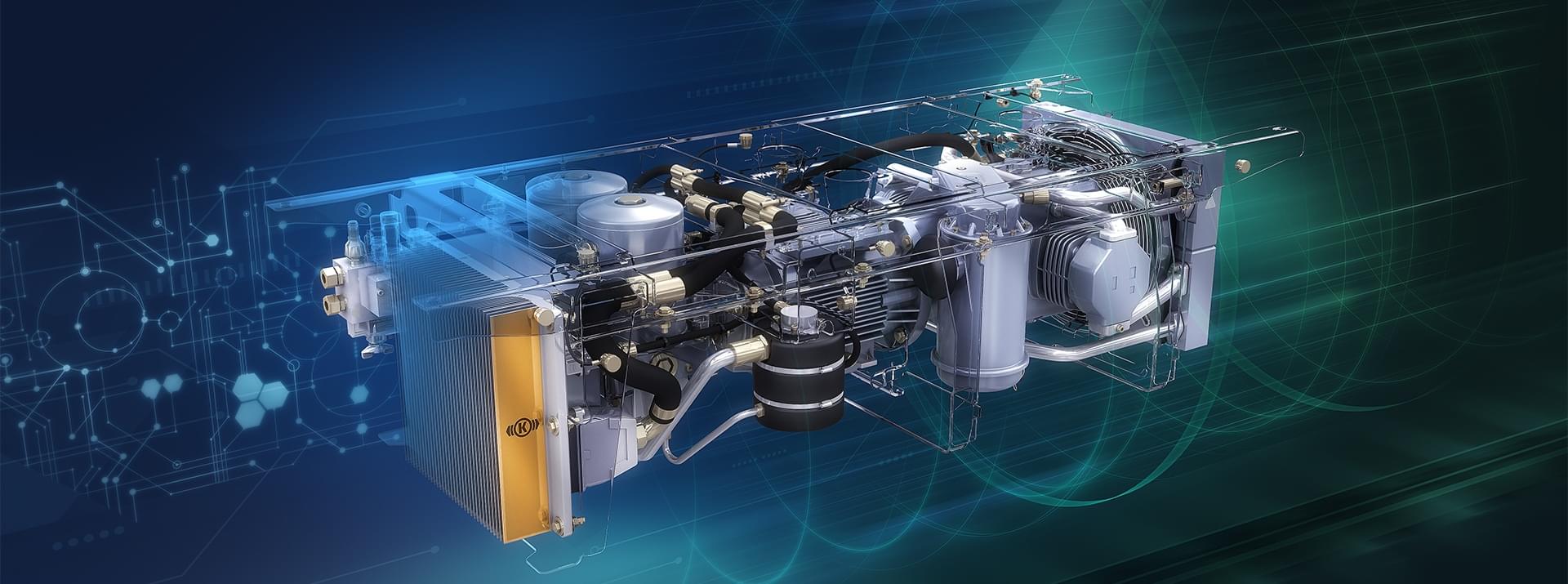
Die Lärm- und Gewichtsreduzierung bei Schienenfahrzeugen gewinnt zunehmend an Bedeutung. Die AirSupply Smart setzt hierbei neue Maßstäbe. Dank intelligenter und adaptiver Funktionen sowie einer, durch innovative Entwicklungsmethoden optimierten Schallauslegung des Kompressors , können bisher für einen offenen Kolbenkompressor unerreichbare Schallziele realisiert werden.
