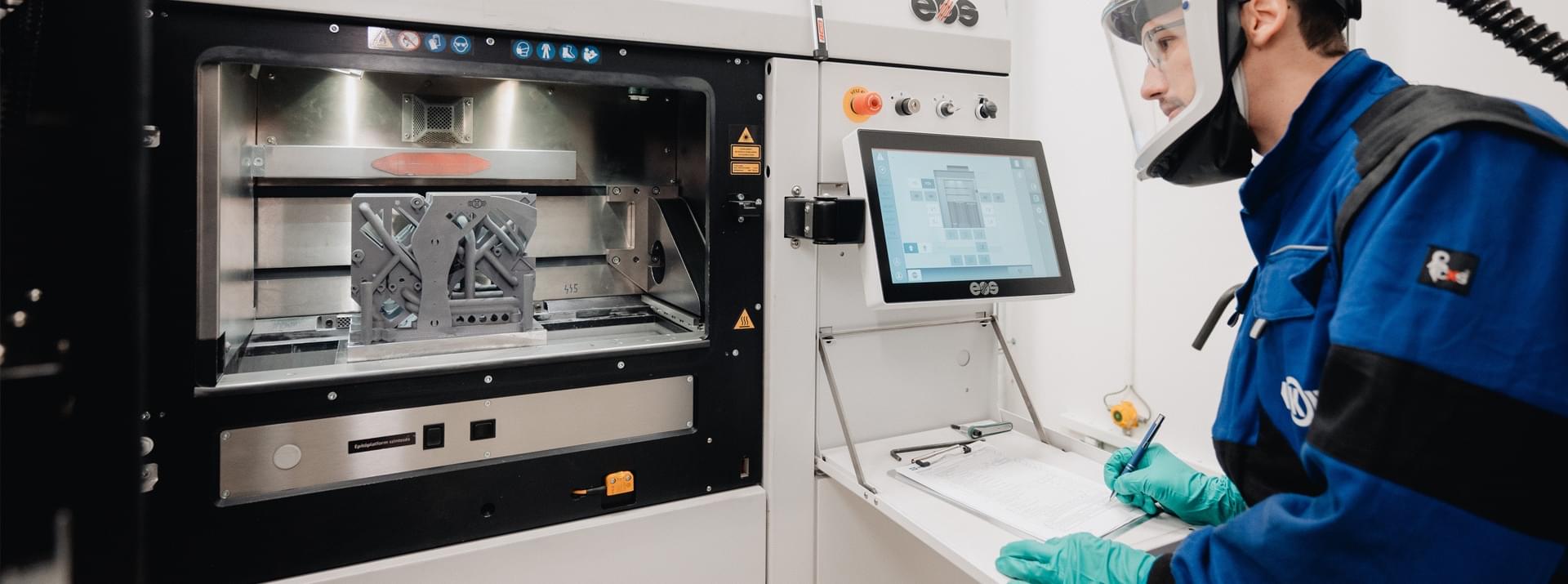
Gemeinsam treiben sie den industriellen 3D-Druck in der Schienenfahrzeugbranche voran: Als Bereichsleiter Production Rail verantwortet Bernhard Winkler von München aus unter anderem das Knorr-Bremse Digital Manufacturing. Bei Attila Kovács, Director Mechanical Design Engineering, laufen am Standort in Budapest die Fäden der ersten additiven Komponentenentwicklungen zusammen.
Herr Winkler, als wir vor etwa vier Jahren über die Potenziale der Additiven Fertigung in der Bahnindustrie sprachen, kamen Sie mit einem 3D-gedruckten Ersatzteil zum Termin …
Winkler: … stimmt, darauf waren wir damals mächtig stolz: unsere erste additiv gefertigte Komponente, die tatsächlich auch in einem Schienenfahrzeug verbaut wurde.
Erzählen Sie!
