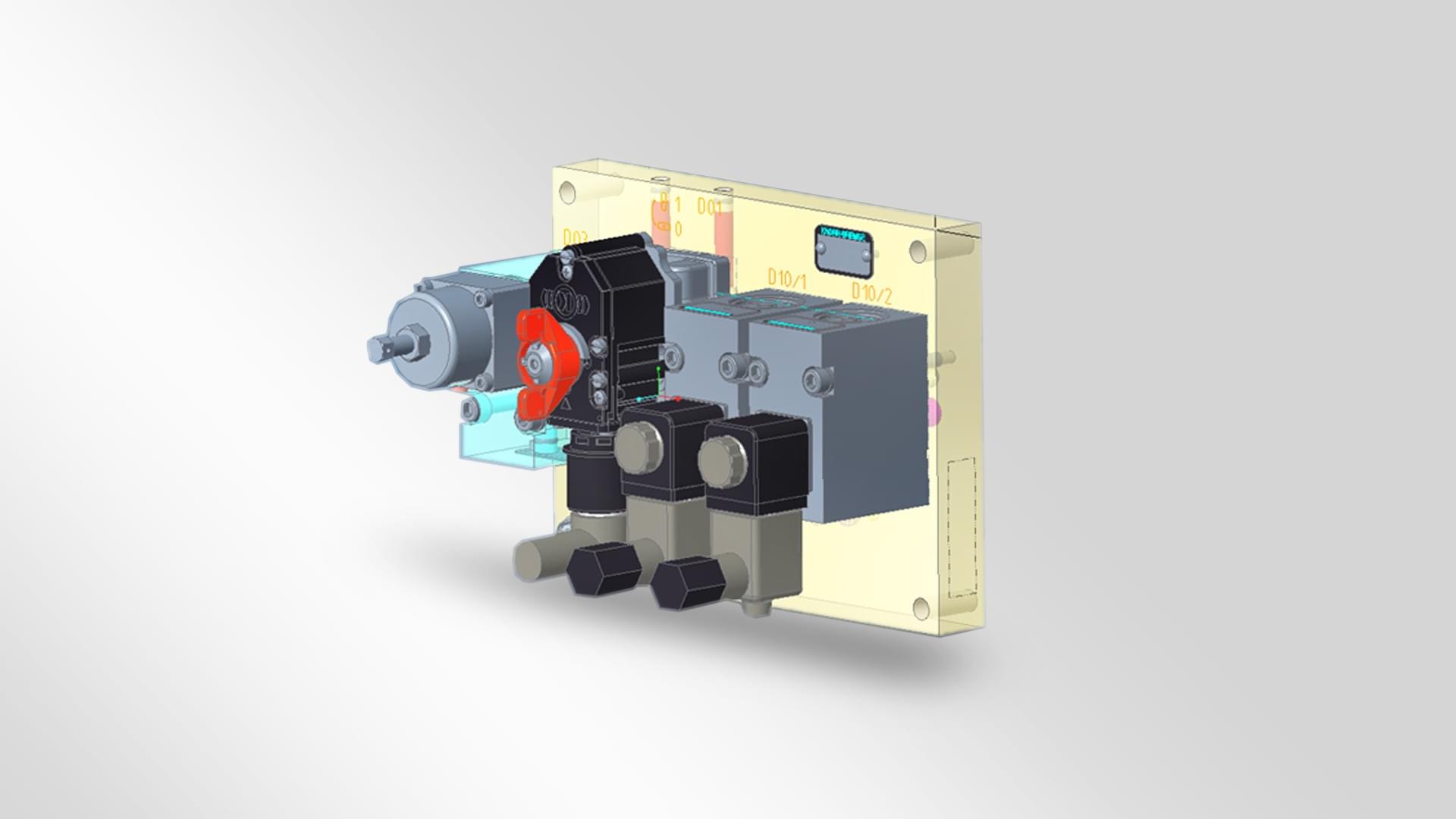
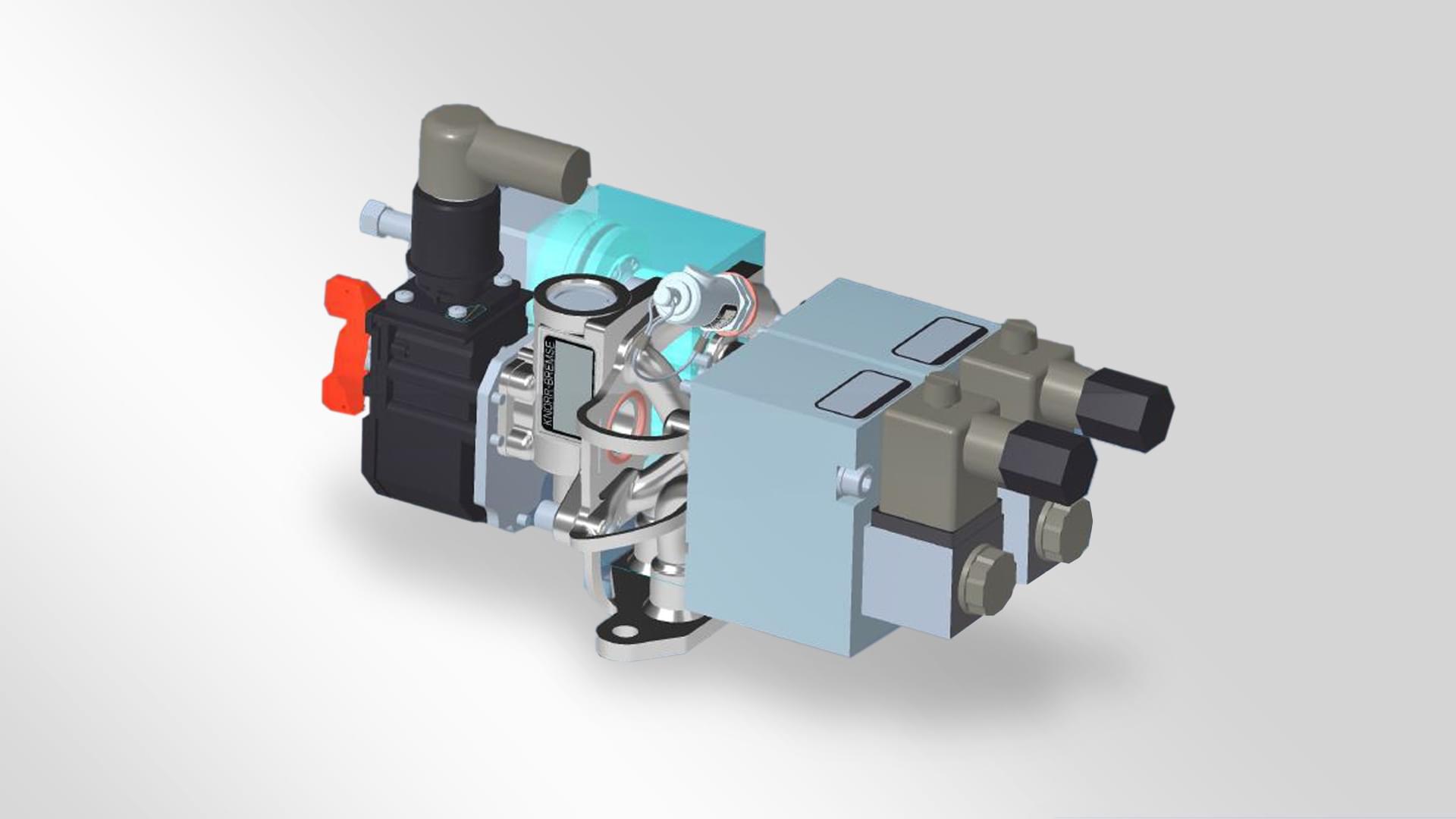
Direct Metal Laser Sintering (DMLS)
The method chosen to produce the unit was Direct Metal Laser Sintering (DMLS) using an aluminum alloy feedstock. A high-power laser fuses layers of the powdered feedstock together at the precise points specified by the computer-generated component design data. The structure “grows” from the bottom up, as successive 60-micron layers are deposited one on top of the other.
It took 12 hours to print the structure in the feasibility study, while a further three hours was found to be a realistic timeframe for completing the necessary pre- and post-processing operations. Post-processing includes the removal of the support structure, which is printed
concurrently in thinner layers. The support structure prevents the printed structure from buckling under its own increasing weight during the printing process.
Load and function testing
After the part had been built, it underwent the obligatory load and function testing. Once it had been connected to the appropriate testing infrastructure, the pressure was gradually increased and the pressure drop measured. An airtightness test was then carried out in a water tank. At 13 bars, the pressure was approximately one third higher than the maximum operating pressure of 10 bars. All of the measurements were within the tolerances specified for conventional control panels. The frame also easily withstood the shock and vibration tests specified by IEC 61373:1999-01 (Category 1, Class B), thereby permitting the conclusions of the FE analysis to be considered validated.
After being installed on standard, volume-produced equipment, the panel underwent all the function test sequences used for pre-delivery testing of conventionally produced panels. Even for the first version of the structure, the measured values in the feasibility study were almost identical to those of conventional panels. This exceeded expectations.