Kontakt
80809 München
Deutschland
carina.smid@knorr-bremse.com
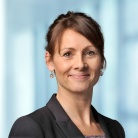
Frequenzumrichter öffnet Tür für adaptive Steuerung und ermöglicht so Schall- und Gewichtsreduzierungen
Im Bereich der Luftversorgung von Schienenfahrzeugen findet gerade ein durch die AirSupply Smart vorangetriebener Paradigmenwechsel statt: Aus einer bislang im Start-Stopp-Modus betriebenen Komponente ist ein intelligentes System mit einem Frequenzumrichter als zentrales Antriebs- und Steuerungsorgan entstanden. Der Umrichter ermöglicht erstmals ein Drehzahl- und damit Leistungsmanagement unabhängig vom Versorgungsnetz des Zuges. Die AirSupply Smart vereint dabei mehrere Funktionen auf eine Funktionseinheit, vereinfacht dadurch das Gesamtsystem und kann durch eine adaptive Steuerung verschiedenste Vorteile erzielen.Ein Beispiel hierfür stellt der “Boost Mode” dar. Bei besonders hohen Luftbedarfen kann der Frequenzumrichter die Kompressord rehzahl erhöhen, um mit der gesteigerten Förderleistung Aufrüstzeiten zu verkürzen. In kritischen Situationen wirkt sich dies unmittelbar auf die Betriebsqualität eines gesamten Nahverkehrsnetzes aus: Verlassen beispielsweise an einer zentralen Umsteigestation ein Großteil der Passagiere auf einmal das Fahrzeug, weshalb die Luftfederung hohe Verbräuche aufweist, kann die erhöhte Lieferleistung die Fahrbereitschaft beschleunigen. Durch die Überhöhung der Lieferleistung, dem „Boosten“, genügt in vielen Fällen, ohne Abstriche bei der Versorgungssicherheit, die Verwendung eines kleineren Kompressors.Dieses sogenannte „Downsizing“ trägt wiederum nicht nur zum reduzierten Gewichts- und Platzbedarf bei, sondern auch zur erheblichen Verringerung von Lärmemissionen. Ein kleinerer Kompressor bedeutet schließlich weniger Geräuschbelastung. Des Weiteren gehen mit dem Ansatz ökologische Vorteile einher: Wo weniger Masse beschleunigt werden muss, reduziert sich der Energieverbrauch des Zuges. Wo geringere Lärmemissionen verursacht werden, sinkt die Lärmbelastung der Umwelt. Ein zusätzlicher Nutzen entsteht, da nun nicht mehr der Spitzenbedarf die Kompressorgröße bestimmt, sondern somit der Kompressor im Normalbetrieb in seinem optimalen Betriebspunkt läuft.Einen weiteren Vorteil der adaptiven Steuerung beschreibt der „Silent Mode“. Durch gezielte Drehzahlreduzierung in Situationen mit geringem Luftbedarf können niedrige Schallwerte erreicht werden. Der Modus unterstützt Bahnbetreiber dabei, strenger werdende Lärmschutzvorgaben einzuhalten und besonders sensible Umweltbereiche zu schützen - beispielsweise beim nächtlichen Abstellen von Zügen in Wohngebietsnähe oder auf Bahnhöfen. Der Komfort-Effekt des „Silent Mode“ ist bemerkenswert, wie das Beispiel am VV120T-Kompressor zeigt: Die Drehzahl geschickt angepasst, lässt sich seine Schalleistung um bis zu 75 Prozent senken. Mit der Drehzahlregulierung ist die AirSupply Smart in der Lage, den bisher nur aufwendig zu lösenden Zielkonflikt aus Förderleistung, Schallkapselung und Kühlluftstromluftstrom im Kompressor zu entschärfen: Wo weniger Schall entsteht, lässt sich an der Einhausung sparen. Wo weniger Schallkapselung nötig ist, ergeben sich Potenziale zur Vereinfachung des Kühlkonzepts, die wiederum die Komplexität der Luftversorgungsanlagen verringert.Aber nicht nur das Drehzahlmanagement macht das Gesamtpaket attraktiv. Mit dem Frequenzumrichter ergeben sich auch bedeutende Vorteile bei der Integration der Anlage ins Gesamtsystem. Für die Elektroingenieure des Fahrzeugs ist der Kompressor eine komplizierte Komponente. Seine Drehungleichförmigkeiten und hohen Anlaufströme belasten