Winkler: Für ein recht dienstaltes Fahrzeug, das eigentlich noch gut in Schuss war, fehlte einem großen europäischen Betreiber ein sehr spezielles Ersatzteil. Die bisherige Komponente wurde bereits abgekündigt. Selbst für die Rohteile waren keine Werkzeuge und Vorrichtungen mehr verfügbar. Also haben wir dem mittlerweile 40 Jahre alten Fahrzeug per 3D-Druck noch ein paar Lebensjahre auf den Schienen geschenkt. Eine klassische Nischenanwendung, keine Frage. Aber was die Aufgabenstellung angeht, da waren wir sehr erfolgreich.
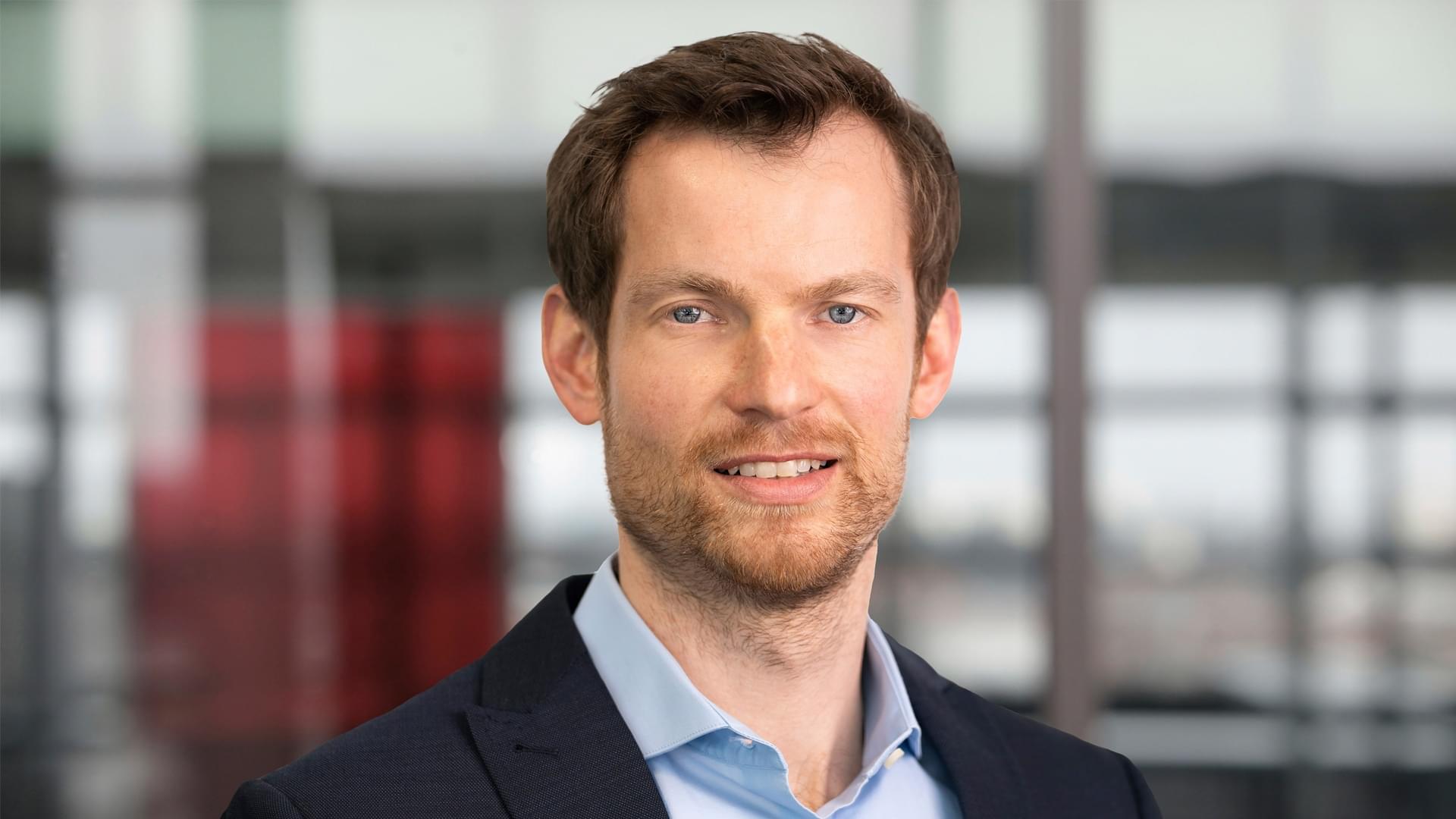
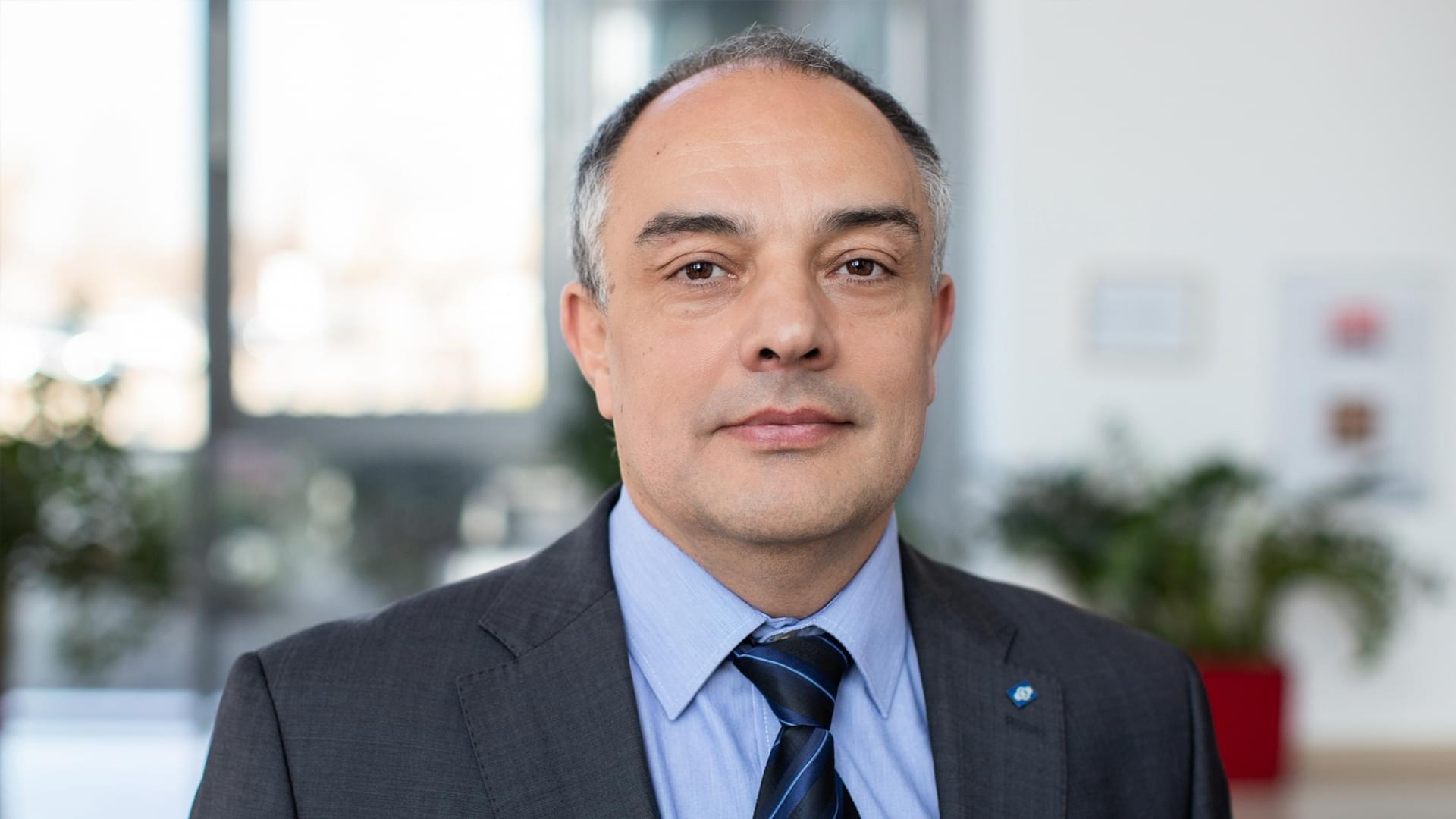
So einfach geht das?