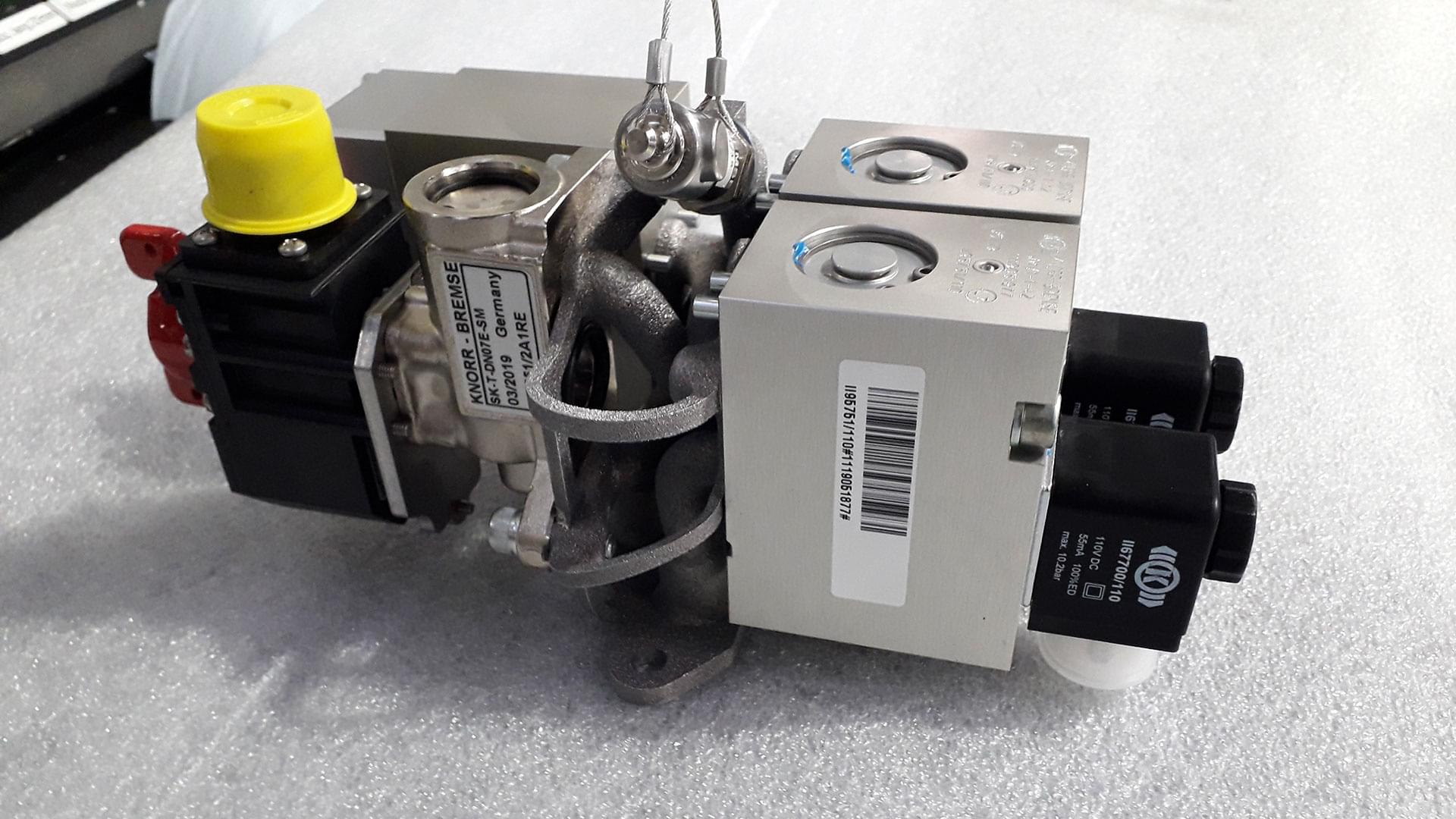
Widespread deployment of 3D printing requires process certification
The results of the upfront simulation and the component and function tests clearly demonstrate that the process is suitable in principle for producing the control panels. Several further test series would of course be necessary before fully commencing volume production, for example to optimize the printing process.
As well as greater component design flexibility, 3D-printed control panels offer a number of other benefits. They are up to 90% lighter than the conventional aluminum panels, and the frame allows the components to be arranged in a far more compact layout. The panels thus present an attractive solution for application scenarios where installation space is tight, such as in low-floor vehicles and future high-speed applications.
However, the fact that the 3D printing process has yet to be certified in the rail industry constitutes a barrier to the technology’s widespread deployment in (volume) production. Regulations must be developed to establish a standardized procedure for certifying additively manufactured components. Moreover, some aspects of the printing process are not yet mature enough for industrial (volume) production. This means that, for the time being, the component properties have to be extensively validated for each specific use case. However, several initiatives have already been launched to develop a certification system for the rail industry and to refine the relevant additive manufacturing technologies.
Authors: Dr. Thomas Anton, Bernhard Winkler, Attila Kovács, Attila Metál