das 3-Phasen Versorgungsnetzes des Zugs erheblich. Der Hilfsbetriebeumrichter (HBU) auf dem Fahrzeug muss die nötigen Leistungsreserven bereithalten und ist dementsprechend überdimensioniert. Zusätzlich ist ansteuerseitig sicherzustellen, dass das Bordnetz nicht etwa durch den gleichzeitigen Anlauf mehrerer Kompressoren überlastet wird. Dies alles ist mit entsprechenden Kosten und Aufwand verbunden. Die geschickte Lösung: Der Frequenzumrichter in der Anlage puffert die Anlaufströme und ist zudem in der Lage, die Gleichspannung des “HBU” direkt zu verarbeiten. Damit entfällt der Kompressor als 3-Phasen-Verbraucher komplett und die entfallenen Wechselrichterstufen im HBU erhöhen dessen Energieeffizienz.Beim „Pantograph Mode“ handelt es sich um ein weiteres Feature mit direktem Effekt auf die Systemkomplexität des Fahrzeugs. So sind viele elektrisch betriebenen Fahrzeuge neben dem „Hauptluftkompressor“ mit einem batteriebetriebenen Hilfsluftkompressor ausgerüstet, um das Anheben der Pantographen im drucklosen Fahrzeug zu ermöglichen. Im „Pantograph Mode“ wandelt der Frequenzumrichter den Gleichstrom aus der Fahrzeugbatterie in Drehstrom um und betreibt den Kompressor mit reduziertem Anlaufstrom sowie niedrigerer Drehzahl. Der damit einhergehende geringere Leistungsbedarf ermöglicht einen kurzfristigen Betrieb des „Hauptluftkompressors“ aus der 110-Volt-Fahrzeugbatterie, ohne diese zu überlasten. Beim hergestellten Kontakt des Pantographen zur Oberleitung wechselt die Steuerung in den klassischen Auffüllmodus. Ein ergänzender Hilfsluftkompressor ist somit nicht mehr nötig, die gesamte Baugruppe kann entfallen, mit allen daraus resultierenden Vorteilen für Platzbedarf, Gewicht und Wartungskosten.
Auch hinsichtlich innovativer digitaler Features zeigt das Konzept seine Stärken. Von Grund auf als durchdachte Plattform konzeptioniert, ist der Frequenzumrichter bereits mit den nötigen Schnittstellen ausgestattet, um neue Funktionen per Software-Update ergänzen zu können. Schon heute überwacht ein Condition-Monitoring-Paket die wesentlichen Systemfunktionen und meldet etwaige Funktionseinschränkungen. Fehlerfrüherkennung, Vermeidung von schwerwiegenden Folgefehlern und Reduktion von Wartungs- sowie Reparaturaufwendungen sind nur einige der sich positiv auf die Betriebskosten der Anlage auswirkenden Vorteile. Die neue Luftversorgung ist dabei in der Lage Daten aus bis zu acht weiteren Sensoren zu verarbeiten, auch für anspruchsvolle Diagnoseaufgaben wie Ölstandüberwachung oder Taupunktmonitoring.Zudem entstehen Synergieeffekte, da sich bereits eine vorhandene bahntaugliche Elektronik für das Monitoring nutzen lässt. Weder sind zusätzliche Schnittstellen oder Gehäuse noch zusätzliche Validierung der Hardware wie EMV-Tests zur elektromagnetischen Verträglichkeit sowie Schock- und Vibrationstest nötig.Ein weiteres Beispiel für die flexible modulare Funktionserweiterung stellt der, in der neuesten Kompressorgeneration von Knorr-Bremse zum Einsatz kommende, elektrisch angesteuerte Lüfter dar. In konventionellen Anlagen wird der Lüfter starr auf der Welle verbaut. Die Ansteuerung des E-Lüfters erfolgt ohne zusätzliche Steuerelektronik direkt aus dem Umrichter. Die nötigen Ein- und Ausgänge sind Teil des Konzepts, wodurch die Steuer-Software problemlos integriert werden kann.Aus ökologischer Sicht ermöglicht die adaptive Anpassung an Betriebsbedingungen und Leistungsanforderung des Kompressors erhebliche Vorteile hinsichtlich Gewichts und Lärmemission der Luftversorgungsanlage sowie reduziertere Komplexität, Materialverbrauchs, Einbauraums und reduzierter Lebenszykluskosten.