Kovács: Leider nicht. Schon der Weg zu den Prototypen ist sehr komplex und voller offener Fragen: Wie muss das Design für die geforderte Funktionalität aussehen? Welches Druckverfahren eignet sich am besten für die konkrete Anwendung? Wie sieht es mit der Werkstoffzusammensetzung aus? Schließlich ist noch die Überwachung des Druckprozesses mit seinen zahlreichen Parametern wie Temperatur, Druckgeschwindigkeit und Schichtdicke entscheidend, um konsistente und zuverlässige Komponenten herzustellen. Und am Ende erfordert die Validierung von mechanischen Eigenschaften, Haltbarkeit und Leistungsfähigkeit spezielle Prüfverfahren. Bis das Ersatzteil endlich verbaut werden konnte, haben wir einen enormen multidisziplinären Lernprozess durchlaufen. Mittlerweile beherrschen wir die Technik und die Prozesse dahinter sehr gut.
Aber allein aus der Herstellung von Ersatzteilen wird noch kein Business Case, oder?
Winkler: Das würde ich so pauschal nicht unterschreiben: Gerade spezielle Komponenten mit kleineren Stückzahlen lassen sich im Vergleich zur konventionellen Herstellung erst additiv wirtschaftlich fertigen. Ich bin mir sicher, die Additive Fertigung wird bestehende Verfahren nicht ersetzen. Sie kann jedoch Lücken bei Designszenarien schließen, bei denen klassische Guss- oder Fräsverfahren an ihre Grenzen kommen.
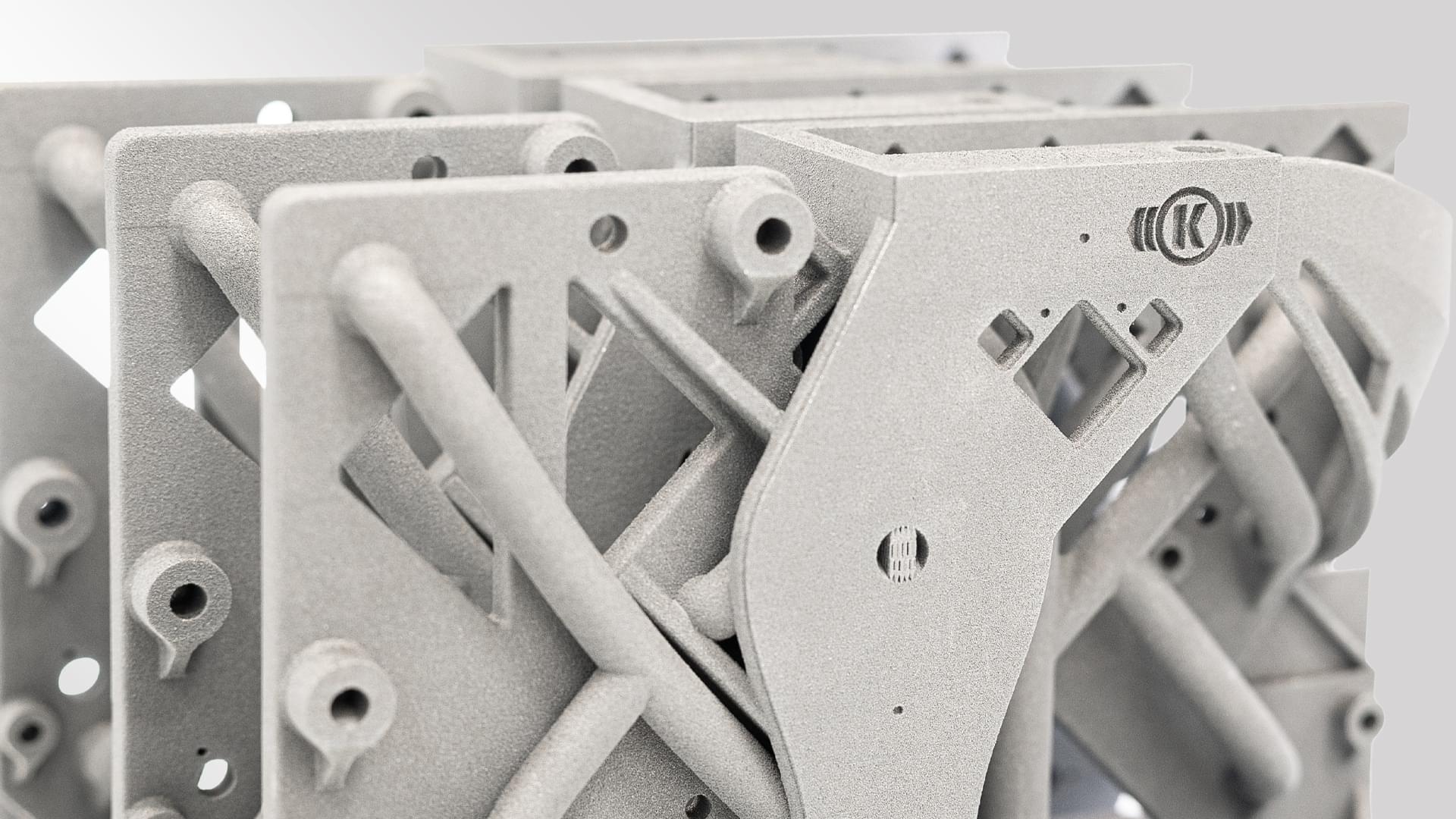
Zum Beispiel?
Winkler: Etwa bei komplex gestalteten Bauteilen, die womöglich auch mit Hilfe der Bionik optimiert wurden. Manchmal sind es vermeintliche Kleinigkeiten, an denen eine konventionelle Fertigung scheitert: ein Luftkanal zum Beispiel, der für die konkrete Anwendung eine bestimmte Form benötigt, die sich aber nicht mehr bohren lässt. In solchen Situationen schlägt die Stunde des 3D-Drucks.