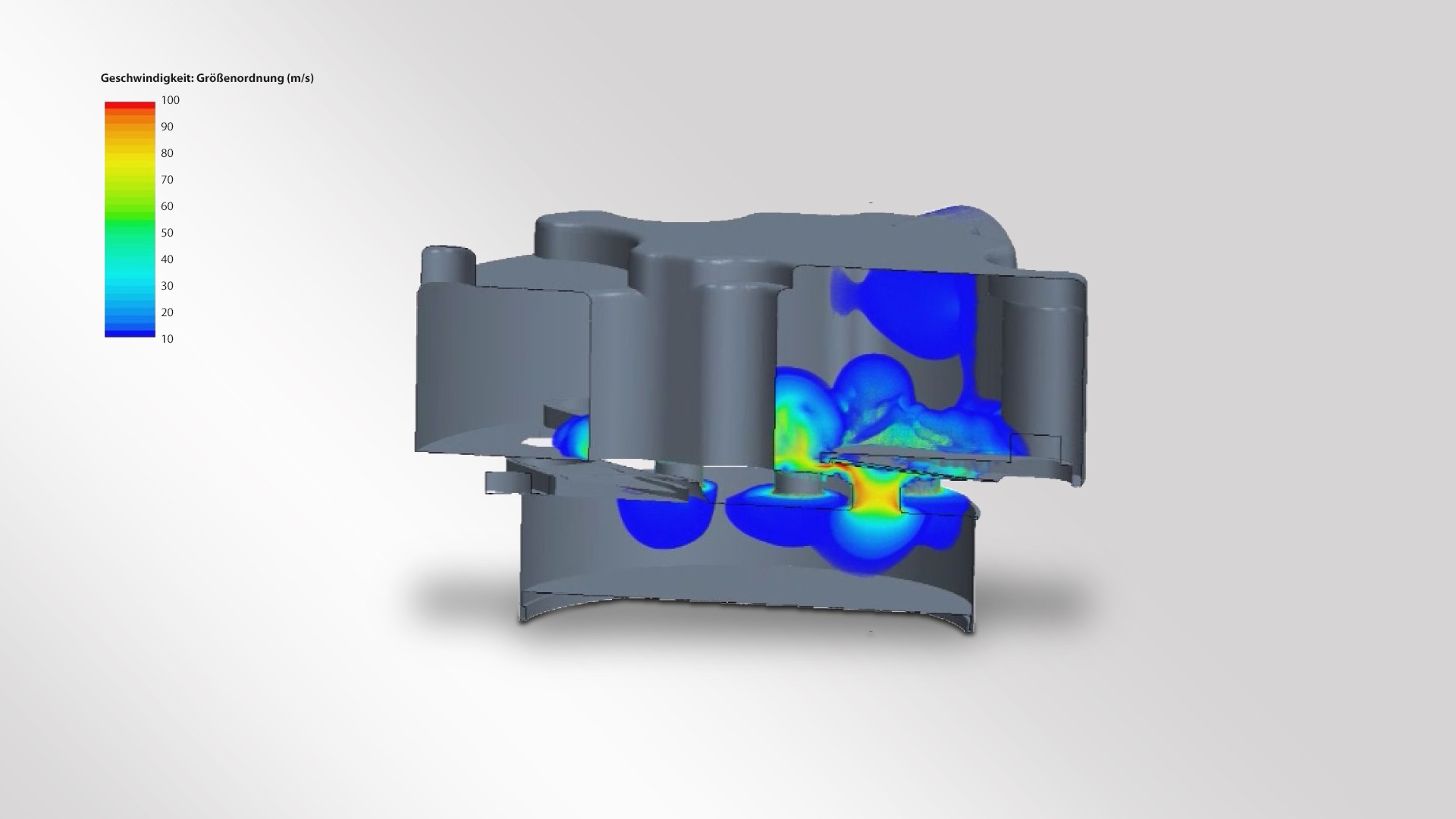
Smarte Entwicklungsmethoden als Wegbereiter für den schalloptimierten Kompressor
Heutige Projekte erfordern teilweise extrem niedrige Schallwerte, die selbst mit dem gewaltigen Hebel des „Silent Mode“ respektive situativer Drehzahlabsenkung nicht zu schaffen sind. Zusätzlich zu den ausgeklügelten Funktionen sind deshalb weitere Optimierungen am Kompressor erforderlich, um die strengen Vorgaben des Lärmschutzes zu erfüllen. Durch die geschickte Verbesserung schallemittierender Kompressor-Komponenten wie Ventile, Kolben, Lager oder Fänger lässt sich deren Körperschall und Lärmbelastung im und außerhalb des „Silent Mode” weiter reduzieren. Die involvierten Phänomene sind jedoch komplex und von Wechselwirkungen gekennzeichnet. In welchen Betriebszustand strahlt welche Komponente welche Schallkomponente ab? Mit herkömmlichen Schallmessungen stößt man bei dieser Analysemethode sehr schnell an die Grenzen. Deshalb gehen die Ingenieure bei Knorr-Bremse einen neuen Weg. Im ersten Schritt müssen die schallerzeugenden Bauteile exakt lokalisiert werden. Die Kombination verschiedener Simulationsmethoden wie Modalanalysen, harmonische Analysen, explizite Struktursimulationen sowie Strömungssimulationen ermöglichen die effiziente Identifikation der relevanten Schallquellen.
Im nächsten Schritt werden Optimierungsmaßnahmen definiert und geprüft. Einfache Verbesserungsversuche an einzelnen Komponenten greifen hier zu kurz, da die Optimierung an einer Stelle die Verschlechterung an drei anderen Komponenten verursachen kann.Smartere Methoden sind gefragt, wie zum Beispiel die Modalanalysen auf Basis der Finite?Elemente-Methode (FEM).Diese bieten eine Alternative und vor allem im Tagesgeschäft eine auch darstellbare Option, um die Werte der Eigenfrequenzen schallemittierender Bauteile über ihre CAD-Daten (Computer Aided Design) zu simulieren. Für die nicht weniger wichtige Bestimmung der Schwingungsamplituden sind wiederum explizite FEM-Simulationen notwendig, um die Amplituden im Zeitbereich zu extrahieren. Nach einer Transformation in den Frequenzbereich ermöglichen diese dann eine quantitative Anregung des Modalmodells.Auf diesem Weg lassen sich nun verschiedene Modifikationen und deren Auswirkungen auf die Schallemission simulieren und virtuell testen. Die effizienteste Optimierung wird im dritten Schritt konstruiert und validiert. Um beim Beispiel des Ventilfängers zu bleiben: Beim Resultat in Form des Silent Valve Systems (SVS) kommt nun eine Dämpfung des Ventillamellenaufschlag auf dem Fänger zur Anwendung, die nurmehr den obligatorischen Hardwaretest zur finalen Bestätigung durchlaufen muss. Analog lassen sich weitere schallbeeinflussende Komponenten wie etwa Lüfterhutze oder Kolbenringe konstruktiv optimieren – und auf diese Weise die Lärmemissionen der Luftversorgungsanlage Schritt für Schritt minimieren.Durch die Kombination des adaptiven Drehzahlmanagements und der Optimierung des Kompressors wurde erreicht, dass die AirSupply Smart VV90-T als der leiseste Kolbenkompressor dieser Baugröße gilt, der von Knorr-Bremse ohne aufwändige Schallkapselung bisher auf den Markt gebracht wurde. Ein herkömmlicher Kompressor im vergleichbaren Leistungsbereich wird vom menschlichen Ohr doppelt so laut wahrgenommen wie die AirSupply Smart VV90-T im „Silent Mode“.