Kovács: Wir müssen ehrlich sein: Eine komplette Bremsscheibe werden wir wohl allein schon wegen der extremen Belastung auf absehbare Zeit nicht additiv fertigen. Aber wir drehen mit dem Verfahren die klassische Herstelllogik um. Anstatt aus einem Metallblock das gewünschte Teil zu fräsen, fügen wir per Laser ein spezielles Metallpulver Schicht für Schicht zur gewünschten Form zusammen. „Design for Function“ lautet das Stichwort. Unsere Entwicklerteams erhalten dadurch eine deutlich höhere Designfreiheit bei der Auslegung neuer Schienenfahrzeugkomponenten oder der Optimierung bestehender Bauteile. Gerade die Bahnindustrie verlangt zunehmend nach komplexen und robusten Bauteilen, die gleichzeitig klein und leicht sind.
Kovács: Abhängig vom konkreten Bauteil ist mit der additiven Fertigung eine Gewichtsreduktion um 80 bis 90 Prozent durchaus realistisch. Damit geht auch der Vorteil von deutlich kleineren Bauteilen einher. Die Fahrzeughersteller unterstützen wir dabei, immer fortschrittlichere Komponenten in immer kleineren Einbauräumen platzieren zu können.
3D-gedruckte Ersatzteile haben Sie schon ausgeliefert. Wie sieht der nächste Entwicklungsschritt aus?
Kovács: Für ein Projekt in Frankreich haben Kollegen aus Budapest und Reims gerade das erste pneumatische Steuerungsmodul ausgeliefert. Zwar handelt es sich ebenfalls um ein Retrofit-Projekt, aber eines mit großem Potenzial für das OEM-Geschäft. Die Nischenanwendungen lassen wir gerade hinter uns, so viel ist klar.