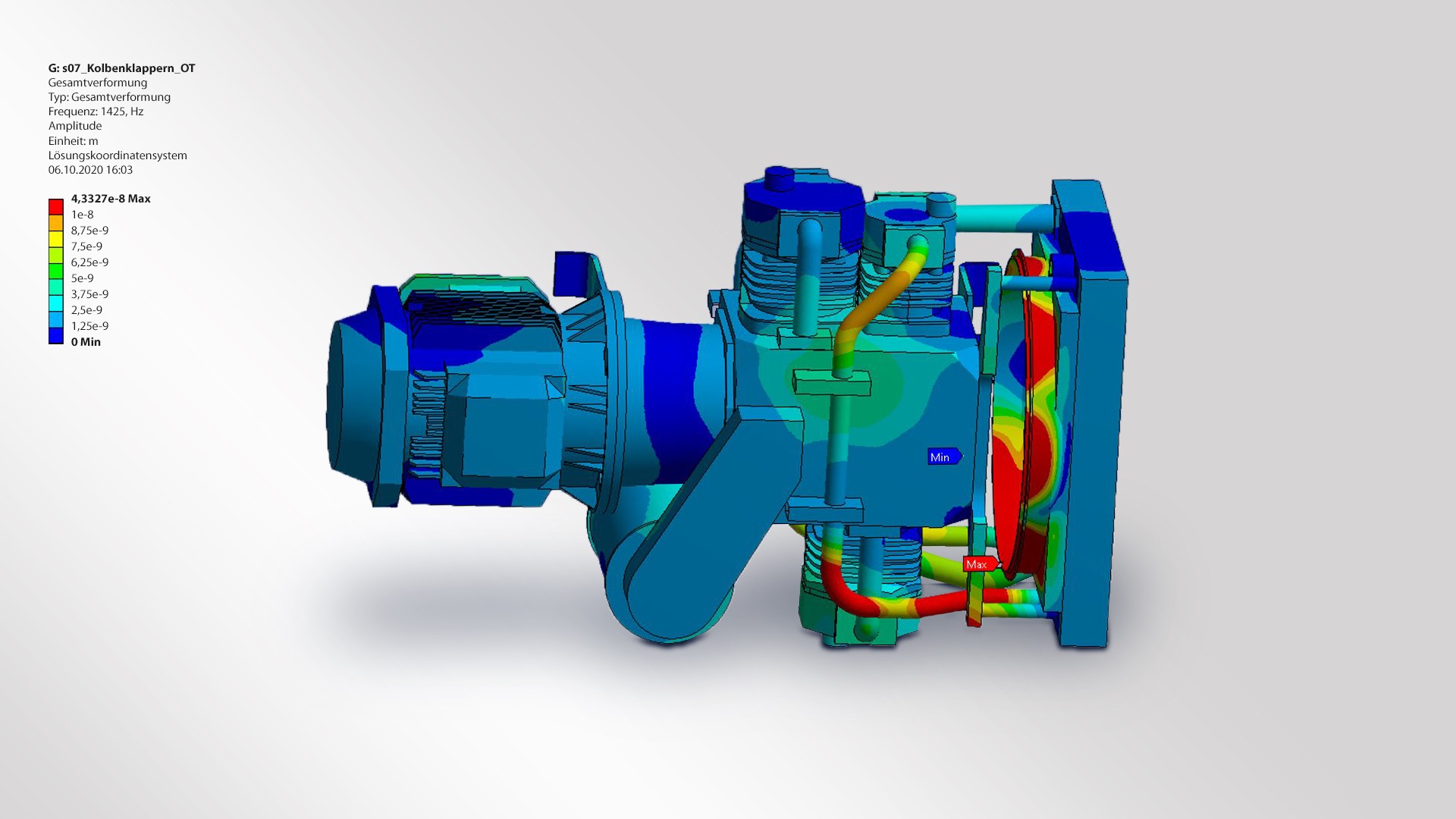
Conclusio
Das Ergebnis zeigt, dass das Potenzial zur Reduzierung von Emissionen im Bereich der Luftversorgungssysteme von Schienenfahrzeugen noch nicht ausgeschöpft ist. Es besteht weiterhin Raum für Innovationen, um die Nachhaltigkeit und Lärmreduzierung weiter voranzutreiben. Die AirSupply Smart VV90-T konnte sich jedoch durch ihre adaptive Ansteuerung und die Anwendung effektiver Entwicklungstechniken als der leiseste bisher je von Knorr-Bremse gelieferte Kolbenkompressor ohne Schallkapsel in dieser Leistungsgröße positionieren.
Autoren: Dr. Martin Schmid; Martin Schmid; Ludwig Obermaier