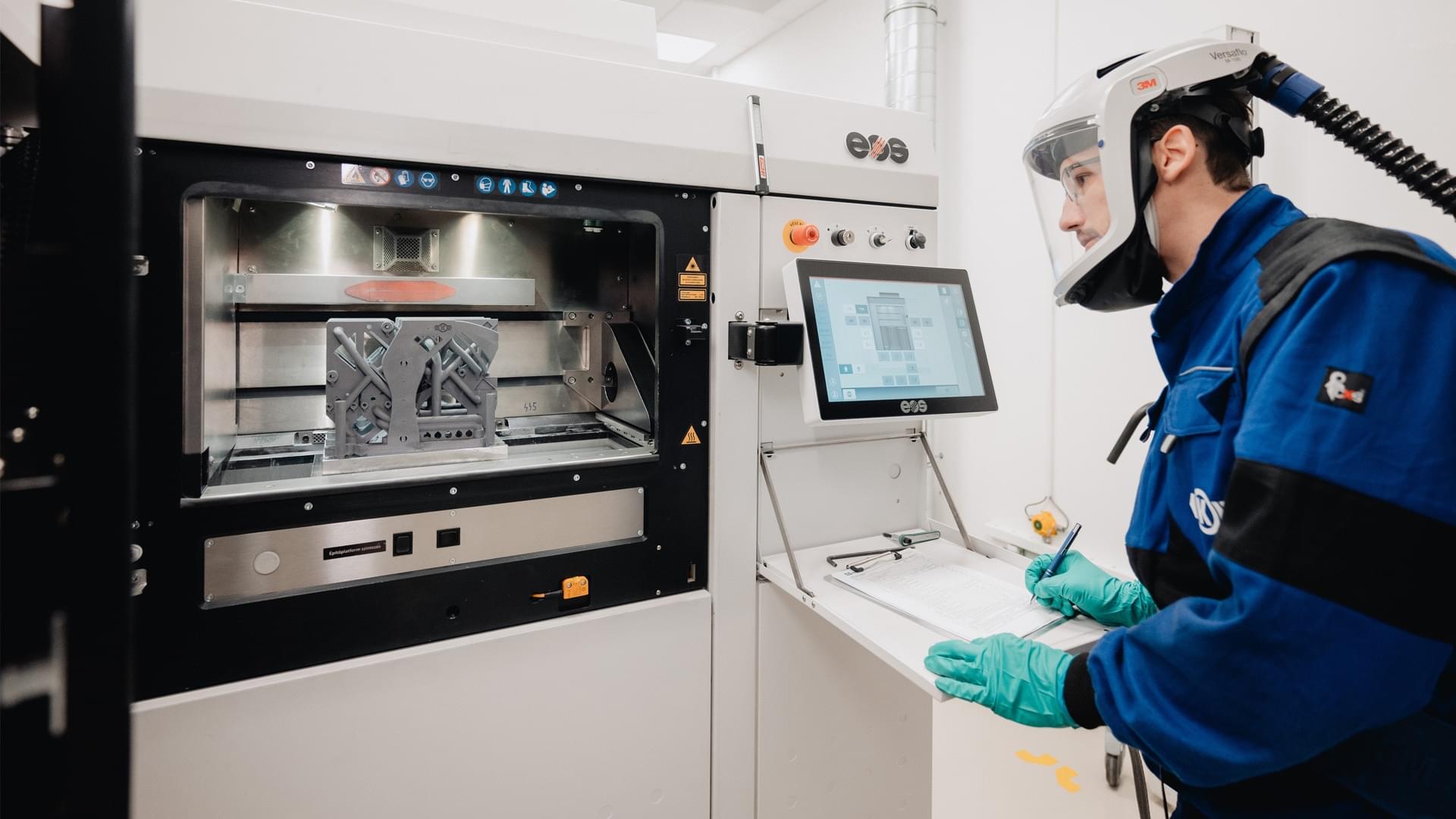
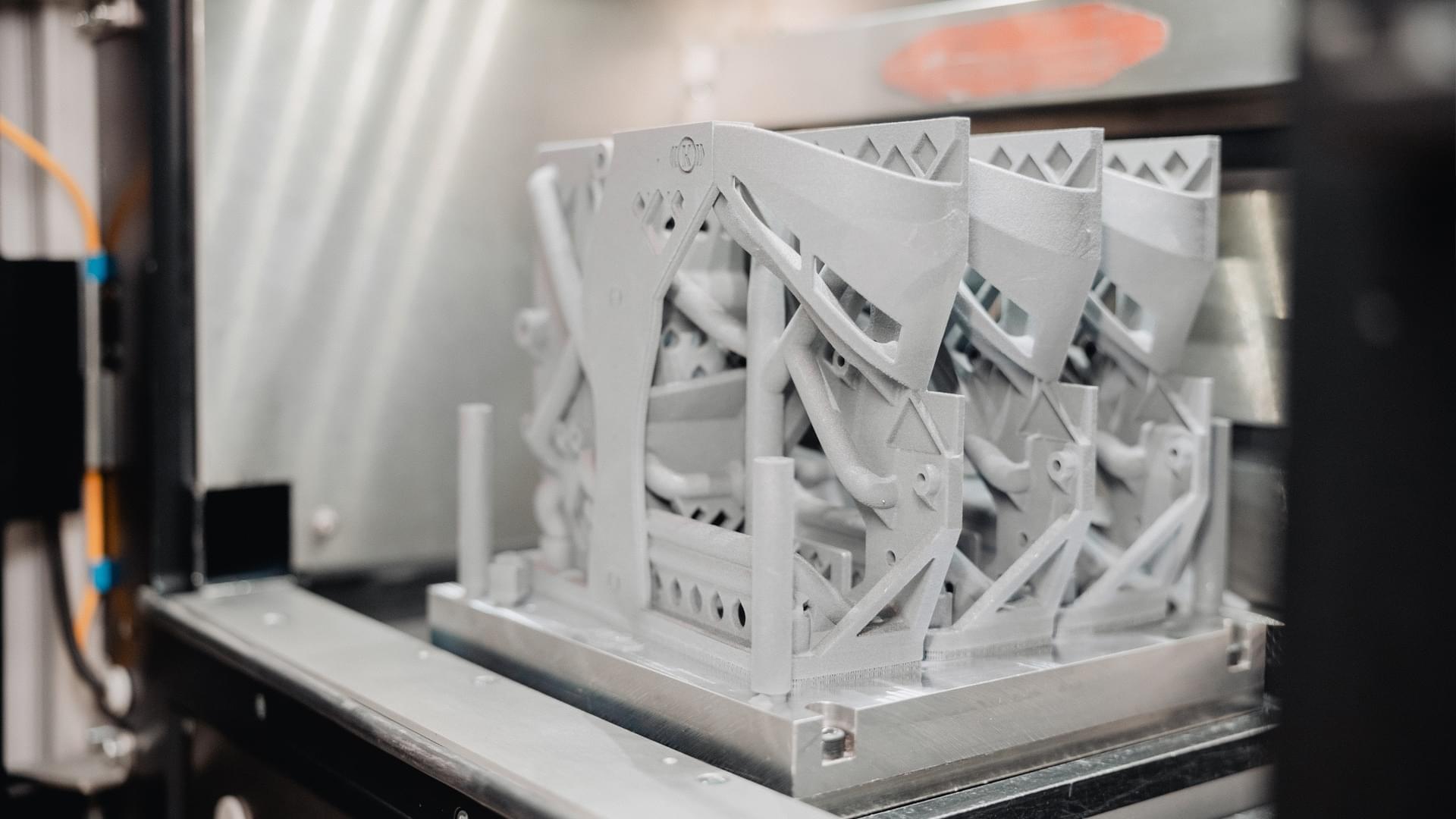
Abgespeckt zum reinen Funktionsträger
Für die Schienenfahrzeugbranche öffnet der industrielle 3D-Druck interessante neue Möglichkeiten. In Fahrzeugen der französischen SNCF wird Knorr-Bremse seine ersten additiv gefertigten pneumatischen Steuerungsmodule verbauen.
Die Steuerungsmodule kommen seit jeher massiv daher: Üblicherweise auf einer Aluminiumtafel als Trägersystem montiert kombinieren sie pneumatische und elektropneumatische Komponenten. Zahlreiche Bohrungen und Luftkanäle verbinden die Geräte untereinander. Ein Verteiler versorgt das Modul mit Druckluft. „Rein von der Funktionalität her betrachtet: Mit den Fahrzeugen ist einiges an überflüssigem Gewicht und Volumen unterwegs“, erklärt Clement Coquerel, Spezialist für industriellen 3D-Druck bei Knorr-Bremse France.
Leistung und Festigkeit wie die konventionellen Tafeln, aber 25 Prozent leichter sowie kleiner
Das Steuerungsmodul jedoch, das in einem Autorail à Grande Capacité, kurz AGC, der staatlichen Eisenbahngesellschaft SNCF verbaut wird, sieht ganz anders aus: deutlich kompakter und eher an ein leichteres Gussteil erinnernd. Viele Kanäle verlaufen nun unmittelbar zwischen den Komponenten anstatt wie früher auf unterschiedlichen Bauteilebenen.
„Leistung und Festigkeit entsprechen 1:1 den Werten des bisherigen Aufbaus“, sagt Coquerel. „Mithilfe der Additiven Fertigung haben wir ihn allerdings abgespeckt zum reinen Funktionsträger mit 25 Prozent Gewichtsersparnis gegenüber konventionellen Varianten.“ Montiert an gängigem Serienequipment durchliefen die Tafeln sämtliche Funktionstestsequenzen sowie Zulassungstests am Zug.
Info
Im sechsten Jahr im Dauereinsatz
Im Jahr 2018 hat sich die „Approval in Rail“-Arbeitsgruppe des Netzwerks Mobility goes Additive e.V. zusammengetan, um erstmals eine im sicherheitsrelevanten Bereich eingesetzte Bremskomponente für den Schienenverkehr im additiven Fertigungsverfahren herzustellen und in einem Fahrzeug zu verbauen. Das gewählte Pilotbauteil, eine Hängelasche, verbindet den Bremsbelaghalter mit dem Drehgestellrahmen. Während des Bremsvorgangs nimmt sie die auftretenden Zug- und Druckkräfte auf und leitet sie vom Bremsbelaghalter in den Drehgestellrahmen. Zuvor von Knorr-Bremse konventionell mittels Brennschneiden aus einem Stahlblech hergestellt, fiel die Wahl zur Additiven Fertigung auf den Werkstoff 1.4404. Verbaut im Sommer 2019 in einem DT4-Fahrzeug der Hamburger Hochbahn, befindet sich das Bauteil mittlerweile im sechsten Jahr im erfolgreichen Dauereinsatz.
Attraktive Einsatzszenarien in Niederflurfahrzeugen oder Hochgeschwindigkeitsanwendungen
Rund 700 AGC-Fahrzeuge setzt die SNCF in verschiedenen Ausführungen und als Diesel-, elektrische und Zweikraft-Varianten quer durch die Republik ein. „Die ersten gingen im Jahr 2004 in Betrieb. Jetzt ist mit dem Midlife-Overhaul genau der richtige Zeitpunkt, um neue Komponenten zu integrieren“, erklärt der Ingenieur. Zwei Steuerungstafeln sind pro Zug verbaut. In drei Zügen werden jeweils eine von ihnen durch die neue, 3D-gedruckte Variante ersetzt. Auf mindestens zwei Jahre ist der Feldversuch terminiert. Er ist SNCF-weit der erste mit einer neuen additiv gefertigten Komponente.
Noch handelt es sich um ein Retrofit-Projekt, doch eines, das auf Dauer ein solches nicht bleiben soll. „Wir wollen mit dem Feldversuch den Nachweis antreten, dass sich die 3D-gedruckten Tafeln künftig mindestens genauso gut auch in Neufahrzeugen verbauen lassen“, blickt Coquerel über den Tellerrand des Projekts hinaus.
Obendrein gehe es auch um Antworten auf die Frage, welche weiteren Komponenten am Zug sich im Sinne von reduziertem Gewicht und Volumen 3D-gedruckt optimieren lassen. „Attraktive Einsatzszenarien können wir uns zum Beispiel für die engen Einbauräume in Niederflurfahrzeugen oder in zukünftigen Hochgeschwindigkeitsanwendungen sehr gut vorstellen.“